Continuous improvement tools can enhance and streamline your lean manufacturing process. Leveraging the right tool at the right time can increase your profitability, reduce process errors and improve productivity.
5 Continuous Improvement Tools to Help Streamline Manufacturing Processes
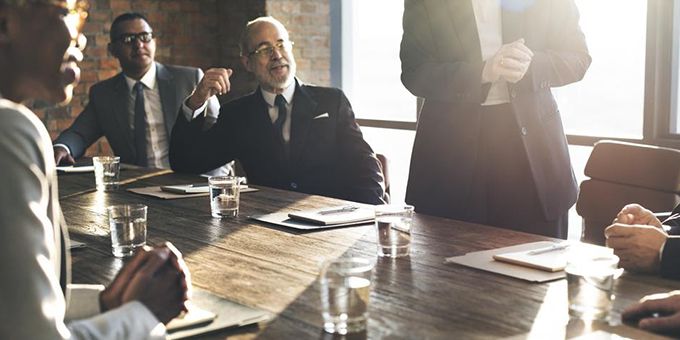
Cheryl Stevens | AmScope
Continuous improvement tools can enhance and streamline your lean manufacturing process. Leveraging the right tool at the right time can increase your profitability, reduce process errors and improve productivity.
There are quite a few different tools, and it can be challenging to assess which one will work best for your company. We discuss five tools, and it is up to your company’s leadership to evaluate which one is best for your process.
Methodology
Over the years, businesses have implemented specific tools and systems to improve their structures and their manufacturing processes. It is helpful to have a framework and a set series of steps to implement change in company processes. Change is difficult and tumultuous, and having a system in place smooths out the process.
The first step in adopting any new system into your company’s process is to ask yourself a series of questions:
- What does your company do well?
- Where does your company struggle?
- What seems unstable in your growth towards a lean manufacturing model?
-
What seems outdated and unnecessary?
As you answer these questions, you will pinpoint areas needed for improvement. What needs to be changed will become apparent, and the continuous improvement tool you will need to implement change becomes more evident.
Below are five excellent continuous improvement tools:
1. Plan-Do-Check-Act (PDCA) Cycle
The PDCA cycle gives you a solid framework for testing out ideas and hypotheses. It is similar to the scientific method created by Francis Bacon, which advises a similar set of steps–hypothesize, experiment, evaluate. Here are the four stages of the PDCA cycle:
- Plan–Define your goal and the strategy by which you will attain them
- Do–Implement the beginning steps of your plan on a small scale to see how it takes
- Check–Evaluate how things are going so far and identify any areas for improvement
-
Act/Adjust–Based on the third step, make any needed adjustments to reach your goals
There is a variation of the PDCA cycle, which is the PDSA cycle. The “S” in this one stands for “Study,” and it involves passive observation instead of action.
2. Kanban
Kanban is a method of visualization that uses sticky notes on a whiteboard to help you see the problem, the path and your goal. This method helps solidify your company’s work process.
Using the Kanban method, you write each step of your company’s process on individual sticky notes. You then order these notes onto a whiteboard so that you can see your workflow more efficiently.
Since the sticky notes are small and adhere to the board, it is easy to move them around for different visualization of your workflow.
Unlike other continuous improvement tools, Kanban is more about evolving than revolutionizing. This method does not force the process to fit the goal, but instead looks at each element as fluid and changeable.
3. Gemba Walks
Gemba walks are one of the most powerful tools on this list. Many lean manufacturing leaders realized that the most impactful way to improve their company’s product was by interacting with those employees who are directly involved with making their product.
Gemba walks encourage the company executives, who are in charge of the significant decisions, to leave their offices and walk around the factory floor. The word “Gemba” means “the real place” in Japanese, but can more accurately be translated as “where the action happens.”
When managers and higher-ups walk and talk informally with their employees on the factory floor (as opposed to a board room), they invite insights that might not have otherwise surfaced. Factory floor employees may feel more comfortable talking to their managers when there is not so much pressure.
The genius of the Gemba is their informality and casual air. It is such an easy tool to implement and makes a drastic difference in the perspectives of both the executives and the floor workers. It also builds rapport between executives and employees, which builds trust and helps with improvement implementation later on.
4. Continuous Improvement Technology
In this digital age, there are computer-based tools that combine the best aspects of these improvement methods and make them easier to use. Technology as a whole aids companies in efficiency and productivity, and now there are specific continuous improvement tools to add to your technology retinue.
A company may utilize a microscope to ensure correct results during a failure analysis or implement software that mimics a Kanban, for example. A microscope for industrial inspection is an invaluable tool in your quest for improvement.
Software quickly observes and reports to a range of recipients without the footwork needed in previous decades. You can also chart your growth and overlay different projections on top of this growth to fully understand your company’s trajectory.
5. The 5 Whys
This tool is one of the best for root cause analysis, which identifies the underlying causes of an outcome. A team using the Five Whys can move past blame or other reactive behaviors and root out the cause of the problem.
Here is how it works:
- State your problem and then ask Why?
- Once this why is answered, ask Why? again.
-
Repeat five times, which is usually the number of whys needed to get to the root of the issue.
With one answer to each question, many other complications and reasons tend to open up below that answer. It encourages a business to continually assess the underlying causes of a problem, and to help employees see that there may be more than one reason that needs to be addressed.
Final Thoughts
One of the most substantial benefits of these tools for continual improvement is their simplicity. Continuous improvement tools take a straightforward premise and stick with it. For Gemba walks, it’s the simple idea of informally interacting with other employees. With the Five Whys, it’s as simple as asking a question.
Technology can aid your company in continuous improvement. You may opt for a microscope for industrial inspection or software that mimics Kanban. Whichever tool you choose, it’s crucial to keep your goal clearly in view. Any step towards continuous improvement is a step closer to a better outcome for your company.
(1).jpg)
Cheryl Stevens is the Community Relations Specialist for AmScope. She oversees all company-wide outreach programs and initiatives. Her passion in life is helping others see the value in and implement STEM programs for children at an early age.
The content & opinions in this article are the author’s and do not necessarily represent the views of ManufacturingTomorrow
Comments (0)
This post does not have any comments. Be the first to leave a comment below.
Featured Product
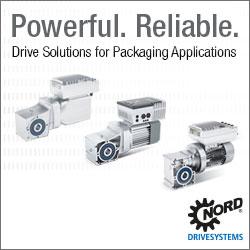