Maximize Efficiency: Seamless Integration with NORD's Intelligent Drive Technology
NORD’s innovative drive systems paired with their basic-to-advanced electronic control technology match a wide range of applications thanks to scalable functionality, high precision regulation, and ease of installation.
Electronic control products from NORD DRIVESYSTEMS are designed for high performance versatility to efficiently manage a wide range of applications requiring high functioning motor controls. As knowledgeable experts in drive technology, NORD effectively partners with customers all over the world to provide solutions that are perfectly matched to their requirements. They offer AC vector drives designed for operation with asynchronous and synchronous motors as control cabinet solutions as well as decentralized solutions. Both are characterized by their scalable functionality, ease of installation, and high precision regulation.
Thanks to their scalable functions, NORD electronic control products are compatible with their full product portfolio of high efficiency gear motors for a complete drive solution adaptable to various industries. The high dynamics, speed control, and precise positioning of the variable frequency drives is ideal for baggage handling systems in airports, bottling systems in the beverage industry, packaging machinery, labeling systems, swivel cranes, and more. Variable frequency drives also enable synchronization of multiple drives such as those in metal processing lines, intralogistics conveyor systems, stage theater technology, and travel drives. Each product family offers basic and advanced versions available with extensive module options for added performance. The NORDAC PRO SK 500P variable frequency drives for example, have five different frame sizes to choose from with each size extending the power range and functionality scope.
In addition to their versatility across a wide range of applications, NORD variable frequency drives are also compatible with a wide variety of Fieldbus implementations including EthernetIP, PROFINET, EtherCAT, and others. NORD application support offers helpful documents and instruction sets to help integrators and design engineers integrate NORD VFDs into common control systems.
All NORDAC variable frequency drives have built-in Programmable Logic Controllers (PLCs) capable of executing various standalone applications. Many of the models including the NORDAC PRO, NORDAC LINK, NORDAC ON, and NORDAC FLEX have encoder interfaces that enable servo-like positioning capabilities with high-precision speed regulation. NORDAC VFDs operating in closed loop mode can manage systems more efficiently, replacing the need for costly, complex servo components.
NORD is an industry leader when it comes to quality and lead time performance. All NORDAC components are manufactured at an in-house facility in Germany with final assembly of models completed at the North American headquarters in Waunakee, WI. Current lead times on NORDAC electronic controls are only 4-6 weeks.
From application development to commissioning and field service, NORD has the resources to support customers' goals. Their inhouse Inverter Lab can model applications for quick resolution of implementation challenges, saving time and money. NORDAC VFDs have multiple commissioning methods for field programmability and can even be programmed during the final assembly process at NORD for ease of start up in the field. Frequently asked questions are listed online for quick, easy reference and for further support, a digital self-services portal is available to submit service requests, find specific unit documentation, and contact the Sales Team or Service department.
Featured Product
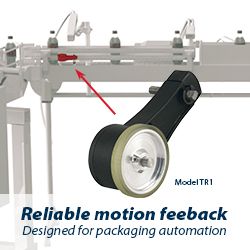