Thinaer Tracks the Untrackable with New IIoT Solution
Thinaer's platform fills digital blind spots, enabling commercial and classified area manufacturers with continuous and contextualized visibility of their operations
Thinaer, a manufacturing digital transformation pioneer, today announced its IIoT asset tracking and digital twin SaaS solution, which is uniquely designed to fill manufacturing data blind spots and deliver IIoT-centric digital transformation for both commercial and classified areas.
Through a strategically designed sensor, infrastructure and cloud agnostic platform, Thinaer tracks the previously untrackable. By filling digital blind spots, Thinaer enables commercial and classified area manufacturers with continuous and contextualized visibility of their operations, providing a complete data picture to drive strategic decisions and build next-generation AI datasets.
"Most commercial and almost all classified area manufacturing processes are not connected or connect-able resulting in upwards of 75% of digital blind spots, leaving manufacturers without a complete data picture to make strategic decisions" said Bryan Merckling, CEO at Thinaer. "Thinaer can holistically connect operations, build the most complete dataset for nextgen AI initiatives and fill blind spots using the latest sensors and infrastructure needed to accomplish any use case."
A complete data picture ensures digital transformation and AI initiative success with improved and more profitable production decisions. Thinaer's unique approach makes it easy for organizations to start their digital transformation and future-proof their investment. Utilizing Thinaer's IIoT infrastructure, different functional groups can layer in additional use cases by deploying more sensors while using the same infrastructure to rapidly scale and fast track ROI , all while accommodating the requirements for both commercial and classified area processes.
Thinaer uses IIoT asset tracking and digital twin to address a major pain point in manufacturing by providing solutions for real-time asset location tracking, environmental condition monitoring, and machine usage and utilization. The platform integrates with nearly any off-the-shelf sensor, can leverage network access points as infrastructure, and hosts multiple cloud options, providing organizations with the flexibility needed to deploy solutions that fit their specific needs.
"One of our customers achieved a 30 million dollar ROI in their first use case and as a company, we are in a constant state of evolution, consistently refining our products to lead the way in embracing the latest trends," said Bryce Merckling, VP of Product at Thinaer. "Our commitment is unwavering, ensuring that we not only keep pace but stay ahead of the curve in adopting new technologies entering the market."
Featured Product
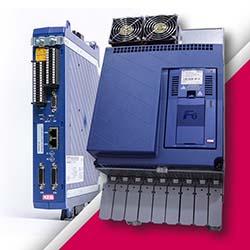
KEB VFDs for High Speed Motor Control
KEB's VFDs are the key to unlocking peak performance in your high-speed machinery. Engineered for precision control, even without feedback sensors, our F6 and S6 drives utilize advanced software and high-frequency output. This ensures smooth operation, reduced vibration, and optimal efficiency. Whether you're building turbo blowers, power generation systems, or other high-speed applications, KEB VFDs deliver the reliability and performance you need.