Tips to Help Manufacturers Address the 2021 Labor Shortage
As we begin to emerge from the COVID-19 pandemic, there is no doubt that many Americans have continued to encounter difficulties or delays when purchasing various items, whether it be household goods, appliances, automobiles, HVAC equipment or the numerous products that contain semiconductors. These unmet demands often lead to discussions regarding supply chain issues resulting from COVID-19. However, while the supply chain challenges are a piece of the story, it isn’t the whole story. In reality, manufacturers are also struggling to find and retain necessary skilled labor. Shortages in the skilled labor workforce are not solely driven by the pandemic, although despite the higher unemployment rates, there are many jobs that still need to be filled.
The U.S. has been seeing declines in skilled labor during the past few years as experienced and knowledgeable employees continue to retire while fewer are choosing employment in factories or skilled trades as such jobs are perceived as less desirable, less stable and offer lower wages.
For many industries, including manufacturing, the pandemic shined a bright light on industry challenges, forcing companies to react quickly and pivot to new solutions. It also has provided an opportunity to revisit processes and whether there are more efficient, less costly ways to operate. While the skilled labor shortage isn’t new, it has been correlated with the pandemic and the ongoing challenges with finding qualified talent to return to pre-pandemic levels.
From technology usage and hiring processes, manufacturers can assess various areas within their businesses operations, as well as the industry, to help respond to the current labor shortage obstacles.
Keep Up to Date with Federal Regulations
In June 2021, the Senate passed the United States Innovation and Competition Act (USICA) which is aimed toward investing in the next generation of American jobs and leadership in manufacturing and technology. Amongst the numerous provisions, USICA contains several higher-education provisions to facilitate research and development in key technology-focused areas including robotics, artificial intelligence, and advanced energy sources. These provisions incentivize higher education institutions to do more on those fronts through scholarships offered for postdoctoral programs, graduate fellowships, undergraduate courses, internship programs and more, with an emphasis on rewarding underrepresented populations in STEM.
Additionally, USICA allows Pell Grants to be used for short-term training and vocational programs that last only eight weeks, a change for the current 15-week requirement. As Pell Grants are funds offered to lower-income students to help pay for tuition and do not need to be repaid like student loans do, this amendment could boost enrollment in short-term training and vocational programs as students would now be able to utilize Pell Grants to pay for these programs.
While USICA may provide the foundation and funding to propel the United States forward in the area of manufacturing, the bill still needs to pass through the House of Representatives and will likely take time to see real impacts. With this in mind, it may be necessary for manufacturers to consider other ways to combat potential contributors to the current skilled labor shortage.
Introduce Technology
As mentioned, one key contributor of the labor shortage is the retirement of tenured employees, presenting a significant gap in experience and knowledge. There is a risk that such knowledge is lost unless steps are taken to ensure it can be transferred to other existing or new employees. Turnover in resources always comes with a cost; however, not retaining the knowledge of those individuals that depart is even more costly. It may be the right time to invest in technology to capture that institutional knowledge through systemized processes and workflows which can also provide a means to analyze data, identify inefficiencies and streamline production processes, recognize profitable and non-profitable production runs and increase monitoring efforts and data transparency.
Evaluate Training
Manufacturers should also consider whether their onboarding and ongoing training programs are adequate or require improvement in content, frequency, or delivery. Training programs can be significantly improved when supplemented with the enhanced systems, processes and workflows discussed above.
To ensure employees are fully engaged, they need to feel prepared and be provided the knowledge to succeed at their role. Additionally, existing employees need to have the opportunity to continually upskill and participate in training that enables growth and advancement. Manufacturers may want to consider offering or increasing apprenticeship programs to provide a paid position for on-the-job learning and to demonstrate the career path and growth opportunities available to individuals as an alternative path to earning a four-year degree.
Diversify the Workforce
Like many industries, diversity in the workforce is another aspect that manufacturer should explore. The skilled workforce has historically been dominated by white males, which may suggest that there is an information gap about the careers that exist in manufacturing or that there are diverse groups of potential candidates that aren’t being considered.
Expanding the pipeline and attracting talent may require a proactive and concerted effort and could involve additional efforts like launching recruitment campaigns at high schools, implementing flexible schedules to promote work/life balance, establishing diversity, equity and inclusion metrics upon which management would be measured, and rebranding the industry and opportunities as interesting, stable and a well-paying career.
The Future of the Workforce
Neglecting the workforce shortage issue could have real growth implications in both the manufacturing industry and the overall economy. To help respond to the labor shortage challenges, manufacturers should analyze various areas within their business to understand where they could improve in processes, hiring and retention. Furthermore, a federal commitment may also be necessary in order to rebound American jobs and investments in research and development, technology and manufacturing initiatives, protect U.S. manufacturing jobs and entice citizens to choose a career in manufacturing or other trades, obtain the skills to enter the workforce and earn a higher paying wage to support their family.
Comments (0)
This post does not have any comments. Be the first to leave a comment below.
Featured Product
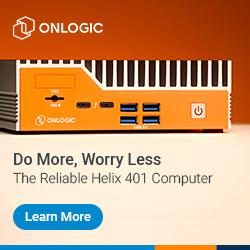