Researchers in Oregon State Universitys College of Engineering have taken a key step toward the rapid manufacture of flexible computer screens and other stretchable electronic devices, including soft robots.
Steve Lundeberg and Doğan Yirmibeşoğlu | Oregon State University
Researchers in Oregon State University’s College of Engineering have taken a key step toward the rapid manufacture of flexible computer screens and other stretchable electronic devices, including soft robots.
The advance by a team within the college’s Collaborative Robotics and Intelligent Systems Institute paves the way toward the 3D printing of tall, complicated structures with a highly conductive gallium alloy.
Researchers put nickel nanoparticles into the liquid metal, galinstan, to thicken it into a paste with a consistency suitable for additive manufacturing.
“The runny alloy was impossible to layer into tall structures,” said Yiğit Mengüç, assistant professor of mechanical engineering and co-corresponding author on the study. “With the paste-like texture, it can be layered while maintaining its capacity to flow, and to stretch inside of rubber tubes. We demonstrated the potential of our discovery by 3D printing a very stretchy two-layered circuit whose layers weave in and out of each other without touching.”
Findings were recently published in Advanced Materials Technologies.
Gallium alloys are already being used as the conductive material in flexible electronics; the alloys have low toxicity and good conductivity, plus they’re inexpensive and “self-healing” – able to attach back together at break points.
But prior to the modification developed at OSU, which used sonication – the energy of sound – to mix the nickel particles and the oxidized gallium into the liquid metal, the alloys’ printability was restricted to 2-dimensional.
For this study, researchers printed structures up to 10 millimeters high and 20 millimeters wide.
“Liquid metal printing is integral to the flexible electronics field,” said co-author Doğan Yirmibeşoğlu, a robotics Ph.D. student at OSU. “Additive manufacturing enables fast fabrication of intricate designs and circuitry.”
The field features a range of products including electrically conductive textiles; bendable displays; sensors for torque, pressure and other types of strain; wearable sensor suits, such as those used in the development of video games; antennae; and biomedical sensors.
“The future is very bright,” Yirmibeşoğlu said. “It’s easy to imagine making soft robots that are ready for operation, that will just walk out of the printer.”
The gallium alloy paste demonstrates several features new to the field of flexible electronics, added co-corresponding author Uranbileg Daalkhaijav, Ph.D. candidate in chemical engineering.
“It can be made easily and quickly,” Daalkhaijav said. “The structural change is permanent, the electrical properties of the paste are comparable to pure liquid metal, and the paste retains self-healing characteristics.”
Future work will explore the exact structure of the paste, how the nickel particles are stabilized, and how the structure changes as the paste ages.
The Office of Naval Research Young Investigator Program supported this research.
About the Collaborative Robotics and Intelligent Systems Institute (CoRIS)
The OSU College of Engineering established CoRIS in 2017 to advance the theory and design of robotics and artificial intelligence. The institute is committed to exploring the impact of robotics and AI on individuals and society through its three principal impact areas: academics, research, and deployed systems and policy. It is made up of 25 core faculty researchers and 180 graduate students, and another 40 collaborators across the university who apply robotics and AI in their work.
The content & opinions in this article are the author’s and do not necessarily represent the views of ManufacturingTomorrow
Comments (0)
This post does not have any comments. Be the first to leave a comment below.
Featured Product
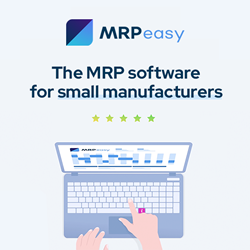