How LiDAR Is Paving the Way for Industry 4.0
Industry 4.0 is sweeping across the manufacturing industry. Data-driven processes and technologies hold substantial promise for manufacturers, but implementing them successfully can be challenging. Light detection and ranging (LiDAR) technology can help.
LiDAR doesn’t typically appear on disruptive Industry 4.0 technologies lists, but it may serve a foundational role in preparing facilities for this transition. Here’s a closer look.
What Is LiDAR?
LiDAR uses pulsed lasers to measure distances, often combining these readings with GPS systems and other data-recording technologies. It works similarly to radar and sonar in that it measures physical space by bouncing signals off objects. However, using a laser instead of radio waves or sound makes it more accurate and precise in many situations.
This technology has been around for a while, but recent advancements have made it more compact, accessible and versatile. It was once the exclusive domain of scientific research and vehicle navigation, but it’s now available to manufacturers.
LiDAR Applications for Industry 4.0
LiDAR’s real-time, three-dimensional information can serve many uses for Industry 4.0 facilities. Here are a few of its most significant applications.
Highlighting Bottlenecks
One of the primary goals of Industry 4.0 is to make manufacturing more efficient, and LiDAR scanning enables these process improvements. These scanners fire up to 1 million pulses per second, making them an ideal solution for monitoring repetitive movements. Using LiDAR to monitor workflows provides plenty of data on how people, machines and products move throughout them.
Artificial intelligence (AI) algorithms, a foundational Industry 4.0 technology, can then analyze this information to highlight inefficiencies. Factories can adjust as necessary to become more efficient. This optimization may not be possible without AI, and AI is only useful with enough relevant data, which LiDAR provides.
Streamlining Facility Improvements
Similarly, LiDAR scans can help facilities understand their current situation to inform faster, more effective physical improvements. Many manufacturers are switching to sustainable business practices and reworked workflows, which may require new or altered infrastructure. LiDAR can provide the necessary surveying for these projects quickly and accurately.
Traditional surveying techniques are slow and, at times, unreliable. LiDAR uses precise, fast lasers, so it can make the process far more accurate and less time-consuming. Manufacturers can then get started on expansion or renovation quicker and with greater confidence.
Guiding Autonomous Mobile Robots
Embracing Industry 4.0 also means increasing automation. Autonomous mobile robots (AMRs) will become more common across factory floors, but they must be able to navigate safely to be effective. LiDAR can provide the navigation they need.
Many self-driving car companies rely on LiDAR for its precise, fast measurements of the world around it. Navigating roads is still challenging, but these benefits translate well to more predictable factory and warehouse floors. LiDAR sensors working together with cameras help AMRs drive safely through the facility without bumping into anyone or anything.
Automating Quality Control
LiDAR could also help manufacturers automate the quality control process. Robots with LiDAR sensors can find defects earlier without human intervention, increasing automation and efficiency.
These sensors’ precision helps them find product defects that humans may easily miss. They fire multiple pulses a second and can detect these errors quickly, ensuring quality control doesn’t create bottlenecks. Automating this final step in production opens the door for Industry 4.0 facilities to develop fully automated, connected workflows.
LiDAR Technology Unlocks Industry 4.0’s Potential
LiDAR’s potential in Industry 4.0 often goes overlooked, but it’s substantial. Implementing LiDAR in these areas lets manufacturers enable more cutting-edge technologies and processes. These improvements could provide a crucial stepping stone toward the data-driven future of manufacturing.
Comments (0)
This post does not have any comments. Be the first to leave a comment below.
Featured Product
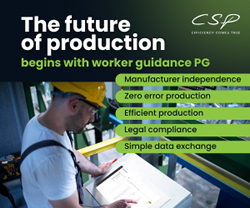