Despite its higher cost and longer development and deployment times, custom manufacturing software is becoming more and more in demand across all sectors as, according to Capterra, 61% of manufacturers already prefer somewhat customized solutions.
When to Choose Custom Manufacturing Software: Top 7 Use Cases
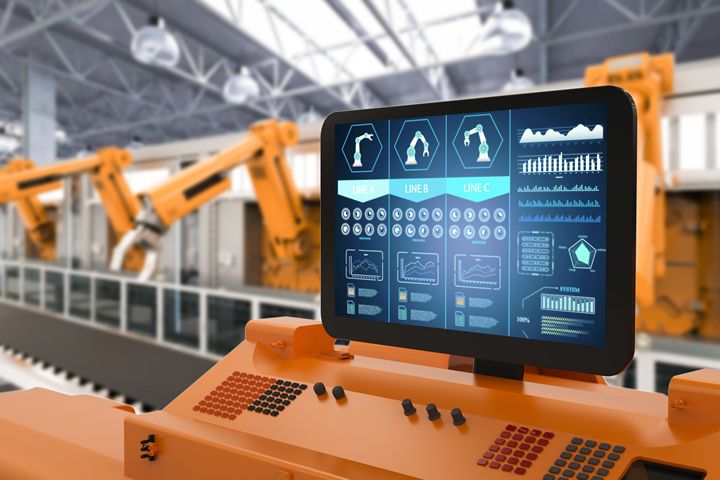
Article from | Itransition
So, in this article, we explain when developing custom manufacturing software is a wise choice.
Case 1. Administration of complex manufacturing processes
Manufacturers in niches like aerospace, automotive, biotechnology, or oil processing industries have complex, interdependent operations that require precise coordination. Their multi-step production process typically involves several teams, and smooth communication between them is crucial.
Why choose custom software: Manufacturers can equip their software with all the necessary features to manage numerous administrative tasks within their complex production workflows. For example, dedicated HR modules can generate production schedules based on the priority of orders and the availability of equipment and resources. What’s more, manufacturers can add collaboration tools to their production software to improve communication and task management across teams. Additionally, tailored data analytics solutions can provide real-time visibility into manufacturing operations and offer insights into workflow optimization.
Case 2. Products with custom configurations
Manufacturers of bespoke goods, such as custom-made motorcycles, cars, furniture, or apparel, offer a wide range of design and material options to meet their customers' exact preferences. However, to deliver a product that aligns with customers' specifications, manufacturers need to precisely capture order details and then closely control the product’s quality.
In addition, due to the high variability of orders, manufacturers can’t accurately plan the needed quantities of specific components and materials. That’s why, to prevent overstock and cut down inventory expenses, custom goods manufacturers try to produce items closer to the time when they are needed. However, it requires more precise supply chain management.
Why choose custom software: A customer-facing tailored solution can provide configurators, 2D or 3D visualization, and real-time pricing change to help customers select among available product options. Additionally, custom quality control software can be equipped with tailored capabilities like the generation of product-specific checklists to help ensure that each product aligns with its unique specifications.
What is more, custom inventory software can incorporate dynamic reordering algorithms that take into account high variability in demand and lead times for materials and components. Since such solutions are very flexible, they would be particularly beneficial for custom manufacturers with multi-level bill-of-material structures.
Case 3. Extensive integration needs
Manufacturing operations typically involve a wide array of machinery and software that needs to be interconnected to exchange production data. Manufacturers can also often integrate their systems with their suppliers’, customers’, and partners’ solutions. Besides, as a company expands its operations or adopts new technologies, it needs to ensure that new equipment and solutions are properly connected to the existing IT infrastructure.
Why choose custom software: By opting for custom software, manufacturers can tailor it to the integration requirements of the existing IT ecosystem. For instance, solutions can be developed with well-defined APIs that simplify the establishment of smooth communication with other solutions. Also, if the software is equipped with data mapping and transformation features, it can translate data from other systems into a compatible format and facilitate data exchange.
