Stratasys Expands Market Opportunities for Medical Device Manufacturers to Leverage 3D Printing to Enhance Innovation and Improve Patient Outcomes
Stratasys Direct’s New ISO 13485 Certification Meets Stringent Regulatory Requirements Essential for Medical Device Manufacturers
Stratasys Ltd. (NASDAQ: SSYS) today announced that its Stratasys Direct manufacturing facility in Tuscon, Arizona has achieved ISO 13485 certification, a globally recognized standard for quality management systems in medical device manufacturing. Stratasys plans to extend this certification to its other Stratasys Direct manufacturing facilities in Texas and Minnesota.
By achieving ISO 13485 certification, Stratasys Direct is formally recognized for its safety, precision, and reliability of its 3D-printed components. This certification addresses critical regulatory requirements, removing barriers to adoption and enabling medical device manufacturers to scale production reliably while accelerating innovation, reducing costs, and improving patient outcomes.
Stratasys Direct 3D prints multiple components for the medical industry making complex geometries and patient-specific components that traditional methods cannot achieve.
"ISO 13485 certification is a game-changer for medical manufacturing," said Gurvinder Kahlon, General Manager and Vice President, Stratasys Direct. "This achievement reflects our commitment to delivering solutions that not only meet rigorous regulatory standards but also empower the medical industry to innovate faster and deliver better patient care."
Stratasys Direct has been a trusted partner to the medical field for years, delivering custom 3D-printed models and components. The ISO 13485 certification builds on that legacy, positioning 3D printing as an essential tool for the medical device industry. By adopting 3D printing, medical manufacturers can reduce development times, create highly customized components, and innovate faster than with traditional manufacturing methods. Stratasys Direct's ISO 13485 certification provides a clear pathway to regulatory compliance, ensuring consistent quality and expanding market access for these advanced manufacturing solutions.
Stratasys Direct will showcase its capabilities and commitment to the medical industry at MD&M West, taking place February 4-6, 2025, in Anaheim, California.
About Stratasys
Stratasys is leading the global shift to additive manufacturing with innovative 3D printing solutions for industries such as aerospace, automotive, consumer products, and healthcare. Through smart and connected 3D printers, polymer materials, a software ecosystem, and parts on demand, Stratasys solutions deliver competitive advantages at every stage in the product value chain. The world's leading organizations turn to Stratasys to transform product design, bring agility to manufacturing and supply chains, and improve patient care.
To learn more about Stratasys, visit www.stratasys.com, the Stratasys blog, X/Twitter, LinkedIn, or Facebook. To learn more about Stratasys Direct's 3D printing services, visit https://www.stratasys.com/en/stratasysdirect/. Stratasys reserves the right to utilize any of the foregoing social media platforms, including Stratasys' websites, to share material, non-public information pursuant to the SEC's Regulation FD. To the extent necessary and mandated by applicable law, Stratasys will also include such information in its public disclosure filings.
Featured Product
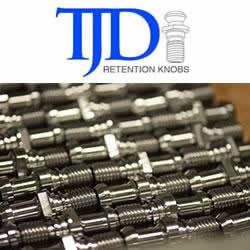
T.J. Davies' Retention Knobs
Our retention knobs are manufactured above international standards or to machine builder specifications. Retention knobs are manufactured utilizing AMS-6274/AISI-8620 alloy steel drawn in the United States. Threads are single-pointed on our lathes while manufacturing all other retention knob features to ensure high concentricity. Our process ensures that our threads are balanced (lead in/lead out at 180 degrees.) Each retention knob is carburized (hardened) to 58-62HRC, and case depth is .020-.030. Core hardness 40HRC. Each retention knob is coated utilizing a hot black oxide coating to military specifications. Our retention knobs are 100% covered in black oxide to prevent rust. All retention knob surfaces (not just mating surfaces) have a precision finish of 32 RMA micro or better: ISO grade 6N. Each retention knob is magnetic particle tested and tested at 2.5 times the pulling force of the drawbar. Certifications are maintained for each step in the manufacturing process for traceability.