Manufacturing’s Finest Hour
THE WOODLANDS, TX, APRIL 9, 2020 - America and its allies won World War II in large part because of our country's massive manufacturing effort. The number of tanks, planes, trucks, ammunition and other essential war materials produced within a few years was unprecedented. These gave us an unbeatable advantage over our enemies on the land, in the sea and in the air.
Currently, we're in a different kind of war against the COVID-19 virus. And much like World War II, we entered this war woefully undersupplied, lacking the tools required to diagnose and treat it, while protecting those on the front lines. As someone who has spent my entire adult life in the manufacturing industry, it comes as no surprise that American manufacturers are once again stepping up to the plate. I couldn't be prouder of the way many are responding to the urgent need to produce the tools and equipment needed to win this war.
There's a scene in the movie "Apollo 13" in which NASA officials are discussing the odds of getting the crippled space craft back home. The head of NASA comments that it could be the worst disaster in the history of the agency. Gene Krantz, NASA's Chief Flight Director, responds by saying, "With all due respect sir, I believe this is going to be our finest hour."
I believe this is the finest hour for the manufacturers who have accepted the challenge of getting the needed supplies and equipment to the brave Americans on the front lines of the war on COVID-19. Here are a few of our customers stories.
Helping COVID Victims Breathe
Based in Addison, Illinois, Pioneer Service makes a wide variety of custom components, many of which go into oxygen equipment, ventilators, respirators and hospital beds. When COVID-19 began overwhelming hospitals and first responders, many of Pioneer's medical customers found themselves unable to meet the sudden upsurge in demand for these vital pieces of equipment. Fortunately, when the calls began coming in, Pioneer Service was well positioned to do their part.
"We had begun ramping up for strong growth before the onset of the pandemic," says Beth Swanson, Vice President of Marketing for Pioneer Service, "so we already had the people and equipment in place. The main issue was whether our suppliers could meet our need for raw materials. Most of them have come through, and we're now committing 70% of our facility to making the components our medical customers need."
In addition to ramping up production of their existing medical parts, Pioneer has begun making new components for respirators and ventilators. They're producing a new type of hospital bed system that makes it easier to move beds when transporting patients from one location to another. Meanwhile, another significant challenge has reared its head - keeping a full crew when many employees have young children at home or take care of their parents.
"COVID-19 has turned everyone's home life upside down, so we had to make some adjustments so employees can come to work every day," says Swanson. "We designated a person to shop and run errands for employees. We're bringing lunch in once a week. And we continue to look for other ways to reduce employees' stress so they can focus on their jobs."
As an ISO 9001 and AS9100 company, Pioneer Services makes a clean working environment a top priority. However, going after germs has taken their cleaning protocols to a new level.
"We require employees to wash their hands when they arrive and leave work," says Swanson. "We wipe down all machine surfaces between shifts, and we don't allow visitors in the building. The hardest part is staying six feet apart because of the collaborative nature of our work."
"Pioneer has a history of helping out in the local community, but we feel an extra level of commitment to the brave people all across the U.S. who are battling the virus. We need to stay well so we can help others recover."
If You Build It They Will Come
For the past 40 years, Lakeview Industries has been making custom foam, plastic and rubber parts for many industries. Their medical products range from die cut cushions and molded silicone bumpers to conductive gaskets that provide an electromagnetic interface (EMI) shield to protect sensitive electronic devices. Never did they expect to be making a product to help fight a raging viral pandemic.
As the COVID-19 virus began to spread throughout the U.S., news of the drastic shortages of personal protection equipment (PPE) disturbed company co-owner John Schwanke. In particular, he couldn't understand why protective face shields were so hard to come by. At the urging of his wife, Cathy, he researched the type of face masks being used and decided his company could make one.
Within days, Lakeview Industries had produced and donated 40,000 single-use face masks to the state of Minnesota. Shortly thereafter, Schwanke's phone began ringing off the hook with orders from law enforcement and trauma centers all over the U.S. Initially, it took about a week to produce 100,000 of the masks. Now that Lakeview Industries has the process down pat, the firm expects to ship more than 250,000 a day.
