Nanotechnology and the future of manufacturing
Nanotechnology involves the manipulation of matter on the atomic and molecular scale — structures between one and 100 nanometres in size. To put that into perspective, comparing a nanometre to a metre is like comparing the size of a marble to the size of the earth. Here Mark Howard, US country manager at automation parts supplier, EU Automation discusses three exciting applications of nanotechnology in manufacturing.
Nanomanufacturing focusses on the development of scalable, high yield processes for the commercial production of materials, structures, devices and systems at the nanoscale. Recently, it has been a growing area of research and development (R&D) for manufacturing applications.
Engineers can synthesise nanomaterial in two ways, the first is by using the top down method, the process of carving nanomaterial out of something bigger. This is the most common method, often used to make computer chips and other everyday items. The alternative is the bottom up method, the process of assembling a structure at the molecular level, one atom at a time. This method is still in the experimental stage of development and is time consuming and complex.
Extensive R&D has led to significant advances in nanotechnology, some which could revolutionise manufacturing processes. Exploration into what can be achieved using the bottom down method has encouraged research into creating molecular components that can self-assemble into a specific structure without the need for external interaction. Three applications in particular reveal tangible evidence of what the future of manufacturing will look like.
Improving safety
The integration of nanomaterial into coatings has led to a great progression in safety wear and has become increasingly popular for biotextiles. When nanosized carbon particles are dispersed within the original fibres of the garment, they create a covering of nanofibers. Using carbon nanofibers as a textile composite makes the garment liquid repellent, stain resistant and even antimicrobial. In manufacturing, this safety wear can be used to protect workers in hazardous areas.
Fuel efficiency
Polymer nanotechnology involves dispersing nanoparticles into an existing polymer’s matrix to develop adhesives, sealants, coatings, potting and encapsulation compounds. Incorporating nanoparticle fillers to these applications has the potential to develop characteristics of thermal stability, water and chemical resistance, higher tensile strength and even flame resistance.
Polymer nanocomposites have become an important addition to the automotive industry, for tyre manufacturing. The chemical and flame-resistant particles offer better performance at a lighter weight to traditional tyres, subsequently offering higher fuel efficiency.
Reducing friction
Introducing nanotechnology to the production of lubricants has unlocked the possibilities for more diverse solutions in manufacturing. In instances where oils are typically used to reduce the friction between two objects, nanoparticles can be used instead. These nanoparticles act like tiny ball bearings, rolling between the two surfaces and reducing the opportunity for heat, wear and oil failure. A diminishing supply of fossil fuels means this development could be revolutionary not just for the future of manufacturing, but for the environment too.
Nanometres may be the size of a marble when compared with the earth, but that doesn’t diminish the significance of nanotechnology. With further research dedicated to the progression of nanomaterials, momentum is building for more industries to incorporate nanotechnology into their day-to-day procedures.
For more information, visit www.euautomation.com.
Comments (0)
This post does not have any comments. Be the first to leave a comment below.
Featured Product
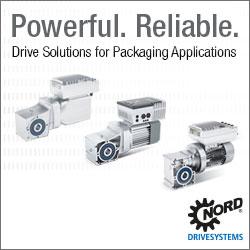