Manufacturing’s 2025 Rollercoaster: How to Keep Calm and Carry On
It’s been quite the ride for manufacturing so far in 2025 (and we’re only three months in). First, the good news: Experts remain firm in their predictions that the industry will grow this year, and the initial signs are indeed positive.
Recent projections from the Institute for Supply Management indicate a 4.2% increase in overall revenues and a 5.2% rise in capital expenditures for the year, signaling a potential rebound from previous economic downturns. Sixteen out of 18 manufacturing sectors are gearing up for improvements, a sign that modernization and expansion are on everyone’s radar.
Siemens just pledged a $295 million manufacturing investment in the United States, and chipmaking giant Taiwan Semiconductor Manufacturing Co. (TSMC) plans to spend $100 billion to expand manufacturing here.
But beneath these signs of growth, very real challenges like labor shortages and supply chain vulnerabilities continue to test our sector’s resilience. These problems are further exacerbated when government policies are shifting – and decisions are changing – nearly every day.
Which begs the question: What should you focus on and where do you invest when things are so up in the air?
Manufacturing’s Top Three Pain Points – Today
Here are three critical areas that are arguably giving the industry the most pain right now and likely aren’t going away anytime soon.
Policy Impacts:
Programs like the CHIPS and Science Act, and the Infrastructure Investment and Jobs Act (IIJA), provide incentives to grow domestic manufacturing, but currently are at risk of being replaced by tariffs as a means to pump up production. (Tariffs should lead to on-shore growth in the long term but will have growing pains, as we’re already experiencing.)
How do you align your operations with economic policies when positions seem to be changing constantly? Without a steady regulatory framework, manufacturers may find themselves scrambling to adapt, risking costly disruptions. “The current chaos around tariffs and education for workforce training makes planning impossible,” said one respondent in a recent IndustryWeek survey.
Supply Chain Vulnerabilities:
The COVID-19 pandemic and ongoing geopolitical tensions have exposed just how fragile global supply chains are today. Manufacturers are increasingly shifting toward reshoring and localizing production to dodge these vulnerabilities and implementing new technologies such as digital supply networks (DSNs) to more tightly integrate supply chains.
This isn’t just about risk mitigation; it’s about building a more robust, responsive network that can weather unexpected disruptions. The complexity and interdependence of global supply chains mean that an unexpected change can cascade into a major crisis.
The need for localized, more robust production networks is clear, and the only way to build that resilience is by rethinking traditional supply chain models. But this takes time – and skilled people.
Continuing Labor Shortages:
Even in a growth economy, attracting and retaining skilled workers is still a major headache that’s likely to persist for years to come. The Manufacturing Institute, in partnership with Deloitte, predicts that 1.9 million manufacturing jobs could remain unfilled over the next decade if talent challenges are not addressed.
This is a stark wake-up call to ramp up training and automate non-value-added processes to ease the strain on your workforce.
The shortage of workers with the right skills is more than a fleeting hot topic; it’s a snowballing barrier to both short- and long-term growth. Insufficient investment in continuing education and training is leaving a growing gap.
Opportunities to Take Advantage of – Today
The road ahead may be bumpy, but it’s also lined with opportunities for those who see this uncertainty as a time to leap ahead. Here are some near-term ways manufacturers can take advantage of the challenges to improve resilience.
Measurable Tech-Driven Efficiency:
There's no longer any question that automation, AI, and smart technologies are essential to stay competitive. But who says you need to do it all at once?
Manufacturers need to start with the basics before jumping into flashy new technologies with murky ROI. One example is transitioning from paper-based manufacturing checks to a digital system that can help automate data collection and ensure process standardization – the very foundation of efficiency. Here, you can measure real before/after improvements with standardized metrics like cost of poor quality (COPQ) and overall equipment effectiveness (OEE).
Capitalizing on Policy Support:
Regardless of the fate of the CHIPS and Science Act and similar programs, there will likely be alternative policy tools aimed at strengthening domestic manufacturing and innovation. Upgrading from antiquated systems to digital solutions, which improves operational flexibility, will help ensure that you’re ready to meet (or exceed) new regulations and more quickly tap into available incentives.
More Operational Agility:
By automating manual processes and getting real-time, data-based insights, you can be more agile in the face of workforce shortages and policy shifts. This agility makes it easier to scale operations up or down based on market demands, so that your production remains robust even when external conditions fluctuate.
Building a Future-Ready Workforce:
In an industry with such a serious labor gap, integrating digital tools is like giving your employees a fast-track training program. Digital technology isn’t just about efficiency. It’s about making your work environment more collaborative and modern, which in turn can help attract the next generation of talent to your company.
Manufacturing is growing, but the challenges are real. Labor shortages, shifting policies, and supply chain risks are making the journey a serious rollercoaster ride. Rather than “wait and see,” smart manufacturers will use this time to bolster their competitive advantage by investing in digital tools, leveraging nascent government programs, and building a tech-empowered workforce.
Eric Stoop is the CEO of Ease.io, which provides cloud-based audit and inspection technology solutions for discrete and process manufacturing. He has more than 25 years of experience building high-performance teams and company culture that maximize innovation and growth.
Comments (0)
This post does not have any comments. Be the first to leave a comment below.
Featured Product
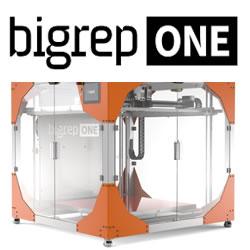