Dissatisfied Workers Cost Frontline Businesses approx. $USD 196 Billion* a year in Lost Productivity
Global report reveals critical gaps in frontline workforce management
SYDNEY - November 22, 2024: Global technology company, SafetyCulture, has released its fourth annual Feedback from the Field report that highlights a challenging period of change for frontline industries, with a stretched workforce battling fractured workplace relationships, inefficient tools, and a shrinking skills pipeline.
Workers are feeling overworked and frustrated with inaction on issues
The majority (78%) of workers are dissatisfied with some aspect of their job. Among these, the primary reasons are slow responses to resolving issues or risks (40%), unreasonable expectations leading to burnout (35%), and pressure to cut corners to save time or money (32%).
When workers are unhappy, performance takes a hit. Of workers who admit to dissatisfaction impacting their performance, 44% feel less motivated, 34% report reduced productivity and 31% say they're more likely to quit and find another job - this rises to 35% among these Gen Z workers.
On average, workers lose about 7 hours a month due to dissatisfaction, which may show up as unproductive downtime, errors, or absenteeism. The collective impact of this discontent is costing frontline businesses an estimated $USD 196 billion1 annually - dubbed the "Dissatisfaction Dollar."
"Them vs. us" - a divide between management and the frontline
Focusing on the construction, retail, manufacturing, mining and energy, logistics, and hospitality sectors, the study reveals a concerning disconnect between management and frontline employees. About half of both groups (50% of employees and 55% of managers) agree there is a "them versus us" mentality between those on the tools and those off them. When asked about various aspects of work, communication from management (38%) and overall management performance (34%) are among factors that frontline employees express most dissatisfaction with.
Sam Byrnes, Chief Product Officer at SafetyCulture, says, "Frontline workers are telling us they feel unheard, overstretched, and compromised. On top of this, there is a strained relationship between employees and management that isn't conducive to a healthy workplace culture or optimal outputs.
"There will always be room for improvement within organizations, but leaders are doing themselves, and their people, a huge disservice by failing to understand frontline challenges, acknowledging and addressing issues, and communicating adequately.
"It's time businesses woke up to the fact that listening to people on the frontline is one of the fastest ways to improve the bottom line."
While the relationship between frontline employees and management shows some cracks, the research explores ways to help repair them - and it's apparent that money talks. Of workers who believe the relationship between the frontline and management could be improved, over half (55%) say better pay and benefits would help. This rises to 61% among frontline employees, compared with 46% in management roles.
The current socio-economic environment could be contributing to the importance placed on better pay and benefits. Three-quarters (76%) of workers with concerns about the future cite the rising cost of living as a worry - the most common concern across all regions surveyed. Looking beyond remuneration, workers who believe the relationship between the frontline and management could be improved say that recognition for strong performance (47%), more regular communication (46%), and, once again, acknowledging and actioning feedback (40%) would help improve the relationship.
Outdated and unfit tools & IT systems are causing a productivity roadblock
Despite hype - and fear-mongering - around new technologies, most workers appear unfazed by their potential impact. Only 34% of those with concerns about the future cite emerging technologies, such as AI, as one of them. In last year's Feedback from the Field report, 40% of respondents ranked AI among their top three concerns, potentially suggesting growing familiarity or comfort with the technology over the past year.
While workers aren't expressing much concern about new technologies, they are frustrated by outdated tools that hinder their efficiency. Nearly two-thirds (63%) of workers are not fully satisfied with their current tools and IT systems. Of these, more than one-third (36%) are dissatisfied with outdated tools and systems, 31% with tools that are unfit for purpose, and 29% with insufficient training on how to use them.
Ineffective tools and IT systems not only frustrate workers but also reduce productivity by slowing processes and causing unnecessary downtime. On average, workers lose almost 6 hours a month due to the impacts of ineffective tools and IT systems. This inefficiency costs frontline businesses worldwide a staggering estimated $USD 162 billion3 annually.
"Workers are only as effective as their tools. That's why we've gathered insights from the frontline at every step of developing the SafetyCulture platform, helping us build an accessible, mobile-first platform that, above all else, meets worker's true needs.
"These tools give onsite teams the knowledge, tools, and confidence to work safely, meet higher standards, and improve every day. It's the power of improvement in their hands."
A brain drain looms due to skills shortages
Outside of the workplace, macro conditions are also weighing on workers' minds. Nearly three in five (57%) workers believe their industry will suffer a brain drain in the future, and 71% of workers believe that skills and labor shortages will present critical issues in their industry. Nearly one-third (31%) of these workers say these shortages are already presenting critical issues, and an additional 39% believe these problems will occur within just three years.
"Workers across the globe are experiencing a huge amount of change. Rising living costs, shrinking skills pipelines and new technologies like AI, just to name a few, are demanding transformation. Even though this time is filled with uncertainty, it's ripe with opportunity to build organizations that don't just survive, but thrive in the future," Byrnes concludes.
For more information and to download the full report, visit https://safetyculture.com/feedback-from-the-field-time-for-change/
Featured Product
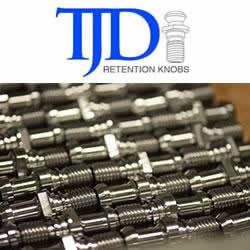
T.J. Davies' Retention Knobs
Our retention knobs are manufactured above international standards or to machine builder specifications. Retention knobs are manufactured utilizing AMS-6274/AISI-8620 alloy steel drawn in the United States. Threads are single-pointed on our lathes while manufacturing all other retention knob features to ensure high concentricity. Our process ensures that our threads are balanced (lead in/lead out at 180 degrees.) Each retention knob is carburized (hardened) to 58-62HRC, and case depth is .020-.030. Core hardness 40HRC. Each retention knob is coated utilizing a hot black oxide coating to military specifications. Our retention knobs are 100% covered in black oxide to prevent rust. All retention knob surfaces (not just mating surfaces) have a precision finish of 32 RMA micro or better: ISO grade 6N. Each retention knob is magnetic particle tested and tested at 2.5 times the pulling force of the drawbar. Certifications are maintained for each step in the manufacturing process for traceability.