Building their manufacturing software using a modular architecture, manufacturers simplify the addition of integration modules that connect it to new IT infrastructure components, including other manufacturing solutions. Besides, custom solutions are designed with user-friendly interfaces to simplify the configuration and monitoring of integrations.
Case 4. Fast-changing market demands
Trends in apparel, home electronics, cosmetics, food and beverage, and other consumer goods change quickly. So, to stay competitive, manufacturers have to quickly develop, produce, and bring new items to market, adjusting production schedules and resource allocation accordingly.
Why choose custom software: Custom solutions can accelerate product development processes to bring new products to market faster. In particular, computer-aided design (CAD) software can offer a toolset, convenient interfaces, and automation capabilities tailored to meet a manufacturer’s needs for quick prototyping and modeling. Thus, due to their high flexibility, custom MESs help develop new models or features much faster.
Case 5. Strict compliance requirements
Highly-regulated pharmaceutical, aerospace, or medical device manufacturers often must comply with numerous regulations and standards. The compliance requirements can apply to various processes, from research and development to production and quality control, and are regularly updated to align with advances in technology and science and new public health concerns. For manufacturers in such strictly regulated niches, a compliance breach can lead to fines, legal actions, product recalls, and reputational damage.
Why choose custom software: Tailored manufacturing solutions like MES or QMS can incorporate real-time monitoring of relevant compliance parameters throughout the production process. Such software can collect and process information about temperature, humidity, chemical composition, or equipment performance with the help of sensors and other integrated IoT devices.
If there’s a deviation from set parameters, the system can alert the employees or trigger predefined actions, such as halting the production line or adjusting machine settings. In addition, custom solutions can be designed to synchronize real-time updates from specific regulatory bodies, helping manufacturers to adapt to new requirements faster.
Case 6. Sensitive manufacturing data
While all manufacturers must safeguard their operations from potential cyberattacks, for some, security is paramount. Companies working on classified projects within aerospace, defense, nuclear power, pharmaceuticals, biotechnology, and other sectors handle substantial volumes of sensitive data, including research specifics, proprietary designs, personnel records, and supply chain information.
Why choose custom software: Manufacturers that handle confidential information should opt for custom solutions because they can be equipped with optimal security controls, including robust authentication and authorization mechanisms, advanced encryption, real-time security monitoring and alerts, and more. These solutions can also be developed with highly secure APIs for integrations with the systems of suppliers, partners, and customers to ensure safe data exchange.
Case 7. Skilled labor shortage
Skilled manufacturing workers are in high demand today, so many companies have to compete for workers. Also, as manufacturing technologies and processes evolve, existing workers and new hires often lack necessary skills.
Why choose custom software: Custom software, such as MES or SCADA solutions, can efficiently automate specific routine operations. For example, it can be configured to send commands to start or stop the operations of robots, CNC machines, and assembly lines or adjust their speed and precision. Such automation can free up the existing specialists to focus on more complex tasks.
As for employee upskilling, manufacturers can benefit from developing custom learning software, especially featuring simulators and smart recommendation systems. Such solutions can analyze the workforce’s skill gaps and suggest customized learning paths that closely mirror the actual production environment and processes, making the training highly relevant and efficient.
To sum up
Custom solutions are developed to address unique manufacturers’ needs end-to-end. They can help streamline complex processes, facilitate better integration and data exchange with existing systems, better meet strict security and compliance requirements, address skilled labor shortages, create unique products, and adapt faster to market changes. In the long run, their adoption helps cut expenses, foster customer loyalty, and increase revenue. That's why the demand for custom software is growing as the manufacturing industry becomes increasingly competitive.
The content & opinions in this article are the author’s and do not necessarily represent the views of ManufacturingTomorrow
Comments (0)
This post does not have any comments. Be the first to leave a comment below.
Featured Product
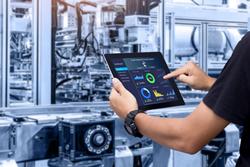