DSM showcases expanded 3D printing portfolio and partnerships at RAPID+TCT 2018
Giving customers more choices speeds 3D printings move into real manufacturing
Royal DSM, a global science-based company active in health, nutrition and materials, will be demonstrating its expanded portfolio of 3D printing materials, for SLA and FFF, at RAPID+TCT 2018 this week in Fort Worth. The company is also announcing a partnership with equipment manufacturer Ultimaker to meet the growing demand for industrial-grade engineering FFF materials.
"Providing customers choices in materials and platforms as they select the right approach for their applications is key to accelerate adoption of 3D printing into industrial manufacturing, beyond prototyping applications", says Hugo da Silva, Vice President of Additive Manufacturing at DSM. "FFF is beginning to burst out of its niche, and DSM has the breadth of thermoplastics materials, the engineering capability, and the understanding of the market to enable additive manufacturing to move into real manufacturing."
Partnership with Ultimaker
To enable end users to easily 3D-print its materials into high quality parts, DSM is partnering with Ultimaker in their alliance program. Combining their material knowledge with Ultimakers insights, gives end users access to a broader scope of professional applications and allows them to print automatically using preconfigured settings available in Ultimaker Cura. This collaboration provides DSM a new route to market, in addition to the existing relationship with Nexeo Solutions 3D for distribution and application development engineering services.
The new partnership underlines DSMs Additive Manufacturing strategy for an ecosystem approach. Partnerships and collaboration across the industry allows DSM to provide customers with the right material for the right platform for specific customer applications, surrounding them with an open and flexible infrastructure.
DSM Additive Manufacturing at RAPID+TCT 2018
At booth 1410, DSM Additive manufacturing will showcase applications with its industrial-grade engineering Novamid polyamide and Arnitel thermoplastic elastomer for FFF 3D printing technology, as well as the Somos materials for SLA and DLP:
• Novamid ID 1030-KS is the first material for FDM/FFF with a UL 94 V-0 rating, enabling the creation of UL-certified small-series FFF/FDM parts for industrial applications. Target parts include fuse boxes, low voltage switch gear, electronic housing, control gear, casings and connectors.
• Arnitel ID 2060-HT offers an excellent combination of properties for demanding automotive applications under the hood such as hot and cold charge air ducts. This new filament is easy to process and can easily be welded, allowing manufacturers / OEMs to significantly reduce the development time of engine components.
• Arnitel ID 2045 is a highly flexible thermoplastic copolymer (TPC) used in electronics, sports and leisure. The bio-based material is 50% made from renewable resources, based on rapeseed oil instead of mineral oil. ISO and USP tested, the material properties make it an excellent material for use in applications such as sports mouth guards and other protective gear.
• Somos Taurus for under-the-hood applications. Somos Taurus is the first SLA material to bring the combination of thermal resistance, mechanical strength and impact performance that until now, has only been achieved in AM using techniques such as FDM and SLS.
DSMs commitment to the ecosystem is also showcased at its booth at RAPID+TCT, where they will host 3D printing machines for different printing technologies: Ultimakers new S5 for FFF 3D printing, and Union Techs SD 250 for SLA 3D printing.
Collaborating with players across the ecosystem is a key focus for the company and they invite you to visit their booth to explore partnership and business model opportunities.
Featured Product
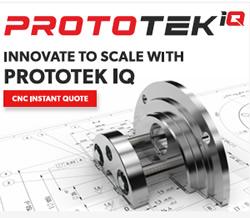
Prototek IQ - Digital Manufacturing Services
Prototek IQ is our new instant quoting platform that simplifies your manufacturing process. With just a few clicks, you can get accurate quotes for 3D printing and CNC machining, which are currently two different platforms. Our easy-to-use interface helps you make smart choices. Use Prototek IQ to improve efficiency and streamline speed to market. We invite customers with experience in large projects, 3D printing, and CNC machining, as well as those with repeat orders, to try our instant quoting platform. You can choose our engineer-assisted quote option if you have unique needs, such as high quantities, specific quality standards, fast delivery, or special finishes.