Electropolishing VS Mechanical Polishing
Polishing refers to the use of mechanical, chemical or electropolishing action to reduce the surface roughness of the workpiece to obtain a bright and smooth surface. It is the modification of the surface of the workpiece by using polishing tools and abrasive particles or other polishing media.
Polishing cannot improve the dimensional accuracy or geometric accuracy of the workpiece, but is aimed at obtaining a smooth surface or specular gloss, and sometimes it is also used to eliminate gloss (matting).
Mechanical polishing is a manual process performed on a single part, whereas electropolishing can be performed on multiple parts at once. Here we introduce the definition and difference between mechanical polishing and electropolishing, hoping to help you make a suitable choice for you.
What Is Electropolishing?
Electropolishing is also called electrolytic polishing. This is a polishing process. Electropolishing electrochemically polishes metal parts. Electropolishing is a metal finishing process that can be performed on a variety of special and common alloys such as copper, aluminum, stainless steel, carbon steel, nitinol, titanium, and more. This "reverse plating" process relies on rectified current and a phosphoric acid-based electrolyte to remove a layer of surface material from metal parts.
A current converted from alternating current to direct current at low voltage is applied to the part to remove the outer skin of the material. To complete the procedure and remove any remaining electrolyte, electropolishing specialists rinse and then dry the part.
After electropolishing a steel part, uneven "bumps" and "burrs" on the metal surface are leveled or removed. Electropolishing is also used to passivate and remove metal parts.
Electropolished parts have clean surfaces and are suitable for a variety of industrial applications including medical, food service, pharmaceutical, automotive and aerospace.
What Is Mechanical Polishing?
Mechanical polishing is the process of making the surface of a part smooth and shiny mechanically rather than chemically. When examining an unpolished part under a microscope, you can see visible "bumps" on the surface. After the part is polished, these "bumps" get smaller. Mechanical polishing is also the process of polishing with abrasives such as sandpaper. The process varies based on original part condition and finish requirements. This is a labor-intensive metal finishing process that is operator controlled and difficult to maintain consistently.
Advantages Of Electropolishing
After examining the differences between mechanical polishing and electropolishing, many companies have decided that there are many benefits to using electropolishing, including:
Enhanced Corrosion Resistance
Untreated metal parts can rust or corrode over time. Electrolytic polishing is 30 times more effective than chemical passivation.
Deburring Edges
Untreated metal parts may have jagged edges, which may be unsafe for some applications, including those in the medical industry. To ensure parts have a smooth surface, they should undergo metal finishing, such as electropolishing.
Ultra Clean Finish
Electropolished metal parts have ultra-clean surfaces that mechanical polishing treatments cannot consistently achieve. Unlike mechanical polishing, electropolishing removes a uniform layer of surface material to create a smooth surface free of debris or other contaminants.
Removed Heat Tint And Oxide Scale
Because electropolishing removes the outer layers of the material, it eliminates scale and hot color that can occur during welding and heat treatment of parts. Electropolishing also reduces the onset of corrosion.
Higher Shimmer Finish Values
Mechanically polished parts with improved micro-finish values cannot reach small features of complex parts. However, electropolishing uses concentrations that reduce microscopic peaks in inaccessible areas.
Enhanced Appearance
Electropolished parts have a bright, shiny appearance that is uniform and lasts indefinitely.
Important Notes About Mechanical Polishing
Mechanical polishing provides a good surface profile for both low and high purity applications. But mechanical polishing not only fails to remove inclusions, but tends to push them into deeper surfaces and even exacerbate them by trying to pick up additional abrasive material, potentially leading to further areas of corrosion.
In addition, the mechanical finishing process eliminates contamination present on the part and provides a bright finish. On the other hand, the electropolishing process produces a completely featureless surface. It shows the true crystal structure of the metal without the distortion caused by the cold working process, which is always evident when using mechanical finishing methods.
How To Choose Between Electropolishing And Mechanical Polishing
Mechanical polishing improves metal surfaces or metal parts by reducing surface roughness, it will give you a smooth surface. In addition, almost all types of materials, including stainless steel alloys, aluminum, metal finishes, and even mirror finishes are improved by mechanical polishing.
However, if you want to remove burrs, clean the scratches with polishing, then electropolishing will serve you well. Electropolishing will help improve the production process if a better surface finish is required for a large number of metal parts.
In addition, if the number of prototypes is small, it is better to choose manual polishing or mechanical polishing, because the cost of electropolishing a prototype is high, and the suppliers who provide this service often have a minimum order quantity.
Conclusion
Both electropolishing and mechanical polishing play an important role in adding the finishing touch to each form of metal. Both techniques also help hide scratches. Compared to passivation, electropolishing equipment helps improve the corrosion resistance of stainless steel by increasing the chromium-to-iron ratio by 4%, resulting in a 30-fold increase in electrical resistance.
In conclusion, mechanical polishing does not produce dangerous chemical reactions and is effective on both metals and plastics. Electrolytic polishing can improve corrosion resistance and facilitate the polishing of a large number of metal parts.
So, depending on your needs and budget, learn the difference between electropolishing and mechanical polishing, then choose the most suitable finishing service for your project.
Featured Product
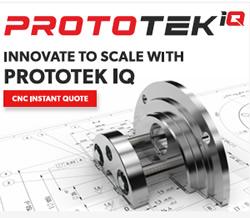
Prototek IQ - Digital Manufacturing Services
Prototek IQ is our new instant quoting platform that simplifies your manufacturing process. With just a few clicks, you can get accurate quotes for 3D printing and CNC machining, which are currently two different platforms. Our easy-to-use interface helps you make smart choices. Use Prototek IQ to improve efficiency and streamline speed to market. We invite customers with experience in large projects, 3D printing, and CNC machining, as well as those with repeat orders, to try our instant quoting platform. You can choose our engineer-assisted quote option if you have unique needs, such as high quantities, specific quality standards, fast delivery, or special finishes.