Karlsruhe University of Applied Sciences enriches Additive Design and Manufacturing Courses with MakerBot 3D printers. Students use METHOD X for a range of prototyping applications in research and development, industry thesis projects, and more.
Prestigious 140+ Year Old University Delivers Advanced Engineering and Technical Training With Method X
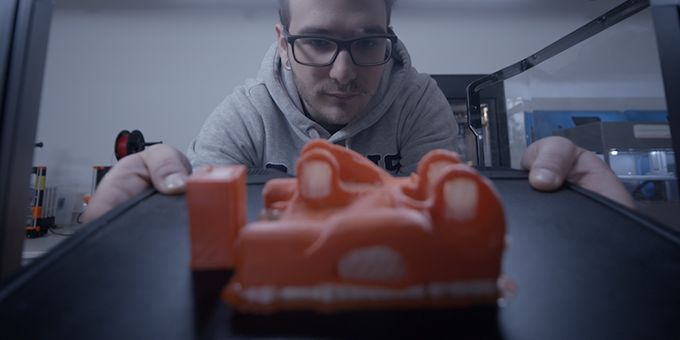
Case Study from | MakerBot
Founded in 1878 and located in Baden-Württemberg, Germany, Hochschule Karlsruhe, University of Applied Sciences (HsKA) has a long and rich history rooted in research and engineering education. Through its robust technical and academic training, the University prepares students with critical skills to excel in their careers.
HsKA is well-equipped with high-tech design, engineering, and manufacturing equipment, including 3D printing technologies. The Additive Design and Manufacturing Lab, situated in the Faculty of Economics, provides students with access to various polymer 3D printing technologies, such as FDM (fused deposition modeling), SLA (stereolithography) and DLP (digital light processing). The lab has several MakerBot 3D printers, including the Replicator 2X, Replicator Z18, and now the MakerBot METHOD X. The school also has a metal fabrication lab within its Faculty of Mechanical Engineering and Mechatronics available for students to use.

“I believe that 3D printing is a valuable problem-solving tool and key competency for the future workforce. It was important to integrate this technology into our courses to give students a chance to use equipment that is currently being used within design and manufacturing companies today,” said Prof. Dr. Florian Finsterwalder.

Prof. Dr. Finsterwalder teaches the Additive Design and Manufacturing courses, where students are taught the foundations generative design and additive manufacturing on both a theoretical and physical level. The courses teach students how to conceptualize, design, and transform ideas into tangible objects that they can physically manipulate. Students also dive into the different materials, processes, technologies, and sustainability practices across the additive manufacturing spectrum. Students learn more than just prototyping; they are taught about the industrialization of the entire additive manufacturing chain.
“Our plan is to increasingly focus on industrial parts, so advanced 3D printing capabilities are very important for us. We believe that the MakerBot METHOD X is the perfect entry-level industrial equipment that can provide industrial-quality parts,” he added. “We have been quite impressed with METHOD and what it was able to do. Dimensional accuracy, which plays a big role in 80% of our projects, is especially important for us. Depending on the materials used, distortion during 3D printing can be quite significant. METHOD’s heated chamber and rigid steel frame drastically reduces the distortion, yielding tight tolerances and a high level of accuracy.”
Additive manufacturing enriches the University’s curricula by providing students with hands-on training with innovative technology that is also used in businesses today. Open 24/7 during the semester, students utilize the lab and the machines frequently. By the time the students graduate and enter the workforce, they will be working at the height of Industry 4.0.
Preparing Students for Industry 4.0
“3D printing as part of product development can be a great benefit for businesses. It can speed up and improve the design process by letting designers test out ideas as often as they need,” said Steven Seither, graduate student and candidate for the Master of Science degree at HsKA. “When I returned to the University for my master’s degree, I quickly joined the Additive Design and Manufacturing Lab as a lab assistant so that I can further familiarize myself with the technology. I have been using 3D printing for quite some time, and I believe that I have an advantage in the job market because of the critical thinking and technical skills that I have developed.”
Prof. Dr. Finsterwalder continued, “The feedback from our students on the METHOD X has been overwhelmingly positive. Our students just want to be able to hit a button and have the printer churn out their idea in a physical form, and in this regard, METHOD has been a very useful tool. Even students who are unfamiliar with the technology can use it for their own projects.”
3D printing is increasingly gaining momentum in education, and that is no different at Karlsruhe University of Applied Sciences. For students, 3D printing is a valuable tool for them to turn their ideas into reality, while building the experience and skills they would need for their careers. To give students an opportunity to work in real-world business situations, while supporting local businesses, the University partners with startups to create capstone projects as well as help place them for work after graduation. The region of Karlsruhe has a very vibrant startup culture, dense with commercial and industrial businesses that have shaped the education and focus for many incoming and graduating students.
“I absolutely believe that 3D printing is increasing creativity and professional development. In the past, the opportunities for realizing prototypes were rather limited due to either time or cost or both. Today, 3D printing offers us an opportunity to quickly realize parts and prototypes. The iteration and the process of developing these objects no longer stay at a theoretical level. Students face challenges and difficulties directly and use 3D printing as a problem-solving technique to realize or produce parts, products, or carry out projects,” he concluded.
The content & opinions in this article are the author’s and do not necessarily represent the views of ManufacturingTomorrow
Comments (0)
This post does not have any comments. Be the first to leave a comment below.
Featured Product
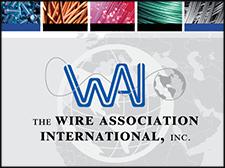