TRUMPF Uses AI to Improve Laser Cutting Edges
New “Cutting Assistant” uses AI (Artificial Intelligence) to independently determine laser cutting parameters // Solution is available for TruLaser machines with a power of 6 kW or higher, purchased after May 2025 // Users save time and counteract the skilled worker shortage
Farmington, Conn., April 24, 2025 - High-tech company TRUMPF is introducing a new "Cutting Assistant" application, which employs artificial intelligence to help users improve the quality of laser-cut edges. Production employees just take a picture of their component's cut edge with a hand scanner. Then, the solution assesses the edge quality, evaluating it using objective criteria such as burr formation. With this information, the Cutting Assistant's optimization algorithm suggests improved parameters for the cutting process. Then the machine cuts the sheet metal once more. If the part quality still does not meet expectations, the user has the option to repeat the process. This solution is available for all TruLaser series laser cutting machines purchased as of May 2025, which feature a power output of 6 kW or higher.
"With the Cutting Assistant, TRUMPF is once again demonstrating how we are pioneering the use of AI in industrial manufacturing," says Grant Fergusson, TRUMPF Inc. TruLaser 2D laser cutting product manager. "The Cutting Assistant is a great example of how AI-enabled tools can help overcome problems related to the skilled worker shortage and also saves time and money. When it comes to productivity, this application creates a competitive edge for fabricators."
AI evaluates edge quality and makes optimization suggestions
When laser cutting, fabricators can find it challenging to determine the correct parameters to use for their material grades. Materials that are not optimized for laser cutting often produce edges with wide variations in cut quality, forcing production employees to constantly change the technology parameters. This involves adjusting each individual parameter one by one— a process which demands a lot of time and employee experience. This presents a challenge for many companies, especially those with inexperienced workers in production positions. By integrating the Cutting Assistant into the machine software, optimized parameters can be transferred seamlessly into the software without the need for programming. This saves time and reduces errors.
Further improvements planned for Cutting Assistant
While developing the Cutting Assistant, TRUMPF experts cut thousands of parts and drew upon many years of expertise, using their extensive knowledge to train the software's algorithm. For TRUMPF, this work on the Cutting Assistant continues. In the future, data from applications in the field will also be incorporated into the solution. This will enable faster and more reliable results, because the self-learning system will continuously improve. Through all of this, TRUMPF ensures that the algorithm does not distribute the user's expertise.
"Manufacturers and users alike benefit from this novel development approach. Of course, data security remains a top priority for TRUMPF," says Fergusson.
TRUMPF regularly provides users with online updates that they can download to their machines for maximum productivity and quality.
Featured Product
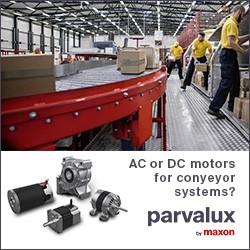