How VR and AR are Creating the Next Generation of Welders
The combined augmented and virtual reality market was worth approximately $16.92 billion at the end of 2021, while it’s expected to peak at $105.67 billion by 2028.
But what will power this impressive growth? Primarily, it will be driven by the widespread adoption of AR and VR technologies across a broad range of applications, including the teaching of specialist skills such as welding.
But how exactly are AR and VR technologies helping to create the next generation of welders? Let’s find out!
The Importance of Technology When Recruiting and Training Welders
Currently, it’s thought that there are nearly 420,000 employed welders in the U.S. These jobs are available across a wide range of industries too, from engineering and automotive manufacturing to power generation and offshore oil and gas production.
Welding is also a specialist skill, with many of those employed in the U.S working in jobs where it’s the only necessary part of the function.
Like many traditional trades of this type, welding is currently experiencing a considerable operator shortage. To this end, an employer with a single welding position may receive up to 100 applications on average, creating significant challenges in terms of recruitment and screening processes.
Certainly, it can be hard to effectively evaluate the skills of respective candidates in a time-efficient manner, especially when dealing with a huge number of applications.
Not only this, but the process of successfully gaging applicants’ technical skills often requires them to perform an actual welding task. This may incur potential safety risks in some instances, while requiring the use of precious resources such as wire, gas and (most importantly) time.
Even once you’ve identified and hired the best candidate, you’ll still have to provide relevant training depending on the experience of the employee in question.
This will command further time and financial resources, while raising significant health and safety challenges that need to be tackled. The level of potential risk involved could also lead to much slower training and development, which is a huge problem given the shortage of welders and the workload placed on each and every one.
Why Welding Simulators Resolves Both Issues
The good news is that both of these challenges can be overcome using welding simulation systems. These include VR systems and those that meld real-world settings with computer-generated imagery using AR technology, the latter of which is commonly used to create simulations that mimic real-time arc welding.
By replicating authentic job scenarios in a safe and virtual setting, it’s possible to both test and train welders effectively while simultaneously minimizing your long-term cost base.
Rather than committing fixed time and materials resources every time you want to screen or train an employee, for example, you can invest in a flexible software subscription system that covers a desired period of time.
This is certainly the case when using Soldamatic welding simulators, which ultimately enable you to cost-effectively test and certify more welders in considerably less time overall.
There are other benefits to using welding simulators too, many of which provide practical help to businesses that are struggling with a shortage of skilled welders.
For example, the augmented and intuitive training provided by welding simulators reduces learning time by approximately 51% when compared to traditional training. This ensures that new employees can develop the requisite skills much quicker, leading to an optimized workforce and improved productivity throughout the business.
Crucially, welding simulators have also precipitated an 84% reduction in accidents. This is an important consideration from the perspective of training and screening applicants, during which time you’ll often deal with nervous or inexperienced applicants or attempt to impart a specific or potentially complex skill.
Make no mistake; reducing the time and risk associated with training will also lower long-term operational costs, potentially contributing to a healthy bottom line even without an increase in revenues.
The Last Word - Creating Next Gen Welders Quickly and Effectively
From the perspective of individual employees and the next generation of welders, simulated learning programs are also highly advantageous.
Certainly, welding is a niche skill that demands manual dexterity, along with a keen attention to detail. Similarly, the quality of welding tasks relies on the operator’s travel speed, use of angles and arc position within the welding joint, and honing such skills can be difficult (and not to mention costly) using traditional training methods alone.
Welding simulators are extremely helpful in this respect, by seamlessly allowing for repetition and continual practice without incurring the time-consuming and costly practice of setting up a real workstation each and every time.
So, not only can the deployment of welding simulators help to expedite the development of a necessary skillset, but it may also create a new generation of welders who have benefited from improved levels of knowledge retention and are able to work to a consistently higher standard.
Of course, VR-inspired training systems work best when combined with some traditional methods. More specifically, trainers can deliver some relevant hands-on training pertaining to a particular skill, before utilizing a welding simulator to test the employee’s aptitude and ability to retain knowledge.
They can then provide instant feedback and accurate proficiency scores, which will lay the basis for future training and clearly identify any areas for improvement.
Comments (0)
This post does not have any comments. Be the first to leave a comment below.
Featured Product
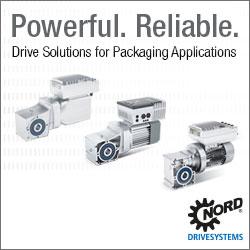