New Solutions for Materials Manufacturing Reduce Environmental Impact in Construction
Construction is historically an environmentally damaging industry. As the fight against climate change gains momentum, the sector must embrace more sustainable practices. Materials manufacturing is an easily overlookable but critical part of that transformation.
Many efforts to reduce construction’s environmental impact prioritize on-site improvements. While zero-emissions equipment and waste reduction strategies are crucial, sustainability is complex, involving far more factors than construction work itself. The manufacturers that produce building materials must also improve for the industry to become truly sustainable.
Material Manufacturing’s Role in Construction Sustainability
Construction is responsible for 38% of greenhouse gas emissions globally. Some of that comes from building operations after construction, but embodied carbon – emissions from the construction process – is a considerable part of it. Likewise, materials account for a significant portion of embodied carbon.
Manufacturing common construction materials typically involves considerable energy expenditure. Since most energy today comes from fossil fuels, that translates into substantial greenhouse gas emissions. As a result, 23% of global emissions come from steel, aluminum, and concrete alone. While not all of that goes to construction, much of it does.
Reducing construction’s carbon footprint means reducing embodied carbon, and much of that falls to material manufacturers. Thankfully, several new solutions have emerged for these manufacturers to improve their sustainability. Here are six possible ways material manufacturing can reduce construction’s environmental impact.
Using Recycled Materials in Concrete
One of the most critical materials to address is concrete. Cement – concrete’s main ingredient – is responsible for 8% of CO2 emissions, and concrete remains one of the most popular materials in the industry. One way manufacturers can reduce concrete’s carbon footprint is to incorporate recycled materials in its production.
Many plastics are easily recyclable, and manufacturers can use these as filler in concrete. Drying and pulverizing plastics creates a fine powder ideal for this application, and using more of it will reduce how much cement manufacturers use. Consequently, cement’s large carbon footprint doesn’t affect concrete’s footprint as drastically.
Alternatively, materials manufacturers can use old concrete from demolition rubble as an aggregate for mixing new concrete. This may provide more strength than plastics while still reducing demand for new cement.
Novel Cement Alternatives
Another way to mitigate cement’s carbon footprint is to replace it entirely. Manufacturers can transition to producing cement-free concrete instead, helping the construction industry move away from environmentally damaging materials. Several novel materials offer comparable strength to traditional concrete without its high carbon footprint.
Ferrock, a combination of iron dust, fly ash, metakaolin, and limestone, is one of the most promising alternatives. This material is five times stronger than cement, is far more flexible, and doesn’t carry cement’s environmental cost. Nearly all its components can come from recycled waste from standard construction processes.
The downside to these new materials is their limited accessibility, which also typically means high prices. However, as demand for green building materials rises, these concerns will fade, and cement alternative production can scale up.
Hydrogen-Powered Steel Mills
Some solutions have less to do with the actual material in question and more with its production. Metals like steel are near-endlessly recyclable, but smelting them – even from recycled materials – involves considerable energy consumption. Some steel mills have addressed this by transitioning to clean energy like hydrogen.
In 2021, a Swedish metal company became the first to produce fossil fuel-free steel, using hydrogen as its sole power source. Since hydrogen produces no carbon emissions when it burns, it’s an ideal alternative to natural gas, coal, and other fossil fuels. While many facilities today use fossil fuels to extract pure hydrogen, this company relied on green hydrogen.
Green hydrogen uses renewable energy sources like wind and solar to power the hydrogen extraction process. That way, the fuel is entirely emissions-free, from production to end-use. Considering steel accounts for 9% of CO2 emissions, transitioning to green hydrogen could substantially impact construction’s sustainability.
Material Localization
Material origins are another easy-to-overlook factor that plays into embodied carbon. Transportation is responsible for 29% of greenhouse gas emissions in the U.S., so transporting raw materials across vast distances is environmentally harmful. Relying on more local sources can help material manufacturers reduce these emissions.
If manufacturing processes happen closer to the mines where their raw materials come from, they’ll require less transportation. This will both improve costs and reduce transport-related emissions. Naturally, not every facility can be close to every type of mine, so manufacturers must also consider what’s available in their area.
Facilities could analyze what resources are closest to them to find what materials they could produce to minimize transportation emissions. This will likely result in initial disruption and increased specialization, but the environmental benefits could be substantial.
Cross-Laminated Timber
Another alternative with promising environmental benefits is cross-laminated timber (CLT). CLT involves gluing layers of wood together at alternating 90-degree angles. This lamination technique makes the lumber far stronger than traditional planks, making it a potential replacement for concrete and steel structures.
While logging isn’t emissions-free, it generates far less greenhouse gas emissions than steel or concrete production. Trees can also regrow quickly enough to be a renewable resource, especially if manufacturers source from sustainable tree farms. Wood is also a natural carbon sink. One five-story lumber building can store 180 kilograms of carbon per square meter.
CLT lets manufacturers provide those environmental benefits while avoiding wood’s traditional weaknesses. Producing this material would help encourage the construction industry to embrace more sustainable building practices.
Nanotechnology
Nanotechnology, which deals with materials less than 100 nanometers in size, also shows environmental potential. At this tiny scale, materials can exhibit unusual physical and chemical properties, such as becoming stronger or better at conducting heat. These properties can make some materials more eco-friendly.
For example, using nano-clay in brick production can make bricks 4.8 times stronger than traditional options. Bricks could then become a more reliable construction material for larger projects, helping construction move away from materials with larger carbon footprints like steel and concrete.
Concrete with nanoparticle-based aggregates is more easily recyclable, helping reduce the industry’s reliance on virgin cement. Similarly, nanoparticles can make steel more corrosion-resistant, letting even recycled steel last longer and reducing the need for fresh metal.
Green Construction Starts With Materials Manufacturing
The construction industry has a long road ahead of it before it can call itself truly sustainable. Materials manufacturing will prove an essential part of that journey, as buildings’ embodied carbon must decline. If materials manufacturers embrace these sustainability initiatives, they can help the construction sector remediate some of its longest-standing problems.
These six solutions are not a definitive list, but are some of the most promising answers to material manufacturing’s sustainability challenges. As going green becomes increasingly important, materials manufacturers should consider these options and similar paths to reduce their products’ embodied carbon.
Comments (0)
This post does not have any comments. Be the first to leave a comment below.
Featured Product
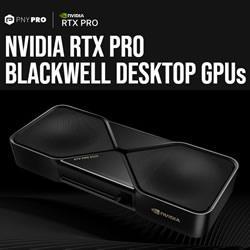