Embrace the edge to avoid unscheduled downtime
According to Arimo, manufacturers can deal with up to 800 hours of downtime per year. As unscheduled downtime is far more costly than planned downtime, it’s important that manufacturers have real-time information about their equipment and processes to avoid unexpected faults and failures. Here Johan Jonzon, CMO and Co-Founder of edge analytics platform developer, Crosser, explains how edge analytics provides instantaneous data to prevent unscheduled downtime.
One of the key metrics for process efficiency is overall equipment efficiency (OEE). This KPI is related to the availability, performance and quality of the production process. High OEE often means good revenue, low OEE indicates the need for optimization and improvements. Unscheduled downtime will dramatically affect availability and performance — drastically lowering the OEE.
Being aware of the real-time status of all equipment and processes is crucial to predicting the potential causes of downtime. Manufacturers who implement edge analytics will be equipped with the necessary data to make informed decisions about equipment and production to optimize processes and maintenance schedules.
Leverage the edge
Edge computing is computation that is done at or near the devices that are generating the data. Typically, the data collected from machines or devices would be sent straight to a local data center for storage and historical analysis. But now enterprises want to leverage that data using big data analytics and extensive cloud services. This causes some major concerns regarding security, latency, bandwidth, costs and reliability.
These concerns are magnified for facilities with a high number of devices transmitting data at the same time. Instead, edge analytics can form a bridge between the devices and the cloud or data center, providing a local source of processing and storage. On-premise analytics can collect and filter data, storing or sending it to the correct location based on abnormalities, business rules and algorithms. Only the necessary data is sent to the cloud or data center, enabling large savings in bandwidth and cloud service costs.
What’s more, the real-time ability at the edge can leverage automatic changes to production according to a pre-determined algorithm, or be evaluated by equipment operators and facility managers to make informed decisions.
Predict to prevent
There are several processes that the real-time integration and analysis of data can benefit. One example is condition monitoring, which involves monitoring a certain parameter of machinery condition, such as vibration or temperature, in which a change could indicate the development of a fault.
Condition monitoring can be used as part of a predictive maintenance strategy by running the condition data through pre-built predictive algorithms that can estimate when the piece of equipment might fail. This means maintenance work can occur in an organized way before the failure occurs either without the need to stop production or during planned downtime, which avoids the sudden and costly onset of unscheduled downtime.
According to a predictive maintenance report by Deloitte, adopting a predictive maintenance strategy can reduce breakdowns by 70 per cent and increase equipment uptime by 20 per cent.
Dedicated to data
An increasing number of manufacturers are adopting predictive maintenance strategies, as they allow systems to be maintained before failure occurs and run as long as possible without interruption.
An edge analytics strategy supports a predictive maintenance strategy, but it’s important that manufacturers choose a platform that is simple to integrate and operate. The Crosser Edge Node software acts as a real-time engine, and its unique architecture hides complexity from the user so that it can be easily used by existing personnel. The software allows manufacturers to collect data from any source, such as sensors or PLCs, and build automated workflows to transform, analyze, and act on the data. Data is then processed at the edge to enable actions based on advanced business rules or codes to be performed rapidly.
Long, and short, periods of downtime can be a costly reality, but can be minimized if manufacturers are informed on the real-time status of equipment and processes. Edge analytics allows the collection, integration and analysis of real-time data, enabling automatic changes to production while providing manufacturers with important data to make informed decisions and reduce unscheduled downtime.
To learn more about Crosser and its edge solutions, visit https://crosser.io/
About Crosser Technologies
Crosser is a Swedish software company with installations in over 20 different countries. We design and develop a Low-Code software platform for Streaming Analytics, Automation and Integration for any Edge, On-premise or Cloud. Our aim is to remove complexity, simplify development and to enable non-programmers to innovate faster with a dramatically lower total cost of ownership. Our vision is that there are enormous business opportunities for companies When Machines Talk (™).
The software is ideally suited for Enterprise customers of various Industrial verticals such as Process Industry, Manufacturing, Utilities and other asset rich verticals. The modular and flexible solutions enable many different applications, including Industry 4.0, Industrial IoT and next generation Hybrid Integration, also called Hyper Automation by Gartner.
Industrial customers include, SCA AB, Valmet Corporation, Novo Nordisk, Gebhardt, Clarebout Potatoes and RubbleMaster.
Crosser was included in the “Cool Vendors in IoT Edge Computing, 2018” report by Gartner, Inc. and was named among the Top 10 Smart Factory Solutions in Europe 2020 by the industry magazine Manufacturing Technology Insights.
Comments (0)
This post does not have any comments. Be the first to leave a comment below.
Featured Product
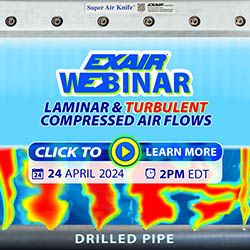