It is estimated that almost every factory loses at least five per cent of productivity, with some experiencing as much as a 20 per cent loss, due to downtime. This translates into millions of dollars in revenue loss.
Obsolescence Management for Manufacturing - Minimizing Unplanned Downtime
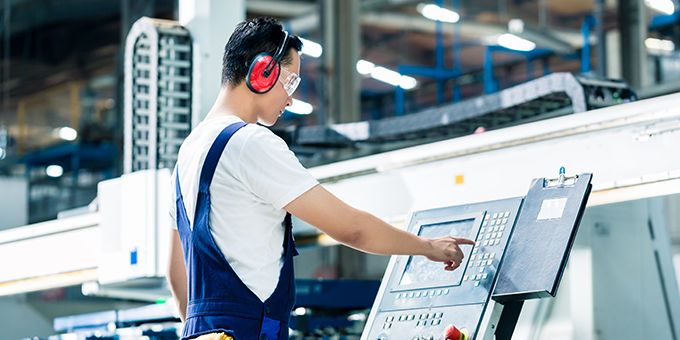
Claudia Jarrett, US country manager | EU Automation
Here, Claudia Jarrett, US country manager at automation parts supplier, EU Automation, explains how a proactive approach to obsolescence management can help manufacturers reduce the risk of unplanned downtime.
Downtime in manufacturing is defined as any period when a machine is not in production. The total amount of downtime a factory experiences includes any stops during production that cause a loss of revenue for the company.
Manufacturers understand that the cost of downtime is not just measured with numbers. Lost production and idle workers are just a small price to pay when reputation and customer relationships are also on the line. With the current state of the global market, upsets in production can lead to lost contracts because purchasing teams can find an alternative source so easily — and for almost anything.
The occurrence of breakdowns can also cause collateral damage that can, in the worst-case scenario, take down an entire production line. For example, if a furnace control mechanism breaks, not only would product be wasted, but heat exchangers could break too, releasing toxic material. Furnaces also take a long time to cool, which further delays maintenance efforts and creates additional cost when compared with predictive maintenance, coupled with an effective obsolescence management plan.
Getting knocked down
If manufacturers do not take preventative measures, these stops will occur without notice and can last any length of time, creating massive backups along the production line.
For example, machine downtime can be caused by part failures such as pumps, belts, sensors and motors that require replacement or repair. The length of downtime is determined by the availability of the materials necessary to make the required repairs, and if a maintenance technician is available to make those repairs.
Manufacturers must be able to quickly bounce back from unplanned downtime if they hope to avoid spiralling costs. The simplest way of doing this, in this instance, is by using a like-for-like replacement part, ideally an exact replacement from the same OEM.
However, if the broken component is no longer in production, it can be difficult to source. This may lead to further delays or require an entire production line redesign. Not only are redesigns costly but undertaking one as a kneejerk reaction to a breakdown could alter the quality of the end product.
While manufacturers can opt for a redesign to remove the faulty component, they should also consider finding a way to source the obsolete part. Replacing a part is faster and more cost-effective than a redesign, but if there isn’t an effective obsolescence management policy in place, the plant manager could be forced to choose the more expensive option.
Stockpiling large amounts of replacements is also not a feasible option. The cost of buying, storing and transporting the parts — and the depreciation in their value — will negatively affect profit, even if only on paper in the case of depreciation. Moreover, the parts will take up valuable space that could be reserved for finished products. A lean framework to help identify and plan for obsolescence is the answer.
Getting back up
Obsolescence management strategies begin when the plant manager audits their systems to establish the life expectancy of each element, how long it has been on the market and if anything has or is close to becoming obsolete. This step is central to the strategy because, without it, it is impossible to gain a comprehensive picture of what must be done to protect the systems.
Consolidating the data from the audit will allow for resource planning, which can include deciding on whether to employ a dedicated automation part supplier, like EU Automation, or manage the process in-house.
Once the framework is in place, it can be fleshed out by performing a risk analysis of the parts. The analysis will take into consideration rarity of the part, risk of failure and the impact that failure will have on the entire system. Regularly contacting an automation parts supplier to keep track of availability will help keep the risk analysis up to date. When a part is high risk in all three areas, it would be best practice to stock it ahead of time.
Following these steps will make sure that you get the most out of your production equipment, minimizing unplanned downtime and allowing you create a well-rounded strategy. It is advisable to also keep an obsolescence logbook, which will help keep the strategy up to date and allow the whole team to understand company policy on obsolescence management.
Let’s return to our original estimation that almost every factory loses at least five per cent of productivity due to downtime. Now let’s imagine that you are the Colonial Motor Company, the Hawke Coach Network or Nissan, Toyota or Ford New Zealand. Instead of losing a few hundred thousand dollars a year, downtime is now costing millions. Investing in obsolescence management now seems essential.
EU Automation recommends forging relationships with reliable spares suppliers. For more information on its range of automation components to support the sustainable surge, or to help you source parts, visit the website at www.euautomation.com/us.
The content & opinions in this article are the author’s and do not necessarily represent the views of ManufacturingTomorrow
Comments (0)
This post does not have any comments. Be the first to leave a comment below.
Featured Product
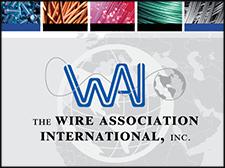