Revolutionizing Manufacturing: Jiepu Unveils the Hidden Potential of Die-Cutting Technology
In a world where precision and efficiency are paramount, die-cutting technology has quietly transformed industries ranging from packaging to automotive. Yet, many manufacturers still struggle with outdated processes, missing out on the full potential of this innovative method.
Have you ever wondered why some companies achieve flawless results while others face recurring challenges like wasted materials or inconsistent cuts? The answer lies in understanding the fundamentals of die-cutting and leveraging advanced techniques tailored to your needs.
Jiepu, a leader with over 20 years of expertise in die-cutting solutions, is shedding light on the key terms and trends shaping this field:
What makes rotary die-cutting ideal for high-speed production?
How can eco-friendly materials redefine sustainability in your industry?
Why is automation the key to unlocking higher efficiency?
These questions are just the beginning. Jiepu's comprehensive insights not only decode the complexities of die-cutting but also provide actionable strategies to overcome common challenges.
Modern die-cutting is more than a production tool—it's a pathway to innovation. Automation has streamlined processes, while advances in customization enable manufacturers to create unique, market-leading products. Additionally, the growing focus on sustainable materials is paving the way for eco-conscious solutions without compromising quality.
Ready to elevate your manufacturing game? Jiepu is here to help. Our proven expertise and cutting-edge technology empower you to stay ahead in a competitive market.
Learn More About Jiepu's Die-Cutting Solutions:https://www.diecut123.com/die-cutting-process-key-terminology-explained
Let's work together to turn your manufacturing challenges into opportunities for growth and success.
Featured Product
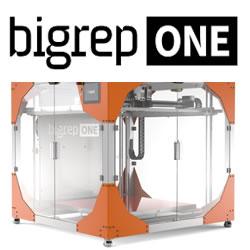
BigRep ONE: Large-Scale 3D Printing
The BigRep ONE is an award-winning, large-format 3D printer at an accessible price point. With over 350 systems installed worldwide, it's a trusted solution for prototyping and production by designers, innovators, and manufacturers alike. Featuring a massive one-cubic-meter build volume, the fast and reliable ONE brings your designs to life in full scale.