The Big Challenges of 3D Printing
3D printing, also known as additive manufacturing, is al alternative production technology which allows for a layer-by-layer creation of more durable, stronger and lighter objects.
“You may have heard about the benefits of 3D printing – the freedom of designs, the lack of tools required, the just-in-time inventory, and so on. To the engineers of today, the list of advantages are endless – it’s a revolution for companies, across all industries,” explains Joe Hughes, tech expert at Writinity and Last Minute Writing.
With all of the benefits of 3D printing, you’d think it would be as commonplace as Wi-Fi in today’s world – but that’s actually not the case. Many companies are struggling to find ways to incorporate 3D technology printing into their product development and manufacturing operations – a bare 2% of the manufacturing market is made up of 3D printing, according to a 2014 report.
However, this is all set to change. The global 3D printing market is set to reach $21 billion by 2020, quadrupling in size. It’s useful then, to understand that despite the challenges faced by businesses wanting to use 3D printing, there are many benefits to 3D printing – the freedom to design what they want, easy prototyping, customisation and streamlined logistics. The challenges presented by 3D printing should be understood by manufacturing leaders, in order to overcome them.
- Lack of Standardization
One of the main problems of 3D printing is the lack of standardization of machines, and the potential for low-quality products. Sometimes, the inexpensive nature of 3D printing costs quality; there are high-end machines that cost millions of dollars to purchase, but others product goods that are inferior to those made by traditional manufacturing.
There is a lack of universal standards in the printing technologies – many manufacturers worry about their products or parts of products produced via 3D printing will be on a par with other manufacturing methods in terms of quality, strength and reliability. So, they remain wary of 3D printing technology, judging the risks involved too great to meet with the benefits.
Lately, there are pushes to end this uncertainty with industry wide standardization of Additive Manufacturing.
- Expenses
Traditional manufacturing has become a refined and incredibly efficient process over the years. Think about plastic bottles – we’re simply too good at making them, so much so that they are a huge issue for the environment. 3D printing may simply be too expensive for a few more years to come, as processes are not refined and streamlined enough.
For example, metal printers required by big companies can easily cost tens of thousands of dollars – the process is slow, and costly. The time taken to 3D print depends on the number of layers that need to be printed, and the speed of the printer itself. Even the best 3D printers can only build between 5 and 40 cm per hour.
- Product Lifespan Problems
The possibility to print a lot of spare parts on demand can extend product guarantees and is actually much more environmentally friendly. Unfortunately, many companies rely on a business model based on low quality products and product rotation. By reducing product obsolescence, 3D printing is a problem – companies will have to work on new business models that guarantee quality and product lifespans, and don’t rely on manufacturing new products constantly. Moreover, 3D printing allows customers to print their own spare parts – not a good thing for companies!
- Copy-Cats
As noted above, consumers could begin printing their own product parts. This is made even more problematic when we see that smaller businesses could begin printing product parts and whole products, copying the intellectual property of bigger businesses.
“Cheap knock-offs from abroad have already seen companies face big hits, and if consumers and small businesses can now product home-made copies, distribute designs and copy products, manufacturers could see their sales hit hard. The manufacturing industry will need to adapt – and that could mean selling dematerialised files with a license online,” notes Sophia Austin, a business journalist at Draftbeyond and Researchpapersuk.
Ashley Halsey is a professional writer at LuckyAssignments and Gumessays.com who has been involved in many projects throughout the country, including many studies of automation and additive manufacturing. Mother of two children, she enjoys traveling, reading and attending business training courses."
Comments (0)
This post does not have any comments. Be the first to leave a comment below.
Featured Product
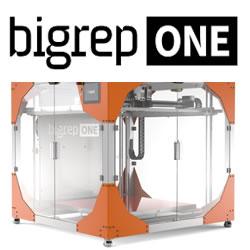