Specifying the right industrial drives is crucial to machine and overall process performance, but with industrial automation shaping the landscape for drive selection, it is vital to keep abreast of defining specification criteria.
Four Key Criteria for Industrial Drive Specification
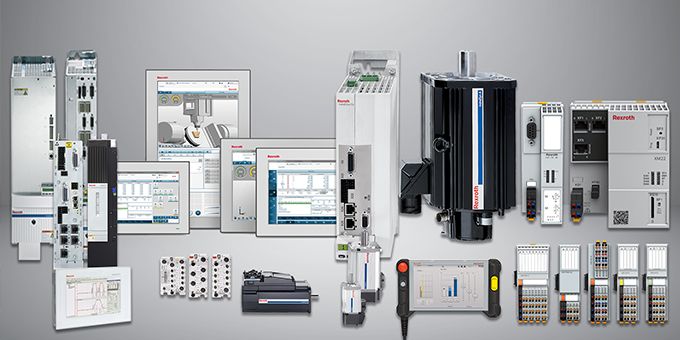
Paul Streatfield | Bosch Rexroth
It can be challenging to continually update your specification choices in line with the rapidly evolving landscape of Industry 4.0 but in doing so, machinery manufacturers can offer their customers a wealth of financial benefits as well as better use of factory space, optimised machinery performance and improved safety standards.
The key to selecting an industrial drive which is compatible with autonomy is to understand how that drive has been designed and constructed to operate in conjunction with other machines and control systems. In doing so, specifiers can better establish whether the drive will not only deliver tangible results, but also whether the investment will stand the test of time against the ongoing evolution of connectivity in the industrial sector.
Adaptable production space with cabinet-free drive technology
Since intelligent servo drives have become an indispensable part of modern machines, end users have enjoyed efficient format changeovers and motion profile adaptations at the push of a button. This performance-enhancing technology comes at a cost though, and with more servo drives comes larger, space-hungry, control cabinets.
These ‘unproductive’ cabinets essentially fill production space which would be better used for expanding a production facility through modulization. Historically the motor and control unit have been separated from each other with a power and encoder cable running from each motor into the control cabinet. This has long been the only way to utilise servo technology, until 2014 saw the introduction of cabinet-free drive technology which retains all the advantages of servo drives, but which delivers up to 90 per cent lower cabling costs and a significant gain in space by eliminating control cabinets entirely.
Designed in accordance with IP65, all network access components previously located in the control cabinet are installed directly into the machine. The mains module is a single unit and connects the entire system to the mains, containing the mains filter, the mains choke and the mains contactor. The regenerative supply module with control electronics, braking resistor and braking transistor completely replaces the supply and control electronics in the control cabinet, allowing the traditional cabinet structure to be completely removed from the system design.
Compared to traditional automation, cabinet free solutions use a fraction of hybrid cabling with the same motor spacing. This not only cuts material costs and installation times, it also reduces the probability of faults in the cabling and delivers additional monetary savings through the direct connection of sensors, I/Os and field bus components to the decentralized drives.
Integral safety features for faster engineering
Drive-integrated safety functions offer an economical method of ensuring maximum protection for people and machines whilst increasing productivity ergonomics and efficiency in engineering.
It is no secret that uncontrolled movements pose significant hazards and the more time operators have to spend inside a machine, the longer manufacturers are spending ensuring compliance with the highly stringent safety regulations outlined in the Machinery Directive 2006/42/EG or the relevant regional standards.
Intelligent, drive-integrated safety functions make it easier and more efficient to perform maintenance work in accordance with legal requirements, offering a wealth of competitive advantages when it comes to reducing system downtime and labour costs.
Building on the in-demand integrated safety functions such as ‘safe stop 1’, ‘safe limited speed’ and ‘safe direction of rotation’, leading innovators of drive-integrated safety features are already bringing to market a wider range of logic functions designed to deliver maximum machine safety even satisfying the highest safety level Category 4, Performance Level e and SIL3, in some instances.
Some of these more sophisticated functions include safe door locking and safe braking and holding systems capable of monitoring and controlling two independent brakes via redundant channels in the drive, ensuring safety in the event that operatives need to spend time beneath gravity-loaded axes.
Operational flexibility with open core engineering
Open core engineering puts entirely new application possibilities within reach for the very first time, replacing traditional HMI devices with smart alternatives during the commissioning, operation and diagnostic phases.
The ultimate in operational convenience, open core engineering unlocks the cutting edge of machine performance by expanding access to the control core and inviting the use of mobile and digital technologies into the industrial environment.
Applications made possible with open core engineering include commissioning machinery with scannable QR codes and the visualisation of processes within the machine, plus diagnostic tools which allow obtained data to be transmitted immediately for storage and evaluation. With new and extensive applications available using commonly used high level languages across all standard operating systems, developing bespoke solutions to a range of complex machining requirements is far more possible than ever before, making open core engineering a key specification criteria for drives moving forwards.
Eliminating higher-level controllers by combining motion and PLC functionality
Some class-leading drive solutions, such as Rexroth’s IndraMotion MLD units, combine motion and common PLC functionality to create a modern, open automation platform for modular machine concepts.
By decentralizing the control architecture in a compact motion control system - with both motion and logic control handled directly in the drive - it is possible to completely eliminate the need for higher-level controllers. As well as offering financial benefits due to less hardware and cabling, this type of drive architecture also enables easier engineering, faster startup, faster diagnostics and the added benefit of only having to back up one data source.
Scalable for a variety of process and manufacturing facilities, with ready-to-use function libraries to simplify use, this style of drive-based solution is available as a single axis control for basic applications as well as a multi-axis control for applications with a maximum of ten axes.
Modules based on PLCopen also provide access to standardized motion control functions whilst open technology and communication interfaces simplify the integration of MLD with a variety of automation concepts.
There is a wealth of further information online to further support specifiers in the drives selection process, ensuring that safety, operational and monetary efficiencies are paramount. For more information, visit https://www.boschrexroth.com/en/gb/trends-and-topics/drive-technology/drive-technology
The content & opinions in this article are the author’s and do not necessarily represent the views of ManufacturingTomorrow
Comments (0)
This post does not have any comments. Be the first to leave a comment below.
Featured Product
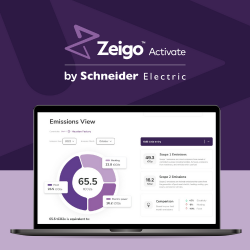