From a molding perspective, only the most experienced expert micro molding companies can successfully achieve the exacting tolerances that micro-optic components demand. Micro-optics require a unique processing knowledge — different from mechanical parts.
Manufacturing Micro-optics — a Micro Molding Perspective
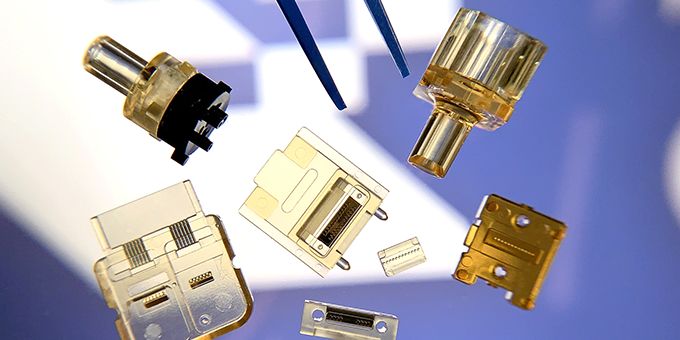
Rick Brown, Senior Sales Engineer for Optical Molding | Accumold
Micro-optics are typically tiny lenses, beam-splitters, prisms, light-pipes, and other optical components in the range of 20 microns to 1 mm in size, or larger optical components with micron features. They allow manufacturers to continue the industry-wide drive towards miniaturisation in applications where light is involved, while at the same time reducing manufacturing costs, and are used today in an array of applications such as sensors, medical diagnostics, DataCom applications, wearables which include fitness type devices and medical diagnostic devices, and emerging technologies such as augmented reality glasses and contact lenses.
From a molding perspective, only the most experienced expert micro molding companies can successfully achieve the exacting tolerances that micro-optic components demand. Micro-optics require a unique processing knowledge — different from mechanical parts — and micro molders must have experience of processing very small parts, with unique requirements when it comes to handling and packaging.
In addition, the micro molding process itself is under serious pressure with micro-optics applications, and often “off-the-shelf” molding machines will not reach the grade. With this in mind, for example, Accumold uses its own micro molding machines made in-house which stretch the envelope and attain the small scale necessary for micro-optics parts, and also achieves the absolute flatness required (the surface relief feature depth of diffractive optical elements (DOEs) being in the range of a few hundred nanometers to a few micrometers and refractive micro lens arrays less than 100 microns).
Use of injection molding for micro-optic manufacture requires the optimization of design, mastering, tooling, and production steps, meaning a close interaction between supplier and product developer is vital.
However, the skills involved in achieving success in micro-optics applications extends beyond the actual molding process itself and necessitates not just engagement with a truly vertically integrated micro molding company (bringing together tooling, micro molding, validation, and automated assembly), but also one that is on top of its game when it comes to Design for Manufacturability (DfM) and Design for Micro Molding (DfMM).
Many customers come to their chosen micro molder with a design that is far from being producible. A good micro molder must be able to guide these customers towards a design that can be produced and scaled up to production. Sometimes it’s as simple as drawing changes on a white board that can then be incorporated into designs, but sometimes there is a need for a complete re-design of parts from scratch using 3D solid modelling software.
All this implies that the healthiest and therefore most rewarding relationship between micro molder and customer is a root and branch partnership, allowing the micro molder the opportunity to impart specialist expertise and knowledge early in the design cycle, and indeed throughout all development stages. Building such relationships has been key to Accumold’s success and means that by osmosis the company tends not to have “one and done” customers with a single project and nothing behind it.
The overall micro-optic manufacturing sector is characterized by high costs and high risks, with few qualified and reliable micro molders available that can manufacture to the level of accuracy required, in the timeframe required, and at a sensible and competitive cost.
Of vital concern when choosing a qualified partner is an understanding of the necessity for qualified and expert testing and quality assurance processes that are unique to micro-optic fabrication. There are numerous challenges when attempting to manufacture micro-optic devices and components which demands that OEMs choose to partner with companies with a proven track record and years of experience manufacturing to the tightest tolerances and the most exacting standards achievable. It is extremely important to review the in-house metrology tools that are available to be able to validate and assess the unique lens profile and surface finish requirements that characterise micro-optics parts and components.
And then there is the tooling side of the equation.
Micro molders will routinely be required to assist in the design, tooling, and manufacture of micro-optic devices such as 250-micron fiber optic lenses, parallel array products, demux devices, and diffractive lenses. They may also need experience of molding attenuated resins and adding IR, anti-reflective (AR), and reflective coatings onto plastics. The demands associated with running micro-sized optical couplers, integrating lenses into housings, replicating lens profiles within a quarter wave, and lens surface finishes within 50 angstroms requires that micro molders have a dedicated tooling expert on staff to advise on and optimize DfM (and more specifically DfMM) and tooling for any OEM light transmission requirements.
But tooling challenges and validation are only two considerations, also of key importance is molding process parameter control and post-molding handling and assembly. Precise control of the shot size or volume of resin injected into the mold on each cycle is vital for the maintenance of accuracy and repeatability of micro-optics shot to shot and run to run.
Once molded however, it is important to use a fully automated and hands-free assembly process, overcoming the basic logistical issues surrounding the removal of such tiny and delicate components while also ensuring that orientation is maintained, and parts are not contaminated by touching. In micro-optics applications, complex assembly operations can often be avoided through the use of over-molding, and a micro molder with the understanding of what is possible in the molding process and has the skills necessary to overmold is often vital. The fewer assembly steps the better, but when post-production assembly is required, and if the volumes are high enough, dedicated molding and assembly work cells can be built to do the assembly all the way from molding to final packaging.
Typically, micro-optics cannot be bulk packaged, and so many methods for packaging need to be available, the most common being custom thermoform trays and tape and reel. For low volume projects it is possible to hand load the trays, but high volumes require automation for inspection and placement into packaging.
Summary
The extremely tight tolerances that are characteristic of micro-optic applications — coupled with the demands for expertise in tool construction, material selection, validation, automated assembly, and packaging — require that OEMs undertaking a micro-optic project engage with a micro molding partner in development to ensure accurate, timely, and cost-effective manufacturing solutions. There are a lot of molders out there that claim to be micro molders, but few have the depth of experience required. Customers need to understand that fact and come to a well-qualified micro molder with an open mind when it comes to DFM and DfMM of their parts.
The content & opinions in this article are the author’s and do not necessarily represent the views of ManufacturingTomorrow
Comments (0)
This post does not have any comments. Be the first to leave a comment below.
Featured Product
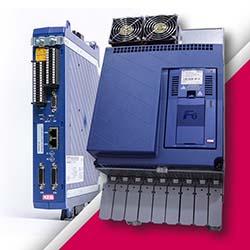