With just about any CNC control, you can be certain you’ll be able to take code from a CAD CAM system and start machining with the push of just a few buttons. But what makes one control better than another?
When to Retrofit a Machine and How to Choose the Right Control
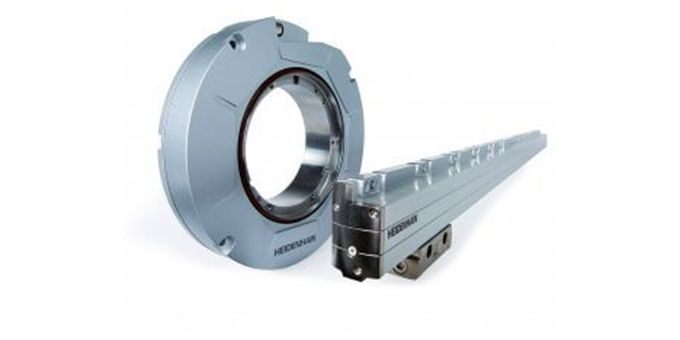
Article from | Heidenhain
Retrofitting a machine tool with a CNC control can revive an outmoded capital investment into an active revenue source. A prime example is what’s happening with the return of manufacturing to the U.S. A lot of the work being reshored includes large parts, because they are getting more and more expensive to bring from overseas. The problem is, the multimillion dollar machines, with dozens of meters of traverse, are 20 years old and replacement is both expensive and very disruptive to business.
Retrofitting has proven a smart alternative because it brings the machine back to life at a fraction of the cost of a new machine and much faster than several-month lead time. While prime candidates for retrofitting, these large machines are not the only ones suited for retrofitting.
When retrofitting machines is a good idea
- There’s a need or opportunity to add new capabilities, cut different parts and/or enter a new market.
- There’s a network of machines, but not all machines have controls that can connect.
- If a company purchases a 5-axis machine in order to be able to cut parts in fewer setups and reduce labor costs.
- In order to counter a competitor who has added a new machine. New machines and controls can outperform previous generations of machines and controls by 50 or 100 percent depending on the application.
- When machining 3D surfaces, as in big mold applications or forming dyes, and the machine cannot hold tolerances anymore.
- If you have different size cavities within the same part. In other words, a cavity on one end of the part machined on Monday isn’t the same size as the same cavity on other end of the part machined on Friday.
What makes a good CNC control
Ultimately, a quality CNC control empowers the operator to do more at the machine. It allows more flexibility to diagnose and address issues right at the CNC without reposting a program from a CAM system to machine a good part. The right control chosen with the right objectives in mind have a huge impact on productivity.
An engaging interface that’s attractive to young talent
All the industry sectors are trying to find new talent and younger generations of people to fulfill the roles of those who will go on into retirement in a few years. Engaging, modern looking, empowering controls will play a big role in both hiring and workforce development. Young workers are used to working with technology and will have more of a desire to use it in their occupation.
Flexibility and versatility
Controls also contribute significantly to the all-important flexibility. Flexibility is something that’s becoming more and more of a requirement to stay competitive. The ability to adjust on the fly and program even 3-plus-2 parts right on the CNC can be a distinct competitive advantage, as opposed to waiting to go through the whole process of CAM reprogramming for simple parts.
Computing power or speed
Especially in 5-axis applications, you are dealing with a lot of data points. Imagine machining a football, every cutting tool edge has to reach that football is an XYZ, maybe even a C position. Millions of points need to be controlled very, very accurately, making it more important that your control can handle the data fast enough; we’re talking millisecond processing times.
The control actually needs to know what’s coming next. If a control is lagging behind, you will see it on the part, a little scratch there or a little dimple there. The cutting tool will stand there turning before it moves on to the next location.
If you want to manipulate 3D models, zoom in and out of specific pockets, you need a powerful control. These also use the same responsive touchscreens of the tablets and smartphones we’ve become so comfortable with.
A fully synchronized motion system
At HEIDENHAIN, we rarely put our CNC control on the machine with motors , scales, rotary or linear encoders from anyone but HEIDENHAIN. When somebody buys a CNC control from HEIDENHAIN with the entire motion system, they’re guaranteeing that everything works in sync. That’s unique to HEIDENHAIN, because not all control suppliers also make encoders, scales and motors. Syncing all the mechanics makes motion faster, more responsive and accurate.
This allows for high performance and features like Adaptive Feed Control where spindle load, speeds and feed are calculated together; if there’s not enough material and things could be moving faster, the machine adjusts how it moves over the area without any intervention from the operator.
The content & opinions in this article are the author’s and do not necessarily represent the views of ManufacturingTomorrow
Comments (0)
This post does not have any comments. Be the first to leave a comment below.
Featured Product
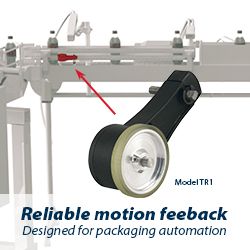