The single-use masks, which are assembled by hand, have a simple design that consists of a plastic sheet to protect the face and an elastic strap to hold it in place. The elastic allows for a "one size fits all" mask that is easy to put on and wear. Most important, the masks can be mass produced in large numbers fairly quickly.
"We took a bit of a risk because we had to buy a lot of materials before we had any orders," says Schwanke. "Even so, it was an easy decision to make. My thinking was ‘if we build them, we can help.'"
Schwanke's thinking turned out to be right on the mark. Initially, Lakeview Industries projected making 500,000 masks. They now expect to ship at least 5 million, and possibly more.
"Our employees are the real heroes in this," says Schwanke. "They're taking a risk to come to work, yet they feel proud to be helping those on the front lines fight this virus. Our team is doing a phenomenal job of turning out these handmade masks as quickly as possible."
From Drones to 3D Masks
Fortem Technologies makes autonomous drones and AI-driven software to protect against malicious drones - products not even remotely related to the medical industry. But when the Provo, Utah police put out an urgent plea for protective masks, Fortem Technologies stepped up to the plate.
Their engineers immediately set to work producing protective masks using the company's 3D printers. Within the first day, they had produced and donated 100 masks to the police department. After adding more 3D printers into the mix, Fortem Technologies is now turning out 200+ masks per day, which are being shipped to other police departments and hospitals from Los Angeles to Texas.
"Making protective masks isn't our core business, so it took some time to figure out the correct specs and ensure the masks are made properly," says Jen Colton, Fortem Technologies' VP of Public and Government Relations. "It's not hard to innovate when you know you can help protect those who are putting their lives on the line for us every day. Once we developed a framework for making the masks, we were able start turning them out in quantity."
Like all businesses, Fortem Technologies is focusing on safety in the workplace. This includes strict adherence to CDC guidelines to work remotely, restrict travel, wash hands frequently and maintain social distancing.
"We're also focused on taking good care of each other, as well as our customers, neighbors and those on the front lines in our community," adds Colton. "We plan to continue printing and delivering as many masks as we can until the need is met."
We Will Get Through This
It feels like every day I get a call from a customer that has increased production or shifted focus to literally save their nation and the world. These are a sample of stories from the family of manufacturers powered by Global Shop Solutions that are helping to defeat COVID-19. When the chips are down, nobody can match the creativity, innovation and problem-solving capabilities of manufacturers. Yet, even these are surpassed by their genuine caring and concern for their country and the communities they live and work in. When we all pull together, we can do amazing things! Cheers to Part II coming soon.
Dusty Alexander, CEO & President
About Global Shop Solutions
We simplify your manufacturing.™ Global Shop Solutions ERP software provides the applications needed to deliver a quality part on time, every time from quote to cash and everything in between including shop management, scheduling, inventory, accounting, quality control, CRM and 25 more. Available in the cloud or on premise, our manufacturing customers benefit from real-time inventory accuracy, improved on-time delivery, lower administrative costs, increased sales and improved customer service. Headquarters in The Woodlands, Texas includes a state-of-the-art R&D facility and Global Shop Solutions training center. Through its offices in the U.S., Mexico, Indonesia, Singapore, Australia, New Zealand and the United Kingdom, the company supports thousands of manufacturing facilities in over 25 countries and nearly 30 industries.
Featured Product
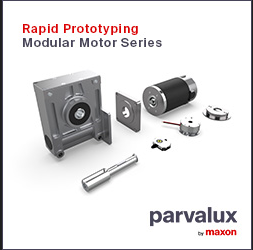
Rapid Prototyping with the Modular Motor Series
Quick to configure. Quick to build. Quick to deliver. Parvalux understands the importance of getting product in the hands of customers quickly and efficiently. The Modular Range does just that allowing customers to configure their own solution, selecting motor and gearbox, adding encoders and brakes to create a solution perfectly suited for their specific applications such as conveyor belt systems, picking systems, parcel sorting equipment, pallet shuttles and automated storage and retrieval systems (ASRS). Read our modular range guide for specifics.