The aerospace industry constantly pushes the boundaries of what's possible, and the demand for advanced manufacturing techniques has never been more critical. This pursuit of innovation has led to a significant shift toward 3D metal printing.
Why 3D Metal Printing Is Key to the Future of Aerospace Engineering
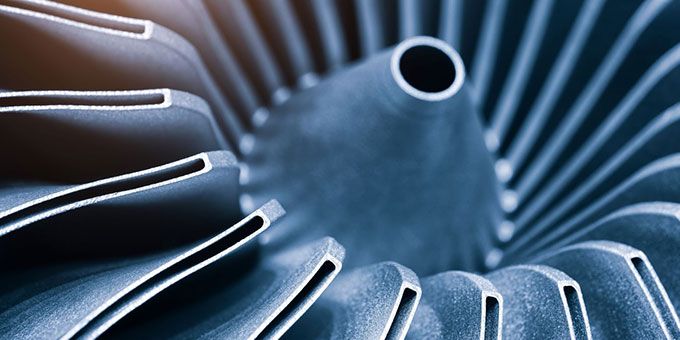
Doug Walker | Fictiv
When fabricating aerospace components, it’s essential to follow rigorous standards for safety and performance. Traditional manufacturing processes, such as casting and machining, have long been the backbone of the aerospace industry. However, these methods have limitations, especially at the forefront of creating complex, lightweight, and highly customized components.
3D metal printing, also known as additive manufacturing, has emerged as a game-changer for the aerospace industry. This innovative technology allows manufacturers to create three-dimensional objects by adding material layer-by-layer, rather than subtracting from a solid block.
Let’s examine the exciting potential 3D metal printing has for the future of aerospace manufacturing.
What new possibilities has 3D metal printing in aerospace unleashed?
The aerospace industry constantly pushes the boundaries of what's possible, and the demand for advanced manufacturing techniques has never been more critical. This pursuit of innovation has led to a significant shift toward 3D metal printing.
This cutting-edge technology is revolutionizing the way aerospace components are designed, offering a myriad of advantages that traditional methods struggle to match. 3D metal printing makes it possible to create intricate geometries and lightweight structures, reduce material waste, and expedite rapid prototyping.
Here’s a closer look at four ways 3D metal printing is propelling aerospace engineering into the future:
-
Complex Geometry: Aerospace components often require intricate designs to optimize their performance and efficiency. Traditional manufacturing methods, such as casting and machining, have limitations in producing complex shapes. 3D metal printing, on the other hand, excels at creating intricate geometries that were once deemed impossible or economically unviable.
-
Lightweight Structures: Weight reduction is a crucial factor in aerospace design. Lighter aircraft consume less fuel, produce fewer emissions, and are more maneuverable. 3D metal printing allows engineers to create structures that are up to 60% lighter with optimized internal geometries, reducing the overall weight of components without compromising strength.
-
Reduced Material Waste: Conventional manufacturing processes often produce significant material waste due to the need for subtractive machining. In fact, aircraft manufacturers cut away up to 90% of the material when fabricating metal parts. However, 3D metal printing is an additive process, so it only uses the material required for the final component, minimizing waste and conserving resources.
-
Rapid Prototyping: The aerospace industry thrives on innovation and iteration. 3D metal printing offers rapid prototyping capabilities, enabling engineers to design, print, and test components quickly and smoothly. This accelerated development process significantly reduces time-to-market and production costs for new aircraft and technologies.
As aerospace engineers continue to explore the limitless possibilities this technology affords, we can expect even more groundbreaking innovations, greater fuel efficiency, and reduced environmental impact in the aviation sector. With 3D metal printing, the sky is not the limit; it's just the beginning of a remarkable journey into the future of aerospace design and manufacturing.
What are the material innovations of 3D metal printing?
In the dynamic world of aerospace engineering, manufacturers continually pursue materials that marry strength, durability, and lightweight properties. The remarkable capabilities of 3D metal printing give engineers a chance to push the envelope of possibilities, and advancements in materials have been essential.
These materials have become instrumental in the development of 3D-printed aerospace components:
-
Titanium Alloys: Titanium is a favored material in aerospace due to its exceptional strength-to-weight ratio and corrosion resistance. 3D printing services allow for the creation of complex titanium components that are both lightweight and durable.
-
High-Performance Alloys: Nickel-based and cobalt-based superalloys are widely used in aerospace for their high-temperature strength and resistance to corrosion. 3D printing enables the precise fabrication of intricate components with these alloys, which are critical in engine parts and other high-stress applications.
-
Aluminum Alloys: Aluminum is valued for its lightweight properties and is extensively used in aerospace structures. 3D printing with aluminum alloys offers the advantage of creating components with reduced weight and enhanced mechanical properties.
-
Composite Materials: In addition to metals, composites are increasingly employed in aerospace. 3D printing allows for the incorporation of composite materials in the design of complex components, providing the desired balance of strength and weight.
Does 3D metal printing pose unique design challenges?
While the rapid rise of 3D metal printing has ushered in a new era of innovation and possibilities in the fields of aerospace and engineering, this transformative technology comes with its own set of unique design challenges.
Aerospace engineers face four key challenges in 3D metal printing:
-
Heat Management: The layer-by-layer additive process can create thermal stresses within the component. Ensuring proper heat management during the printing process is crucial to prevent distortion or cracking.
-
Residual Stress: Residual stress in 3D printed components can affect their mechanical properties. Design modifications and post-processing techniques are necessary to mitigate these stresses.
-
Support Structures: Complex geometries often require support structures during printing to prevent deformation. These support structures must be carefully designed and removed after printing.
-
Quality Assurance: 3D printing quality assurance in aerospace is of paramount importance. Ensuring that printed components meet the required standards for strength, durability, and safety is a continuous challenge.
The key to overcoming these challenges is innovation, problem-solving, and determination. With each challenge, we come one step closer to mastering 3D metal printing, revolutionizing industries, and reshaping the future of design and production.
Conclusion
The aerospace industry is at the forefront of adopting 3D metal printing for the creation of complex components. This technology has revolutionized the way aerospace engineers design and manufacture critical parts, providing opportunities for lightweight structures and intricate geometries while reducing waste and production costs and improving lead time.
With material innovations continuing to evolve and design challenges being addressed, we should expect 3D metal printing to play an increasingly pivotal role in the future of aerospace manufacturing.
The content & opinions in this article are the author’s and do not necessarily represent the views of ManufacturingTomorrow
Comments (0)
This post does not have any comments. Be the first to leave a comment below.
Featured Product
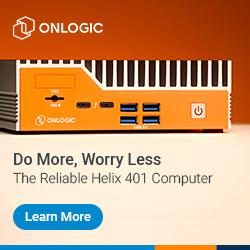