IoT and connected devices are making the development process more transparent. The technology also allows plant managers and overseers to accurately review operations, which leads to a more positive direction for everyone.
Tips and Tricks for Implementing Automation in Your Manufacturing Plant
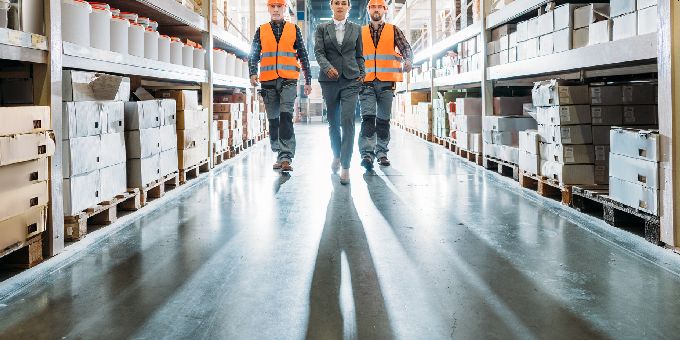
Megan Ray Nichols | Schooled By Science
Modern technology is transforming the world by generating opportunities that weren't available just a decade ago. In manufacturing, for example, IoT and connected devices are making the development process more transparent. The technology also allows plant managers and overseers to accurately review operations, which leads to a more positive direction for everyone.
As efficiency and productivity become the core focus of many factories and plants, automation and advanced robotics enter the spotlight. Most automated machinery and tools can operate at an optimal level, as well as improve working conditions for those spending the most time inside such facilities. Robots can take over rote tasks, freeing up human workers to handle more exciting duties. They can also be used in place of people for dangerous or risky tasks.
Thus the idea of cobots, or collaborative robots, comes into the fold. They are robotic devices, tools and machinery meant to work alongside humans as opposed to replacing them outright. It's a synergistic approach to automating and optimizing the factory floor of tomorrow.
However, while many of these technologies are promising and offer considerable benefits, there are some things you should know before deploying them in your factories or plants.
Start Small to Win Big
Automation can be very costly, but it's likely you know that already. This is not unlike making a machinery or equipment change in the conventional sense. It takes time and money, and it requires lots of human resources to replace or redesign a factory floor.
That's why it's safer and more useful to start small when implementing automation. Choose a process or particular step to automate that will be highly beneficial for everyone. This allows you to dip your toes in the water as far as implementing and maintaining automation, but it affords the same to your workforce. They get experience working alongside such equipment, which helps everyone reach a level of optimal performance.
When you buy automation machinery — especially assembly-based automation — you're not walking into a warehouse and picking out a complete product. You'll need to tailor equipment choices to your plant's regular operation. Different assembly pieces are ideal for certain situations, so you'll want to do some research before settling on a new piece of equipment.
As you and your workforce grow to understand the automation setup better, you can begin expanding and slowly implementing more processes and tools.
Of course, another solution is to look into robot-as-a-service providers, which work similar to software-as-a-service in that you are essentially renting the equipment from an experienced provider as opposed to buying it outright.
Plan for Growth
If you're building a brand-new facility or plant from scratch, this is less a concern. However, if you're upgrading an existing facility with legacy hardware, you'll need to consider your boundaries. Do you throw everything out all at once and start over, or do you replace equipment bit by bit? Furthermore, how do you handle future expansion?
With a budding business, you always want to leave or make room for future growth. That's not saying you should leave entire segments of your plant or facility empty, but you'll need to consider how and what you're going to do when it comes time to expand.
What part numbers, machines and future equipment would you like to implement? What are the best ways to do this, and is there a requirement for how you should go about it? Do you need to replace or install another piece of equipment first?
Plant assembly is always going to be a multistep process, which means you and your workforce must be ready at all times. Plan ahead. Scope out the various hardware you might need or want, find prices or solicit quotes, and consider what must be done to make room or deploy said machinery. One machine, for example, might be much smaller than previous equipment, which leaves you ample room to add new tools. The opposite may also be true when a newly assembled system is much larger than anything you used in the past. Be ready to accommodate for these things.
Design for Components
There are various types of equipment and hardware, and that means they all come with unique features, parts and uses. Look at what you are doing currently within your plant, and choose systems that align with said functionality.
That means designing your new equipment or assemblies based on the components they offer. Are you going to need cameras, custom sensors, PLCs, motors or drives, or even human-machine interfaces (HMIs)? Find out what you need by going to your engineers and floor workers and surveying how they use the current systems, what they might require out of something new or even what brands they trust.
Don’t be afraid to think outside the box, either — or outside the walls of your plant. Tools like SourceESB allow you to select, organize and research all the various parts or assemblies you might need for a new system. It can be an invaluable tool, especially when you want to confirm or double-check compatibility across several different distributors.
Consider Intellectual Property for Developed Systems
You'll be working closely with an integrator or systems team that knows the hardware and assemblies you're trying to build. During the project, everyone will collaborate to come up with something custom yet efficient that meets the needs of your business. Once everything is said and done, those integrators will move on to help other teams and other companies optimize their equipment.
They may borrow or reuse the design you created collaboratively to make their job easier. This isn't always a big deal, mainly if your integrator invested more time developing the systems than your internal teams, but it's something to consider.
Who owns the intellectual property of the finished systems and assemblies? Do you want to restrict the reuse of designs or plans?
Mind Your Documentation
No one enjoys putting together thorough documentation for any system, let alone custom assemblies and machinery. However, it's a necessary evil — especially if you hope to pass the torch to another team or management crew. The resources will be essential to upgrade, amend or even repair equipment in the future.
One might consider developing and maintaining a central documentation repository for all necessary resources.
Luckily, when working with integrators, you can establish a proper protocol for creating and receiving documentation, be it a digital CAD format or paper schematics.
If you follow the guidelines or tips discussed here when exploring automation and advanced robotics, you’ll come out on top. A more successful deployment is likely with lowered risks and fewer obstacles, making your plant more efficient now and in the future.
The content & opinions in this article are the author’s and do not necessarily represent the views of ManufacturingTomorrow
Comments (0)
This post does not have any comments. Be the first to leave a comment below.
Featured Product
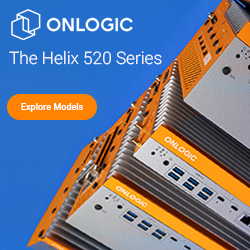