Forward, Toward a New Normal - A transitional playbook for resuming manufacturing operations in the [hopefully soon to be post] Covid-19 Era
As companies and their workforces emerge from their forced coronavirus hiatus, a clear picture of a “new normal” for the manufacturing business and its employees remains elusive, with only hazy possibilities and vague pathways forward.
What is clear, however, is that for the foreseeable future, there will be new employee, operational, customer and supply chain norms — some temporary, others here for the long haul — that manufacturers must find ways to internalize if they are to rebound from the crisis and remain sustainably competitive. Strong Industry 4.0 practices and capabilities surely will make the process of assimilating these new norms smoother and more efficient — and put companies in good position to actually shape the new normal for themselves.
In the short term, though, the focus is on reckoning with the transitional realities that apply to workforces, factory assets, production workflows, customer interaction/experience and the supply chain. Here’s a look at some of the digital tools and approaches that can be particularly helpful to manufacturers in those areas.
Workforce & HR
Complying with back-to-work guidelines from OSHA and the Center for Disease Control and Prevention (CDC) is one of many employee-focused considerations for manufacturers as they resume operations. As capacity restarts gradually, monitoring worker’s health to avoid an outbreak, and reinforcing employees’ sense of safety, are top priorities. Companies need to define and enforce new health and safety protocols as they reopen, with the ability to conduct in-house health screenings, monitor compliance with social/physical distancing policies, and track employee interactions in the workplace. A company could use a digital symptom check system to ask employees specific health and contact questions, and complement that with onsite contact tracing to manage exposure and identify workspaces that need to be sanitized.
The coronavirus outbreak has underscored how critical an asset your workers are, as well as the importance of providing them new work support options and more effective communication. The move to remote work we’ve seen in recent months likely will lead to more flexible working arrangements going forward. Companies thus will need secure digital communication and collaboration tools to support a less centralized workforce.
The model for recruiting and hiring also figures to change, at least for now, so HR departments will need to be flexible — and digital — in how they find, evaluate and onboard talent.
Also on the HR front, it’s critical that manufacturers have the means to rapidly train employees on any new production workflows and processes they’re implementing as a result of the crisis.
Amid so much uncertainty and fluidity in the markets they serve, manufacturers must find ways to be more agile, with the ability to reconfigure processes, people and technology to create value. With end-to-end operational visibility, a manufacturer can connect workforce (re)deployment directly with its production priorities, for example, using financial modelling to determine those priorities, then identifying which workers are essential to meeting them.
Returning to work can be a stressful experience. With the tools to digitally monitor, analyze and manage employee experience, manufacturers can open and maintain a communication and feedback loop with employees to clearly understand their morale, concerns and logistical needs as they return to work or stay working remotely. These experience-management tools give company leadership valuable data-supported insight into their employees’ mindset, and into the adjustments needed to improve the employee experience.
Using experience-management software, a company can assess employees concerns and confidence levels, and use aggregate data to gauge sentiment and areas of concern across its workforce. This can help inform how companies shape their policies. It also can help companies measure the effectiveness of the policies they implement.
Manufacturing Operations
On the production side, manufacturers are adjusting workflows and processes around new Covid-19 realities such as physical distancing, reduced workforce and uncertain demand.
Relying more on automated manufacturing processes, especially repetitive tasks, along with automated decision-making on the factory floor, can help to minimize the impact of future disruptions.
This heightened level of automation depends on a manufacturer’s ability to gather and analyze data from the factory floor so they have a firm handle on the products being produced, the time required for machine change-overs, the availability of parts, the impact of reduced workforce on production lines and overall throughput, machine downtime and other key information. With connected smart manufacturing assets and predictive tools such as digital twin, manufacturers can reconfigure their factories to meet production priorities, and to improve resource productivity and efficiency. When factory assets can communicate with one another via a central digital platform, factories can easily adjust to the flexible manufacturing line setups that today’s uncertain business climate demands and will allow them to make more individualized products efficiently in the future.
Customer & Demand-Side
The demand part of the picture looks equally uncertain. What is certain is that the coronavirus crisis will fundamentally shift how people work and live.
Maintaining contact with customers and soliciting their input to better understand their expectations (via social media, email, text message, etc.) and intentions is vital for business continuity and recovery. Manufacturers that have the multichannel digital tools to connect directly with customers to gather data about their expectations and experience during the transition to a new normal, and tailor the customer experience accordingly, may well emerge from the crisis with stronger customer relationships. It is clear that manufacturers will need to accelerate the shift to e-commerce, digitizing the purchase experience and placing a greater emphasis on new business models.
During the transition, order backlog management and order prioritization will be critical, supported by the ability to assess customers’ lifetime value and other criteria.
Supply Chain & Logistics
The Covid-19 crisis has exposed vulnerabilities in even the strongest supply chains and most rigorously tested contingency plans. Rigid supply chains limited the ability of some manufacturers to switch suppliers in a pinch, and a general lack of visibility into supply chain risk made planning difficult. Companies need to start redesigning supply chains to optimize resilience and speed. So instead of thinking offshore vs. onshore, the starting point is building a supply network that creates the most value, perhaps with multi-shoring and an emphasis on geographic diversity and business networks versus single-sourcing.
Developing such a supply network requires a set of robust supply risk analysis and management tools, including the analytic and modeling capabilities to identify the most pressing supply chain vulnerabilities, such as a lack of alternative sources for a key material or component. A digital platform to which the entire supply network is connected, and across which data about inventory, delivery timelines, transportation logistics, etc., flows seamlessly in real time, can provide members of the network with the visibility they need to make sound strategic decisions in collaboration with their partners. Here’s where financial scenario planning capabilities also prove valuable, enabling companies to model various scenarios to make well-informed decisions while identifying and prioritizing risk and exposure.
As important as a connected, collaborative supply network and Industry 4.0 tools can be in a crisis like the one we’re experiencing today, they will be essential to competing in the manufacturing business, whenever it finds its new normal.
Gustavo Milan is an Industrial Manufacturing Industry Advisor at SAP, where he’s part of the Global Industrial Manufacturing Industry team focusing on delivering value to customers and building customer experience strategies.
Comments (0)
This post does not have any comments. Be the first to leave a comment below.
Featured Product
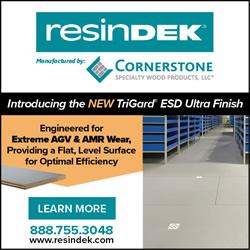