Robot Monitoring and Preventive Maintenance Solution
A robots abnormal condition can be detected early via data comparison, so a high-speed equipment monitoring solution must be able to acquire analog signals at the rate of 1000 signals per second. Then the collected signals need to be delivered to the control room for monitoring management and data analysis.
Maintenance Trends in 2017
Remember that these trends are already in place, for the most part. What you'll deal with are advancements and enhancements that make the trends more apparent.
One-Stop Repair for Food & Beverage Processing Equipment
Food and beverage processors speed repairs and reduce costs by working with single source for full gamut of machine repairs, from electronic controllers to motors.
Automatic Lubrication Systems That Stand Up to Corrosive, Caustic Environments
The latest in automated lubrication systems ensure optimum equipment performance, even in harsh plant environments, and reduce unscheduled maintenance. Corrosive plant environments are among the most serious threats to many industries today, contributing to extensive production downtime and exorbitant maintenance costs.
Factory Equipment Maintenance and Industry 4.0
The automation and collection of information thats available from machine to machine communication enables manufacturers to transition from corrective to preventive maintenance and ultimately to predictive technologies which rely on more information and data collection.
Records 31 to 35 of 35
Featured Product
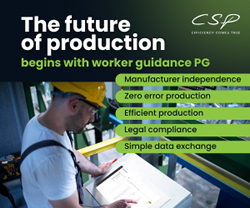
Quality assurance in the manufacturing industry
Efficiency and precision with CSP software. In the highly competitive world of manufacturing, quality assurance is a critical factor for success. CSP offers you state-of-the-art software solutions specifically designed to ensure the highest standards of quality assurance in the manufacturing industry.