In the realm of manufacturing precision, the assurance of product packaging integrity takes center stage. Using thermal cameras for in-line seal strength testing has revolutionized quality control and efficiency in the packaging industry.
In-Line Seal Strength Testing Using Thermal Cameras
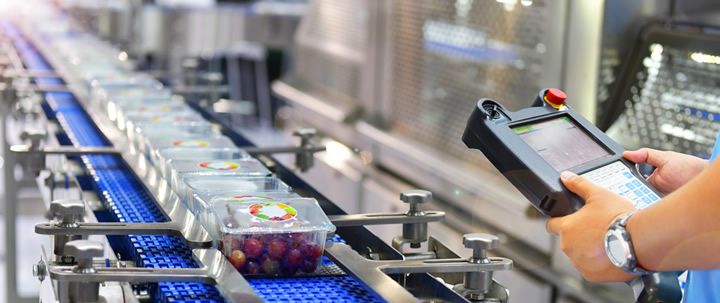
Article from | MoviTHERM
In the realm of manufacturing precision, the assurance of product packaging integrity takes center stage. Using thermal cameras for in-line seal strength testing has revolutionized quality control and efficiency in the packaging industry.
Why Seal Strength Tests Matter
Seal strength tests are vitally important in manufacturing because they determine how well product packaging holds up. The results significantly affect how long products like food, beverages, and pharmaceuticals stay fresh and safe.
Ensuring that package seals are strong is not just a routine step but a crucial measure to prevent issues like leaks and contamination. Seal strength tests play a key role in safeguarding product quality, reducing waste, and maintaining customer satisfaction.
Traditional Seal Strength Testing Methods and Their Challenges
Traditional seal strength testing methods have long been the stalwarts of quality control in manufacturing, yet they come with inherent challenges. These methods often involve sampling a limited number of packages, leaving a substantial portion unchecked and potentially harboring defects.
The use of vacuum chambers, for example, while effective in detecting leaks, is time-consuming and introduces the possibility of human error. Placing packages in a vacuum chamber and submerging them in water to detect leaks may not address all packages produced, leading to undetected faults that could compromise product quality.
As industries evolve and demand higher quality, the limitations of these conventional approaches become more apparent, paving the way for innovative solutions like in-line seal strength testing using thermal cameras.
Using Thermal Cameras for Seal Strength Testing
Thermal cameras are an effective tool for checking package seals right on the production line. Thermal cameras examine the seals of packages right after they’ve been heat sealed. They detect temperature differences on the surface of the packaging, essentially “seeing” the leftover heat from the sealing process. With real-time analysis, it speeds up the production line, making the packaging process more efficient.
Integrating thermal cameras into the production line ensures a fast and consistent inspection process. Using this method helps cut downtime by quickly spotting and fixing defective packaging before it causes disruptions. By implementing thermal cameras into your process line, you can automate your inspection process to provide reliable results. This lowers the risk of human error that can happen with manual inspections.
In-line thermal seal inspection brings advanced technology right into the heart of the production process. It raises the bar for quality control and ensures that every packaged product meets the highest standards of safety and reliability.
Packages Suitable for Thermal Inspection
Thermal seal inspection can work for different types of packaging, such as:
- Flexible Packaging – This includes pouches, bags, and sachets made from plastic films, aluminum foil, and paper.
- Rigid Packaging – This includes trays, clamshells, and blisters made from plastic, glass, and metal materials.
- Sealed Containers – This includes cans, jars, and bottles made from glass, plastic, and metal.
- Pharmaceutical Packaging – This includes blister packs, pouches, and bottles used for medication.
- Food Packaging – This includes trays, bags, and bottles used for food and beverage products.
MoviTHERM TSI for Heat Seal Testing
MoviTHERM’s TSI is a seal inspection system that uses a thermal camera to assess the quality of heat seals. The automated inspection system compares unknown package seals to known good seal profiles and reliably detects good and bad seals. MoviTHERM TSI has an integrated recipe manager that allows the system to store hundreds of inspection scenarios. It also allows for system adaptation to various packaging seal inspection applications.
Core features of MoviTHERM TSI include:
- Infrared Cameras that view and measure thermal variations of good and bad seals without contact.
- Hardware and software that easily integrates with existing production equipment.
- Advanced and reliable inspection logic pre-programmed for multiple packaging scenarios.
- Image and data logging for traceability of performance.
