What Are the Benefits of Adding IoT to Laser Cutting?
While laser cutting has many advantages, it can also be challenging to implement. High initial costs, safety concerns and the need for specialized training can stop manufacturers without the necessary funds and experience from capitalizing on its potential. Internet of Things (IoT) functionality in the laser-cutting process can help businesses overcome those barriers.
IoT is an umbrella term covering electronics that can wirelessly communicate with one another in real-time. Smart home devices are some of the most familiar examples, but many industrial-grade, manufacturing-specific IoT solutions exist. Here’s how bringing that connectivity to laser cutters can benefit manufacturers.
Improved Safety
One of the most significant advantages of IoT connectivity in the laser-cutting process is its impact on safety. Lasers can be dangerous, causing amputations and even death when employees get in their way. This equipment can also emit hazardous fumes, presenting less noticeable but still serious risks.
The IoT helps by creating distance between employees and these hazards. Workers can operate IoT-enabled laser cutters remotely without losing any precision. Consequently, they can run this equipment continuously without worrying about amputation or fume-related risks.
Protecting employees’ well-being is enough to warrant these safety improvements on its own, but they also have tangible business benefits. Fewer injuries mean less unexpected downtime and fewer losses from workers’ compensation payments. Those savings can justify the higher costs of implementing IoT-connected laser-cutting equipment.
Real-Time Operating Data
IoT in laser cutting also lets equipment operators capitalize on real-time data. Connected sensors can gather data on operational factors like temperatures, cutting speed, material thickness, beam power and more and transmit it to workers in real-time. This insight enables more effective control.
Standardization is key to maximizing manufacturing efficiency, but businesses must realize that some fluctuations are inevitable. In light of that unpredictability, employees must be able to adjust to these changes, which the IoT’s visibility enables. When laser operators can see changing conditions in real-time, they can adapt to them to maintain productivity and accuracy.
An IoT sensor may reveal that a laser isn’t cutting material as quickly as it should, informing the operator to temporarily dial up the beam’s length, temperature or pulse rate. Alternatively, warnings about warping or excessive temperatures can tell employees to dial these factors back. By adapting to these changes, workers prevent errors and maximize productivity.
Predictive Maintenance
Another important benefit of IoT in the laser-cutting process is that it enables predictive maintenance. This practice uses IoT sensors to monitor maintenance-related factors like temperatures, mechanical stress and vibrations and alert employees when these parameters suggest the equipment needs repair soon.
Basing maintenance stops off these data-based alerts instead of schedules or running equipment to failure has many benefits. Since these timely warnings let employees fix laser cutter issues before they become larger problems, predictive maintenance lowers repair costs by 25% on average. It also prevents unnecessary maintenance stops, leading to a similar improvement in uptime.
These savings are particularly important for laser cutters, which often carry high upfront expenses. Implementing predictive maintenance allows manufacturers to reduce their laser cutters’ operating costs, making up for their purchase price in less time.
Flexible Automation
IoT connectivity can also enable flexible automation in laser cutting. Automated cutting processes are more efficient but can be challenging to implement effectively because they often mean sacrificing adaptability. The IoT provides a solution by letting automated systems respond to real-time data from upstream processes.
IoT-connected automated laser cutters can communicate with other IoT equipment earlier in the manufacturing process. They can then receive data on any unexpected delays, material irregularities or other disruptions and adjust accordingly to compensate for these unusual situations. That way, variability elsewhere in the production line won’t disrupt automated laser-cutting processes.
When automation becomes more flexible, it becomes a more practical solution for manufacturers. Automating laser cutting, in turn, helps organizations overcome experience barriers to the process. Manufacturers won’t require employees to have as much specialized training, making it easier to capitalize on laser cutting’s benefits.
Enhanced Inventory Management
Laser cutting can also benefit from IoT implementation outside of the laser cutter itself. Inventory management IoT solutions are an excellent example. By boosting inventory visibility and efficiency through the IoT, manufacturers can ensure a smoother laser-cutting workflow.
IoT tracking solutions in material inventories can provide real-time updates on things like upcoming parts’ composition, thickness and other factors that impact cutting. With this information in hand, laser cutter operators or automated systems can adjust ahead of time to account for any irregularities or changes. That way, they can ensure they cut the material as quickly, safely and accurately as possible.
Adapting to unique material qualities can significantly impact productivity. Some manufacturers have increased output tenfold after adjusting their cutting processes to particular material needs.
Better Quality Control
Similarly, IoT connectivity in post-cutting quality control can improve the laser-cutting process. IoT technology in quality checks can identify where errors stem from to inform relevant, effective changes to prevent future mistakes.
Over time, IoT-connected quality control machine vision systems will gather data on defects, revealing trends like which types of errors are most common. Feeding this information into artificial intelligence (AI) analytics engines lets manufacturers see what’s likely behind their most common errors. Once they know the source of the problem, they can address the issue at its roots to prevent these defects in the future.
These ongoing improvements let manufacturers minimize time losses from rework and expenses from wasted materials. As a result, they’ll improve their profit margins, accelerating their laser-cutting systems’ return on investment. Preventing defects can also boost customer satisfaction and loyalty.
IoT Improves the Laser Cutting Process on All Fronts
These six benefits make the laser-cutting process safer, more accurate, reliable, efficient and cost-effective. Those improvements make laser cutting a better investment, even for manufacturers who previously couldn’t justify its expense or necessary training. In turn, more facilities can experience the speed and accuracy of laser cutters in their production lines.
Like with laser cutters themselves, implementing IoT systems can take time and money. However, as these advantages highlight, the results will compensate for those disruptions over time. As the industry becomes increasingly competitive and demands rise, manufacturers cannot afford to overlook the IoT’s benefits.
Comments (0)
This post does not have any comments. Be the first to leave a comment below.
Featured Product
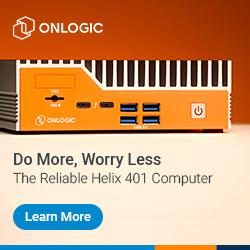