Trelleborg Supplies Boeing with Component for 3D-Printed Face Shields
Trelleborg Sealing Solutions, an established provider of solutions to Boeing’s aircraft, is supplying a face shield component to the aerospace manufacturer as it joins the urgent effort to assist medical workers on the front lines of the COVID-19 coronavirus pandemic.
Trelleborg Sealing Solutions, an established provider of solutions to Boeing's aircraft, is supplying a face shield component to the aerospace manufacturer as it joins the urgent effort to assist medical workers on the front lines of the COVID-19 coronavirus pandemic.
Boeing approached Trelleborg at the end of March 2020, to manufacture and supply an elastomer strap needed for the adjustable headband of 3D printed face shields. The Trelleborg Sealing Solutions dedicated aerospace facility in Northborough, Massachusetts, supported a 48-hour turnaround of prototypes using methodologies including 3D printing. The following week, the site was able to ramp up production to 5000 straps per week.
Quinn Collett, Air Frame Manager, Trelleborg Sealing Solutions Aerospace, says: "In these unprecedented times, it's imperative everyone plays a role that might not be in line with the one they are used to. We were fortunate to receive the call from Boeing to support this effort and leverage Trelleborg's expertise to quickly address the need."
Boeing plans to produce face shields using its additive manufacturing machines at various sites across the US. Boeing is working with the Federal Emergency Management Agency (FEMA) on this effort. FEMA will determine where the face shields are most needed.
The elastomer straps provided are manufactured from aerospace grade silicone. After a few fit trials, Boeing and Trelleborg were able to lock in the final released design.
About Trelleborg Sealing Solutions and Trelleborg Group
Trelleborg Sealing Solutions is one of the world's leading developers, manufacturers and suppliers of precision seals, bearings and custom-molded polymer components. It focuses on meeting the most demanding needs of aerospace, automotive and general industrial customers, including those from the pharmaceutical industry, with innovative solutions. Its network extends to over 25 production facilities and more than 50 marketing companies globally. The business area accelerates the progress of its customers through outstanding local support, an unrivalled product range including patented products and proprietary materials, a portfolio of established brands, unique process offerings, its ServicePLUS value chain solution and ‘Ease of Doing Business' philosophy.www.tss.trelleborg.com
Trelleborg is a world leader in engineered polymer solutions that seal, damp and protect critical applications in demanding environments. Its innovative solutions accelerate performance for customers in a sustainable way. The Trelleborg Group has annual sales of about SEK 37 billion (EUR 3.46 billion, USD 3.87 billion) and operations in about 50 countries. The Group comprises three business areas: Trelleborg Industrial Solutions, Trelleborg Sealing Solutions and Trelleborg Wheel Systems, and a reporting segment, Businesses Under Development. The Trelleborg share has been listed on the Stock Exchange since 1964 and is listed on Nasdaq Stockholm, Large Cap.www.trelleborg.com
Featured Product
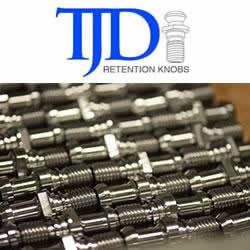
T.J. Davies' Retention Knobs
Our retention knobs are manufactured above international standards or to machine builder specifications. Retention knobs are manufactured utilizing AMS-6274/AISI-8620 alloy steel drawn in the United States. Threads are single-pointed on our lathes while manufacturing all other retention knob features to ensure high concentricity. Our process ensures that our threads are balanced (lead in/lead out at 180 degrees.) Each retention knob is carburized (hardened) to 58-62HRC, and case depth is .020-.030. Core hardness 40HRC. Each retention knob is coated utilizing a hot black oxide coating to military specifications. Our retention knobs are 100% covered in black oxide to prevent rust. All retention knob surfaces (not just mating surfaces) have a precision finish of 32 RMA micro or better: ISO grade 6N. Each retention knob is magnetic particle tested and tested at 2.5 times the pulling force of the drawbar. Certifications are maintained for each step in the manufacturing process for traceability.