CRP Technology Introduces Vapor Smoothing to Boost Surface Quality and Performance of Windform Materials
The Italy-based company specializing in 3D printing services has expanded its suite of production and post-processing capabilities, offering clients a fully integrated process from additive production to final inspection. Vapor smoothing can be applied to stand-alone Windform parts or following manual finishing, further enhancing the already high-performance characteristics of Windform materials.
CRP Technology, a leader in advanced 3D printing services, has introduced vapor smoothing into its production department, enhancing the surface quality and mechanical properties of 3D-printed parts in Windform composites. Known for their strength, light weight, and durability, Windform materials now gain the additional benefits of this innovative post-processing technique, which seals micro-porosities to produce smoother, more resilient surfaces. This service addresses the stringent requirements of industries such as aerospace, automotive, and motorsport.
Aesthetic and Functional Advantages
Vapor smoothing can be applied directly to Windform parts, creating a surface finish comparable to plastic injection-molded components. Alternatively, it can be combined with manual finishing—a hallmark of CRP Technology's expertise—to achieve a flawless finish that often eliminates the need for painting, thus reducing both cost and weight. This dual option makes vapor smoothing especially versatile, allowing clients to tailor it to specific requirements.
CRP Technology also provides stand-alone vapor smoothing services for existing SLS or MJF parts, particularly for black-colored components.
"We integrated this service to elevate the parts we produce in Windform while preserving the mechanical excellence for which these materials are known," says Franco Cevolini, CEO and CTO of CRP Technology. "For applications requiring aesthetics, durability, and weight efficiency, vapor smoothing provides a distinct advantage on parts that are already world-class, thanks to Windform. In contrast, some 3D printing service providers use vapor smoothing simply to make lower-grade parts more acceptable."
Expanding Capabilities in Critical Sectors
In motorsport, vapor smoothing optimizes airflow by reducing surface roughness, enhancing aerodynamics and overall performance. In aerospace, it improves the surface finish needed for components exposed to extreme conditions, ensuring precision and durability for mission-critical applications.
End-to-End Solution for High-Performance Parts
With vapor smoothing now part of CRP Technology's comprehensive post-processing services, clients receive an end-to-end manufacturing process covering every stage from additive production to final inspection. Parts in Windform can also undergo CNC machining for high-precision detailing, and each part is subject to rigorous quality checks to ensure consistency and reliability.
This integrated approach further strengthens CRP Technology's position as a leader in advanced manufacturing with composites, providing clients with versatile solutions that meet the highest standards of form and function.
Featured Product
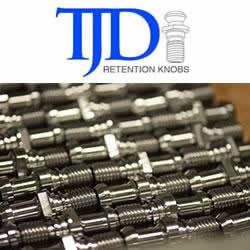