Amada Miyachi Europe offers Weld Monitoring Devices to Support Quality System Requirements
Amada Miyachi Europe announces powerful high performance weld monitoring equipment ideal for process development, production monitoring, data collection and analysis to support quality system requirements. Amada Miyachi Europe weld monitoring devices can be smoothly integrated into the production process, providing precision real-time dynamic measurement of all welding variables.
Amada Miyachi Europe announces powerful high performance weld monitoring equipment ideal for process development, production monitoring, data collection and analysis to support quality system requirements. Amada Miyachi Europe weld monitoring devices can be smoothly integrated into the production process, providing precision real-time dynamic measurement of all welding variables. Available options include the MG3 Digital Weld Monitor and the Advanced Data Analysis Monitoring (ADAM) system.
With increased emphasis on accountability, the MG3 Digital Weld Monitor offers the tools required for process development, production monitoring, data collection, and analysis to support ISO, GMP and TQM requirements. The high-performance MG3 Digital Weld Monitor offers all the tools required for micro resistance welding applications, including process development, production monitoring, data collection, and analysis to support ISO, GMP and TQM requirements. Featuring two independent measurement channels, the MG3 Digital Weld Monitor offers oscilloscope functions with zoom and cursor modes, full on-screen SPC capability, and an integrated clock and date for weld reporting and traceability.
Representing the very latest technology in resistance weld monitoring, Amada Miyachis Advanced Data Analysis Monitoring (ADAM) allows the operator to measure current, voltage, force, displacement, and cover gas flow/auxiliary input. It features a modern PC infrastructure to conveniently import and export saved data. Equipped with a large 22-inch colour widescreen monitor, ADAM allows users to view several charts conveniently. Users know what happens during the weld, as well as what happens before the weld is triggered. Sophisticated statistical process control (SPC) capabilities, including an integrated database and Minitab 15® statistical software, enable customers to analyse and collect data.
Other key features include high resolution sensors; pre-and post-trigger viewing; envelope limits; and Ethernet communications capability. ADAM also supports ISO, GMP and TQM requirements.
Featured Product
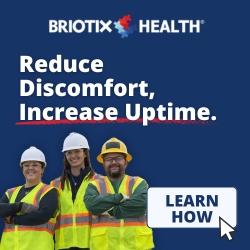