Despite its effectiveness, plasma treatments for surface modification and chemical deposition remain less than fully understood. So, too, are the tool selection choices. For this, vendors work with customers to select equipment and help justify the ROI
Making the Case for the ROI of Plasma Treatment Equipment
Michael Barden | PVA TePla America
Plasma treatments are a powerful technique for solving challenging surface issues whether through precision cleaning or by increasing surface wettability to promote adhesion. Plasma can also be used to deposit a wide range of chemistries onto surfaces.
So, when surface challenges arise and engineers and production personnel are tasked with evaluating plasma as a possible solution, it often involves a quick immersion into the physics and chemistry behind the technology.
But it also extends to how plasma is applied to each part, the type and size of chamber, tooling options, and facility requirements. Because any investment in technology must be justified based on ROI, factors such as budget, throughput and maintenance costs, must be considered prior to equipment purchase.
Therefore, whether looking to purchase equipment for full-scale manufacturing or for R & D, here are some of the key factors that should be considered when approaching an equipment vendor.
Plasma Consideration
With the right type and configuration of equipment, the collective properties of the plasma (ions, electrons and radicals) produced in the chamber can be controlled to alter the properties of surfaces without affecting the underlying materials.
For example, surface etching can be achieved through pure chemical etching of the surfaces or through physical etching or through both chemical and physical etchings.
In chemical etching, plasma activated gas species attack the material surfaces forming volatile derivatives of the materials that leave the surfaces. In physical etching, ions in the plasma are accelerated towards the substrate surfaces. On their way to the substrate surfaces they may collide with other neutral atoms/molecules to ionize them while the original ions may become neutrals. The ionized atoms/molecules start accelerating toward the substrates and the newly created neutrals continue heading toward the substrate surfaces by maintaining their pre collision velocities. As a result large number of ions and neutral species bombard the substrate surfaces causing substrate materials to eject from the surfaces.
In fact, there are so many combinations and potential chemistries involved, that equipment vendors such as PVA TePla in Corona, California often host customers to answer questions and assist in the selection of the right tool for their applications.
Although there continues to be much to learn about the physics of plasma most customers are more focused on the results of the process and how the modified surfaces can be tested. Even more questions are targeted at the type of tool that should be purchased, the facility requirements and the overall costs.
Many customers don’t care how the plasma is generated, they care about the cost, throughput and the outcome.
Equipment Selection
Although there are atmospheric systems for inline manufacturing, the majority of plasma treatments are conducted in low pressure vacuum chambers. So, from an engineering perspective, it can be important to understand the basics of what occurs within the plasma chamber.
Most low pressure plasma systems involve a chamber, vacuum pump, power supply, electrodes, the system interface and control, electrical components, gas/monomer distribution components, and exhaust system.
In general, these components have multiple options to accommodate the various processes that will be performed in the chamber.
In other words, if the vacuum chamber will be used for chemical deposition, surface functionalization, etching or cleaning, it likely will require a slightly different gas delivery system, power generator, temperature controls or chamber pressure.
There are three primary cost drivers in any plasma system – the type and size of chamber, power generator and vacuum pump.
The vacuum chamber is a rigid enclosure from which air and other gases are removed by a vacuum pump. The size of the chamber is dictated by the largest size of substrate that will be processed in the chamber. This volume requirement directly influences the size of vacuum pump required.
Vacuum pumps come in wet and dry configurations. Wet pumps use low vapor pressure oil to seal in gas to create vacuum and also lubricate its components. Dry pumps do not use any oil to seal in gas, but they may or may not use oil to lubricate the components.
The size and speed of the Pump have a direct impact on processing speed as well as actual process results that can be achieved. In addition a whole variety of factors including size of the chamber, the distance the pump is from the chamber, the length and diameter of the hose connecting the pump and the chamber, the base processing pressure required, time required to reach the base pressure, process pressure and gas load during processing.
As for the power generator, the type and size of substrate is a determining factor. If it is a conducting substrate, a dc or rf or mw power supply can be used. Non-conducting materials require an rf or mw power supply.
There can be other important considerations as well.
The temperature requirements for the processes conducted in the chamber will determine the required maximum substrate temperature for the system. Understanding the thermal budget of the substrates may require adding a temperature controller/chiller to the system.
Another key factor is whether the tool will be used for production or R&D. If for production, will it be a fully automated or a semi-automated? For R&D, will it be a semi-automated or a manual?
Facility Considerations
For production engineers, the facility considerations such as the footprint of the system, types of connections required and accessibility for maintenance are equally important.
So, too, are the ongoing consumable costs for electricity, gas, compressed air, reagents and chemicals involved. The production volumes factor heavily in this consideration as the cost-per-piece for 100,000 parts is very different than production of 8 million parts.
The duty cycle of the equipment can determine whether the most cost-effective vacuum pump option is wet or dry, for example.
Estimating the number of hours each day the tool will be utilized is also important to calculate cost of ownership (COO).
Budget Considerations
Most potential customers arrive with a pre-determined budget and delivery timeline. For this reason, companies like PVA TePla prefer to understand the parameters up front so they can tailor a solution that meets the requirements and throughput of the applications.
If we understand the budget constraints going in, then we can configure the tool based on customer prioritized process requirements. This may involve configuring the system to meet some of the process requirements while keeping options open for future upgrades to meet the other requirements when more money becomes available.
Still delivering a quote is only part of the battle. It is incumbent on companies like PVA TePla to assist customers in calculating COO to justifying the purchases to company execs.
Generally we are helping the engineers, or the process engineers, develop the case for their ROI.
For more information, contact PVA TePla America at 951-371-2500 or 800-527-5667, rayc@pvateplaamerica.com or visit www.pvateplaamerica.com.
About Michael Barden
As Head of Research & Development and Lead Scientist for PVA TePla America, Barden designs and develops custom surface coatings for the medical device and electronics industry. He specializes in nanoscale plasma enhanced chemical vapor deposition (PECVD), silane chemistries and self-assembled monolayers (SAMs). Barden manages both internal and collaborative R&D as well as contract processing.
The content & opinions in this article are the author’s and do not necessarily represent the views of ManufacturingTomorrow
Comments (0)
This post does not have any comments. Be the first to leave a comment below.
Featured Product
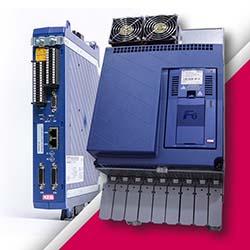