In today’s fast-paced world there is an immense pressure on manufacturers to create a better, faster, stronger, cheaper product, and only those who are willing to adapt and innovate will survive. Manufacturers who’ve been dragging their heels (or worse, kicking & screaming) are now getting on-board with replacing metal parts with plastic ones.
Manufacturers Replace Metal with Plastic to Reap Benefits of Plastic Resins While Maintaining Integrity of Metals
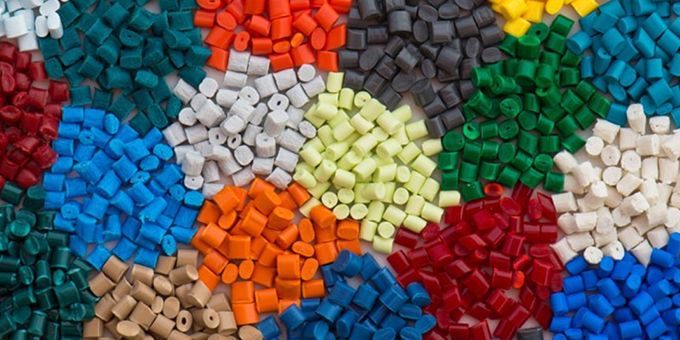
Article from | PMC Plastics
In today’s fast-paced world there is an immense pressure on manufacturers to create a better, faster, stronger, cheaper product, and only those who are willing to adapt and innovate will survive.
Manufacturers who’ve been dragging their heels (or worse, kicking & screaming) are now getting on-board with replacing metal parts with plastic ones.
Industries being most impacted by the switch include:
- Automotive/Transportation
- Aerospace/Aviation
- Military/Defense
- Consumer Appliances/Goods
For many decades these industry manufacturers have relied on metal– not because it’s necessarily better, but because it’s just the way it’s always been.
But, with modern advances in engineered resins and plastic molding capabilities, manufacturers are no longer bound by the heavy, expensive and restrictive metal parts of yesterday.
The forward-thinking manufacturers who have/are switching from metal parts to plastic ones are doing so for a lot of reasons, including:
Plastic vs Metal:
- Plastics weigh and cost significantly less than metal. In fact, plastic can be 6x lighter than Steel and half the weight of Aluminum, and can offer a cost savings of 35% – 50% over metal.
- Plastic molding is less time consuming than metal fabrication because using plastic vs metal streamlines and reduces the amount of secondary operations needed.
- Plastic doesn’t corrode, which means it can actually be a better solution than metal, particularly for those industries mentioned above. Now plastic parts can eliminate the cost and downtime it requires to repair or replace corroded metal parts.
- With plastic, complex geometries, surface texture and branding/labeling can all be directly incorporated into the part’s tooling, which means plastic parts can be produced faster and at a more cost-effective scale than metal parts.
- Plastic parts can go to market faster than metal ones because of the design flexibility, reduced secondary operations, quick molding cycles, and fast production times it has over metal.
Some of the most common plastic engineered resins being used to replace metals include:
- ABS
- Acetal Copolymer (POM)
- Acrylic (PMMA)
- LDPE
- PAI
- PEEK
- PET
- PUR
- PPS
While not all metal parts can be replaced with plastic parts, there is a substantial opportunity for many manufacturers to take advantage of replacing metal parts with plastic ones when and where it makes sense.
In fact, this is more true now than ever before with advances in engineered resins making it possible for plastic to perform as well as (or even outperform!) metal in aspects like strength-to-weight and strength-to-stiffness ratios.
There is a strong future ahead for plastics and manufacturers who seize these opportunities as they become available will inevitably beat out their competitors.
If you like this article you may like "Quick Guide to Metal Additive Manufacturing for Industrial Components"
The content & opinions in this article are the author’s and do not necessarily represent the views of ManufacturingTomorrow
Comments (0)
This post does not have any comments. Be the first to leave a comment below.
Featured Product
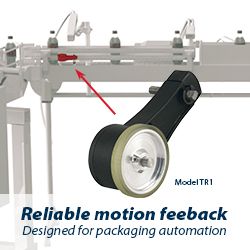