Imagine being able to produce short-runs of end use parts to test a concept or for direct use in just days. How would it feel to be able to bring a product to market faster than the competition?
Case Study: Buying Time with 3D Printed Tooling
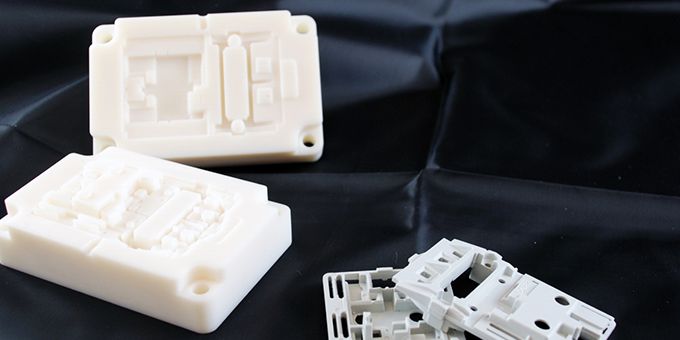
Contributed by | DSM
Wehl&Partner has been able to help customers realize just that using additive manufacturing and Somos® PerFORM. What would typically take them weeks to produce with a traditional machined metal tool has been achieved in one third the time or even less.
Wehl&Partner has used traditional methods for their injection molding projects for many years and still offer traditional aluminum tools when hundreds or a few thousand parts need to be produced. They have discovered great benefits by expanding their product offering to include tools produced with additive manufacturing, specifically made by SL (stereolithography). They have experimented with different materials and multiple technologies and have found tools made with SL and Somos® PerFORM offer the best results.
Tools made with Somos® PerFORM have high strength and allow them to heat the inserts on the tool to produce real parts in various materials and real injection conditions. This was not achievable with other 3D Printing materials such as DigitalABS, as the inserts could not be heated and only allowed for the injection in a cold mold which was unrealistic. In addition, the strength and accuracy was also compromised. Tools made with Somos® PerFORM retain their high strength properties and accuracy allowing for the production of high detail parts with fine features.
“We tried creating the tool with digital printing (PolyJet®) and stereolithography and the only technology that worked for the tooling application was SL with Somos® PerFORM. Somos® PerFORM is the only additive manufacturing polymer material where you can inject with real conditions with mold temperatures up to 120 degrees Celsius,” said Javier Garcia, CEO for Wehl&Partner Iberica.
It is a process of knowing where you can go with materials, process and design. The life of the mold itself is based on the materials and properties that are being injected into the mold. If you are injecting polypropylene, the tool will stay intact for hundreds of parts as the material is soft. If you are using a glass fiber filled material, the life of the tool will be much shorter. “If the mold is designed properly, you can produce up to 40 to 50 parts using a 30% glass fiber filled material without problems,” said Mr. Garcia, CEO for Wehl & Partner Iberica.
Wehl&Partner is one of the first to make this type of tool with Somos® PerFORM and are pleased to provide real injection parts for testing in a few days which has been ~70% faster as as compared to conventional methods. They have already made 30 different molds for several customers in the ten months since adding Somos® PerFORM to their portfolio.
If parts are simple, then you can mill a mold using traditional methods. If the mold is more complex or if quick turn-around time is needed, the additive manufacturing route is the way to go. “Our customers are delighted because you can send parts out in a few days. The process speeds up the process to 1-2 weeks versus 5-7 weeks,” said Javier Garcia. “This product and process combination buys you time. You are not buying parts, you are buying time.”
When time is of the essence, Somos® PerFORM can be used to create a high quality tool for end-use parts. It is being used by customers to make parts to test under real conditions and gain approval of new designs which speeds up the product development cycle and ultimately shortens the time to bring new products to market.
Mold for white goods component in 20% Glass Filled Polycarbonate shot at 150 degrees Celsius. This mold produced 40 parts and was fully intact after the parts were produced.
Mold for electrical switch gear in Polyamide 6 shot at 270 degrees Celsius. This mold produced 47 pieces and was fully intact after the parts were produced with only a few broken edges on the mold.
The content & opinions in this article are the author’s and do not necessarily represent the views of ManufacturingTomorrow
Comments (0)
This post does not have any comments. Be the first to leave a comment below.
Featured Product
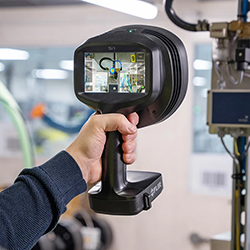