Here Jonathan Wilkins, director at EU Automation, discusses the issues and solutions surrounding retrofitting legacy equipment with smart technology.
Retrofitting Legacy Equipment
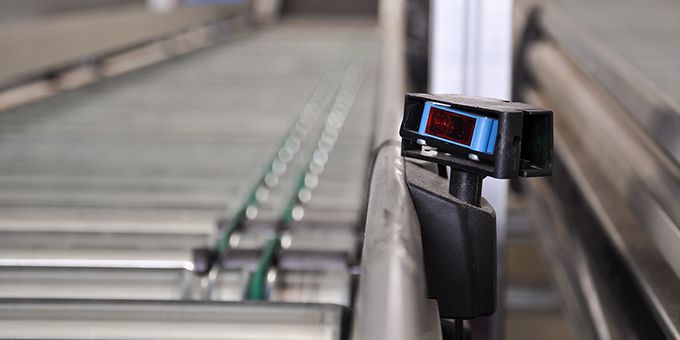
Jonathan Wilkins | EU Automation
After her mother took away her devices, a teen girl went viral after allegedly tweeting from her fridge. The reason this was so entertaining is because it’s unexpected — you don’t typically associate fridges with communication, just as you don’t with legacy equipment. Here Jonathan Wilkins, director at EU Automation, discusses the issues and solutions surrounding retrofitting legacy equipment with smart technology.
Legacy equipment was not designed to communicate, but it can be given a new lease of life by retrofitting smart technology — even if it is 20 years old. Retrofitting avoids replacing an entire system by instead adding the required capabilities to equipment that is already installed.
Issues with legacy equipment
Functional legacy equipment, such as drives, sensors and PLCs, are often the backbone of a factory. As technology progresses, these machines may need to be integrated with newer machines, which come equipped with data collection and communication capabilities. This can cause issues for manufacturers in connectivity and interoperability.
New machinery is being produced and saturating the market at an accelerated rate, despite the lifespan of older models not being complete. As technology advances, we don’t want legacy machinery to be left behind — replacing the backbone of the facility would be costly and time-consuming. However, manufacturers don’t want to be held back from collecting data on their processes and equipment that could hold valuable insights. So, asides from ripping entire systems out and replacing it all with new versions, what can we do?
Finding a solution
Design engineers should aim to implement a roadmap of the factory’s existing digital capabilities and focus on aims, targets and prioritizing actions that will effectively increase business value. Some machinery may need replacing with new technology, however, retrofitting viable legacy equipment, with smart technology, can be far more cost effective than replacing the entire production line and will can extend the lifespan of equipment.
The ultimate dream for many manufacturers is full digitization, vertically and horizontally, across the company, as well as its suppliers and distributors. Thankfully, manufacturers working towards this do not have to invest in a haul of new equipment. One step to take when upgrading systems is improving human to machine interaction, by retrofitting a human machine interface (HMI), with an easier-to-use graphical interface, such as a touch screen, or additional capabilities. For example, a HMI could be easily integrated into system by connecting a USB, RS-232, RS-485 between the HMI and PLC. If the units have wireless capabilities, it can be even easier.
Smart sensors, which can measure vibrations, temperature and pressure can be fitted onto legacy machinery, allowing data to be collected and made available across the whole factory network. This can feed into a predictive maintenance approach to glean insights on machine performance and upcoming maintenance needs. If a smart sensor detects that a piece of equipment may break down, the manufacturer can take steps to order a replacement.
While these simple steps might not meet visions of tapping into every piece of equipment from your smart fridge, it does provide a good starting point to access, monitor and control information remotely in factories.
The content & opinions in this article are the author’s and do not necessarily represent the views of ManufacturingTomorrow
Comments (0)
This post does not have any comments. Be the first to leave a comment below.
Featured Product
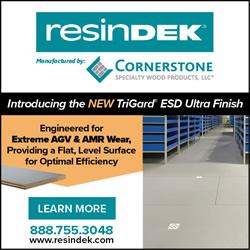