Desktop Metal Is Set to Change How Metal Is Manufactured with the Fastest Metal 3D Printing System in the World
For the First Time, Affordable, Safe and Precise Metal 3D Printing for Both Prototyping and Mass Production Will Be a Reality Across Industries - at Speeds 100x Faster
BURLINGTON, Mass.--(BUSINESS WIRE)--Desktop Metal, the company committed to making metal 3D printing accessible to global manufacturers and engineers, today launched two systems covering the full product lifecycle -- from prototyping to mass production -- which mark a fundamental shift in how products will be developed and brought to market. The DM Studio and DM Production systems change the rules of traditional metal manufacturing solutions with the advent of first-of-its-kind innovative approaches that reduce costs and significantly increase speed, safety, and print quality.
The first office-friendly metal 3D printing system for rapid prototyping, the Desktop Metal Studio System is 10 times less expensive than existing technology today. The system is a complete platform, including both a printer, starting at $49,900, and microwave-enhanced sintering furnace that, together, deliver complex and even impossible geometries of metal 3D printed parts right in an engineers office or on the shop floor.
The DM Studio System:
Eliminates the need for expensive, industrial facilities to safely house the technology. Unlike traditional metal 3D printing processes, the DM Studio System requires no hazardous powders, no lasers and no cutting tools to operate. Instead the DM Studio System uses Bound Metal Deposition (BMD), a proprietary process, to make accurate and repeatable parts, similar to the safest and most widely used 3D printing process for plastics, Fused Deposition Modeling (FDM) technology.
Makes metal 3D printing drop-dead simple. No need for dedicated operators, the DM Studio System uses cloud-based software to streamline the entire workflow so engineers can go from computer-aided design (CAD) software to printed parts seamlessly. Proprietary Separable Supports make it possible to remove support structures by hand, while swappable print cartridges make for safe, fast material changes.
Significantly increases the versatility of prototyping. Out of the box, the DM Studio System is designed to support hundreds of different metal alloys -- the same metals used to mass produce parts can now be used to prototype them.
To manufacture metal 3D printed parts at scale, Desktop Metal also announced the launch of the fastest 3D printing system for mass production of high resolution metal parts today, the DM Production System. Using new, proprietary Single Pass Jetting (SPJ) technology, the DM Production System is 100 times faster than todays laser-based additive manufacturing systems. For customers, the Production System dramatically reduces the cost-per-part when compared with todays laser-based systems, for the first time making it competitive with mass production techniques like casting.
"Until now, metal 3D printing has failed to meet todays manufacturing needs due to high costs, slow processes and hazardous materials," said Ric Fulop, CEO and Co-founder of Desktop Metal. "With a team of some of the worlds leading experts in materials science, engineering and innovation, Desktop Metal has eliminated these barriers by developing metal 3D printing systems that can safely produce complex, strong metal parts at scale."
Since its inception in October 2015, Desktop Metal has raised $97 million and attracted major investors, including GV (formerly Google Ventures), BMW Group, GE, Lowes, NEA, Kleiner Perkins Caufield & Byers, Lux Capital, Saudi Aramco, and 3D printing leader Stratasys. With over 138 patents filed and a growing team of more than 100 employees, Desktop Metal continues to gain momentum as it brings its products to market. Members of the founding team, in addition to Fulop, include some of the most forward-thinking innovators in the industry: Jonah Myerberg, Chief Technology Officer and a leader in materials engineering; Ely Sachs, MIT professor and early pioneer of 3D printing, inventor of binder jet printing; Yet-Ming Chiang, MIT professor and one of the worlds top materials scientists; Christopher Schuh, Chairman of the MIT Dept. of Materials Science & Engineering and one of the worlds leading metallurgists; A. John Hart, MIT professor and expert in manufacturing and machine design; and Rick Chin, VP of Software, who was one of the early team members of SolidWorks and previously founder of Xpress 3D (acquired by Stratasys).
"The rapid pace of innovation in technology is enabling OEMs to design, produce and deliver their products differently. I see a huge potential for the highly competitive automotive industry to accelerate product development and production," said Uwe Higgen, Managing Partner of BMW i Ventures. "Desktop Metals technology offers a new way for the manufacturing industry to be smarter, faster and more cost effective with metal 3D printing. Whether its rapid prototyping or output at scale, a solution for printing metal parts that is competitive to the traditional manufacturing processes is certain to change the face of automotive design and production."
"Caterpillars Parts Network has twenty-one distribution centers around the world that hold hundreds of thousands of service parts to provide over 2,000 dealer locations with the parts needed to provide our customers with their expected uptime," said Don Jones, Caterpillar Global Parts Strategy Manager. "By leveraging a portion of 3D printing for metal parts, we will be able to enhance best in class service with lower inventory investment. We are excited to evaluate the Desktop Metal suite of products, which will allow us to print metal parts at high speed and minimal post processing and environmental constraints closer to our customers, reducing the need to expedite ship critical parts from across the globe."
The DM Studio System is available to reserve in May with shipping beginning in September 2017. The Studio printer is available for $49,900 and the complete system, including printer, debinder, and furnace, is $120,000. The DM Production System is available on reserve in May for shipping beginning in 2018.
About Desktop Metal
Desktop Metal, Inc., based in Burlington, Massachusetts, is accelerating the transformation of manufacturing with end-to-end metal 3D printing solutions. Founded in 2015 by leaders in advanced manufacturing, metallurgy, and robotics, the company is addressing the unmet challenges of speed, cost, and quality to make metal 3D printing an essential tool for engineers and manufacturers around the world. For more information, visit www.desktopmetal.com.
Featured Product
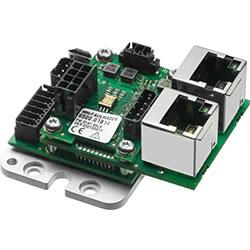