TSI Inspection Software
The TSI user interface is designed to be user-friendly and accessible through touch screen technology. All buttons and features on the interface can be easily operated by simply touching the screen.
In this particular example, the TSI user interface is being used to inspect bottle caps. The interface provides a visual representation of the inspection process, allowing the user to easily identify any issues or defects.
One of the key features of the TSI user interface is the thermal image display. In this example, the thermal image shows a bright yellow ring around the bottle cap. This indicates that the seal on the cap is good and meets the required standards.
To further confirm the quality of the seal, the interface also includes an indication window. In this window, a green “PASS” message is displayed, indicating that the seal has passed the inspection and is considered to be of high quality.
Overall, the TSI user interface provides a comprehensive and intuitive platform for inspecting bottle caps. Its touch screen accessibility and clear visual indicators make it easy for users to navigate and interpret the inspection results.
What’s Included with MoviTHERM TSI?
MoviTHERM TSI solution provides 100% in-line, high-speed integrity inspection for heat-related production lines.
The system includes:
- High performance thermal camera
- Standard powder-coated Industrial Electrical Enclosure (Optional
- Stainless-Steel enclosure for food & beverage or pharmaceutical environments)
- Touch-Screen PC and application specific software GUI interface
- Interactive inspection Recipe Programmer to accommodate multiple products – or to try different “what-if” scenarios
- Robust bi-directional PLC interface to transfer status messages and
- PASS/FAIL results to a plant PLC (Ethernet/IP or Modbus)
- Image FTP to transfer fault images to a remote server for off-line review
Use Case Examples
Thermal Seal Inspection (TSI) emerges as a highly effective solution for ensuring the integrity of various types of packaging sealed with heat. This innovative technology plays a pivotal role in maintaining the quality and safety of packaged products, particularly in industries like food, beverage, and pharmaceuticals.
Let’s delve into specific applications of TSI and how it contributes to the inspection of different types of sealed packages:
Bag Seal Integrity Inspection
- Scenario: Bags leaving the heated press or sealed with hot glue.
- How it Works: TSI capitalizes on the residual heat retained by bags after the sealing process. This residual heat serves as a key indicator that can be accurately detected and inspected by TSI. The technology ensures that the seal conditions are thoroughly evaluated, providing insights into any potential faults.
MoviTHERM TSI for Bottle Cap Seal Integrity Inspection
Bottle Cap Seal Integrity Inspection
- Scenario: Induction sealer creating heat in the foil section of the sealing packet.
- How it Works: TSI extends its capabilities to assess the integrity of bottle cap seals. In instances where an induction sealer generates heat in the foil section during the sealing process, TSI steps in to evaluate the residual heat. This evaluation aids in identifying the seal condition and detecting specific fault types, if present.
MoviTHERM TSI for Pouch Seal Integrity Inspection
Pouch Seal Integrity Inspection
- Scenario: Seams formed by heat and pressure in pouch-forming processes.
- How it Works: TSI proves invaluable in assessing seams created through a combination of heat and pressure in pouch-forming processes. By comparing the thermal profiles of test samples to known non-leakers, TSI efficiently detects leaks in pouches. This method ensures a comprehensive evaluation of pouch seal integrity.
MoviTHERM TSI for Package Seal Integrity Inspection
Thin Film Plastic Covered Packages Inspection
- Scenario: Common in the food industry.
- How it Works: TSI excels in the inspection of thin film plastic-covered packages, a prevalent packaging type in the food industry. This technology swiftly and reliably identifies the seal area, allowing for the detection of seal integrity. This is particularly critical for ensuring the safety of food products, providing consumers with confidence in the quality of packaged items.
Conclusion
Thermal cameras for in-line seal strength testing have revolutionized quality control. Seal strength tests are vital for products like food and pharmaceuticals. Traditional testing has limitations, making way for innovative in-line thermal camera testing. This real-time approach on production lines reduces downtime, cuts waste, and improves product quality.
MoviTHERM’s TSI system is a leading solution for this. It ensures reliability and safety across various packaging types. In-line thermal seal inspection with thermal cameras proactively enhances quality control, prevents defects, and meets industry standards.
The content & opinions in this article are the author’s and do not necessarily represent the views of ManufacturingTomorrow
Comments (0)
This post does not have any comments. Be the first to leave a comment below.
Featured Product
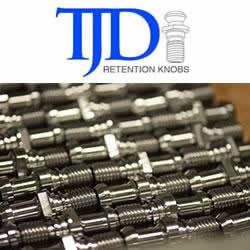