Todays HMIs (Human Machine Interfaces) go beyond pushbuttons to incorporate high resolution, multi-touch and haptic technologies.
Expanding the Definition of HMI
Allen Tubbs | Bosch Rexroth
Today’s HMIs aren’t just responsive. They’re also intelligent.
Modern Human Machine Interfaces (HMIs) have evolved to become much more than a touchscreen on the side of a machine. Simply defined as software that is capable of interacting with a machine on behalf of a human, today’s HMIs go beyond pushbuttons to incorporate high resolution, multi-touch and haptic technologies that have been developed for smartphones, in addition to incorporating entertainment technologies such as augmented and virtual reality.
These new HMI technologies also open up a host of other applications that go beyond the standard machine control. What was once just a tool for operators to input commands to a machine, now empowers operators to see more, know more and do more.
Expanding the definition of HMI
As both a lead user and lead provider of IIoT technologies, Bosch Rexroth has been taking the idea of an HMI further and redefining it for use in its own factories, as well as for those of its customers. New capabilities include not just the fast and flexible integration you expect from a contemporary machine interface, but also decentralized control and virtual reality visualization that redefine radically the way humans and machines work together.
Consider, for example, employee work instructions. In the past, these may have been printed sheets assembled in a binder, or possibly electronic versions of printed documents presented on a digital display. Now, by streaming data to and from production cells in an assembly line and integrating HMI communication capabilities into employee workstations at its plants in Homburg and Lohr in Germany, and in Bethlehem, PA in the U.S., Rexroth has added flexibility and increased productivity in its own production systems by providing employees with instant access to the information they need to get the job done right. Further, when connected to production planning systems, these new style HMIs help operators flex quickly from one product variant to another, by automatically switching instructions as production needs change, thereby enabling production lines to produce customized products with higher efficiency.
As the benefits of connected automation gain traction, more and more manufacturing facilities are tapping into stored data and production procedures to take advantage of those benefits and to become flexible and more efficient. The end result: the ability to manufacture a wider variety of products on a single system than what would normally be possible with a simple operator interface – potentially even thousands of variants.
ActiveAssist
Naturally, having your workforce keep up with constantly changing product assembly requirements in a “batch of one” environment is critical for successful implementation of such a concept. To guide workers through process steps for whichever product is currently required from their workcell, Rexroth’s ActiveAssist smart workstation technology transforms an entire workstation into an HMI – by projecting work instructions and feedback directly onto the operator’s workspace. Its technology is compatible with the ActiveCockpit communication platform (see below) and can allow information to be sent directly to the individual employee’s station. This gives the operator the ability to produce an unlimited number of variants of a product since instructions are provided to the operator digitally. Each ActiveAssist system is individually tailored to the designated employee’s needs, and the intuitive operating interface can be adapted towards the language and expertise of the employee. The system assures quality control as well as tracks operator motions and actions, using auditory and visual cues to guide the employee through the proper steps. In fact, operator motions are digitally verified by both sensor data and a vision system, which monitors the operator movement, indicates errors and can even intervene to correct the employee to prevent faulty products from leaving the facility. As a result, assembly time is reduced since the assembler does not have to continuously glance at a traditional HMI screen for instructions. In this way, ActiveAssist can reduce assembly error while enhancing the operators’ safety, as well as increase productivity while reducing costs.
Augmented Reality
Augmented reality is more than just something interesting to do with your smartphone. Already deployed in automobile manufacturing, augmented reality is becoming more popular in machinery used in manufacturing and heavy industry, as well. By allowing additional images and information to be added to a live camera feed, augmented reality users can visualize complex service and repair scenarios, complete with virtual tools and components. The Hägglunds Insight Live system works in just this way to connect users of Rexroth’s large hydraulic drives anywhere in the world to the Hägglunds service department. The user’s own maintenance team troubleshoots, adjusts settings or performs emergency tasks with guidance from Hägglunds specialists. Using a simple app on a smartphone, tablet or laptop – or a pair of video goggles for a hands-free experience – the on-site engineer works directly with one of Rexroth’s in-house Hägglunds service experts.
Via the device’s camera, the Rexroth expert sees exactly what the local engineer sees and can interact visually through the app, appearing on the engineer’s screen as part of the image. Our expert, who may be hundreds or thousands of miles away, can not only give audio instructions, but can also point out the actions that need to be taken on the customer’s equipment.
The ability to visualize various scenarios reduces downtime, assembly and repair time. Users can even visualize hidden components and assemblies, preventing unnecessary disassembly. Augmented reality can also reduce training time and costs due to the quicker retention of processes and components associated with utilizing augmented reality capabilities.
ActiveCockpit
New, interactive plant-floor visualization systems are an important step forward in tying the diverse elements in a connected factory together. Rexroth’s ActiveCockpit, for example, moves beyond the individual workstation and makes production data available on the plant floor. But it goes far beyond the simple visualization of production data. Rexroth’s ActiveCockpit, simply put, is an interactive communication platform built for the manufacturing industry. It incorporates HMI concepts with the technological capabilities of smart phones and interactive TVs to bring different parts of the manufacturing environment together into a single, cohesive visualization system. By providing easy access to the real-time happenings of the entire facility, ActiveCockpit encourages the exchange of information between the employees, machines and the shop floor. Now the HMI function isn’t limited to a machine but is connected to business, logistics, planning and maintenance systems. ActiveCockpit provides real-time interaction to everyone in the enterprise, incorporating machine floor data directly to and from the other parts of the factory. When combined with other Bosch Rexroth Industry 4.0 products, such as ActiveAssist, ActiveCockpit can transform a facility into a connected network of communication between humans and machines alike.
A new level of customization and connectivity
Of course, the “traditional” machine-based HMI is changing, too, thanks to the rapid advances in connectivity. With web-based HMIs and fast, reliable data exchange between the user application and platform independent process data gateways like WebConnector and subordinate devices via the Open Core Interface, it’s now possible to create customer-specific visualizations and to make them operable on any variety of devices or screens. Machine manufacturers can now go far beyond the capabilities of proprietary systems and generate dialogs for use cases such as set-up, diagnosis, maintenance, shop floor data collection and self-monitoring. By tailoring the interface and capabilities to the needs of their specific customers, machine builders can save their customers time in set-up, training and implementation. This brings a whole new level of value to machinecontrolled HMI functions.
New machine control technology, such as Rexroth’s Open Core Interface, allows machine builders to tailor machine interfaces and capabilities to the needs of their specific customers.
The content & opinions in this article are the author’s and do not necessarily represent the views of ManufacturingTomorrow
Comments (0)
This post does not have any comments. Be the first to leave a comment below.
Featured Product
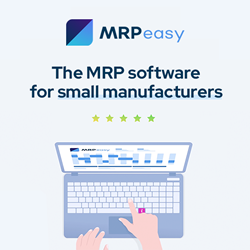