The True Complexity of SMT Machine CPH Calculations
In the realm of Surface Mount Technology (SMT), the efficiency of a production line is often gauged by the metric known as Components Per Hour (CPH). At first glance, calculating CPH appears straightforward: divide the number of components placed by the time in hours. However, this simplistic approach belies the intricate factors that significantly influence the actual performance of an SMT line.
Traditionally, manufacturers provide CPH specifications in two ways: "Maximum CPH," representing the peak speed achieved under ideal conditions, and figures based on standards like IPC-9850, which categorise CPH by package type.
While these metrics offer a baseline, they often fail to account for the dynamic variables present in real-world production environments.
Several critical elements can cause a substantial disparity between theoretical CPH and actual output:
Machine Downtime: Unplanned stoppages due to maintenance or technical issues can drastically reduce productivity.
Changeover Times: In high-mix, low-volume setups, frequent changeovers are necessary, leading to increased downtime and reduced CPH.
Component Variability: Different components may require varying placement times, affecting the overall throughput.
Operator Efficiency: The proficiency of the personnel operating the machines plays a pivotal role in maintaining optimal performance.
Board Complexity: More complex board designs can lead to longer placement times and increased chances of errors.
To bridge the gap between theoretical and actual CPH, it's imperative to adopt a holistic approach that encompasses these variables. This involves:
Comprehensive Performance Metrics: Beyond CPH, metrics such as Overall Equipment Effectiveness (OEE) provide a more nuanced view of production efficiency, considering factors like availability, performance, and quality.
Regular Maintenance and Training: Ensuring machines are well-maintained and operators are adequately trained can mitigate downtime and enhance performance.
Process Optimisation: Streamlining changeover procedures and optimising component placement strategies can lead to significant improvements in throughput.
Advanced Simulation Tools: Utilising modelling tools to simulate SMT line performance under various scenarios can help in identifying potential bottlenecks and areas for improvement.
Featured Product
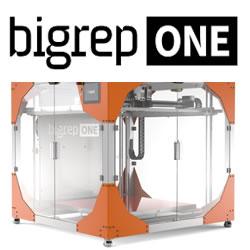