How MRP Software Transforms Manufacturing Efficiency and Reduces Waste
Manufacturing is the backbone of any industrial economy. Any industrial economy functions through manufacturing operations yet faces major problems by wasting resources and generating bottlenecks and wasting too much material. The manufacturing industry explores continual methods to optimize their processes and decrease expenses while increasing operational output. Manufacturers can reach their goals through Material Requirements Planning (MRP) software because it optimizes inventory management and production scheduling while minimizing material wastage.
This article investigates the role MRP software plays in manufacturing process optimization as well as its capability to decrease waste volumes which drives business competitiveness during fast-paced industrial markets.
Understanding MRP Software
MRP software is a digital solution designed to control production activities by evaluating operation requirements while checking inventory capacity and supply chain information. The software enables manufacturers to access necessary materials at proper times and achieve operational efficiency by reducing delays.
Traditional manufacturing methods often relied on manual planning, which led to inefficiencies, errors, and excess stock. The automation features of MRP software allow businesses to get real-time data about production timetables and inventory tracking as well as supply chain purchases. Numerous businesses have started adopting MRP Software Solutions because these solutions help optimize operations and maintain better market leadership.
The Key Ways MRP Software Enhances Manufacturing Efficiency
1. Optimized Inventory Management
Maximum efficiency results from MRP software through its implementation of optimal inventory management methods. Both storage expenses increase due to too much inventory and production disruptions happen because of under-stocking. The real-time demand and supply data that MRP software utilizes permits exact raw material quantity calculations which stops both product deficits and stock excesses.
Manufacturers can ensure uninterrupted supply chains through automated reordering as well as supplier integration capabilities in MRP software. By optimizing operational efficiency MRP software increases both total productivity rates and reduces overall expenses.
2. Improved Production Scheduling
The design of production schedules at the correct time helps companies to fulfill shipping requirements alongside enhancing customer contentment. The production schedules generated through MRP software use forecasted demand together with resource availability to handle capacity limitations effectively.
The software relies on historical production data and present work order analysis to help manufacturers optimize planning which decreases unused periods and optimizes machine utilization. The result of better workforce management enables smoother operations.
3. Enhanced Demand Forecasting
Having correct forecasts about consumer demand plays an essential role in waste reduction and operational efficiency improvement. Effective demand prediction through MRP software depends on historical data analysis supported by predictive analytics.
Manufacturers operating with knowledge of market movements and customer buying patterns can produce at required levels thus preventing overproduction of unsold stock. The data-based method helps manufacturers track actual customer needs which leads to better resource management decisions.
4. Seamless Supply Chain Coordination
Through MRP software manufacturers achieve better supply chain coordination because it allows real-time tracking across their operations with suppliers and distributors and manufacturers. Better coordination between manufacturers enables them to prevent supply chain problems along with shorter production cycles and uninterrupted manufacturing run.
An automated system for purchase orders along with real-time inventory tracking and supply communication tools provides businesses with proper delivery of raw materials at the right times. The system cuts down operational bottlenecks which leads to improved operational effectiveness.
5. Minimizing Production Downtime
Radical production stoppages result in considerable monetary losses within manufacturing environments. Through preventive maintenance tasks MRP software enables scheduled examinations for equipment alongside scheduled repairs before equipment breakdowns occur.
Manufacturers perform machine performance checks to detect foreseeable equipment breakdowns while simultaneously predicting these failures to maintain ongoing production. A proactive management method prevents time-consuming delays while maintaining continuous business operation output rates.
How MRP Software Helps Reduce Waste
1. Reduction in Material Waste
Raw material waste exists as a prevalent issue that affects manufacturing facilities. The optimization of procurement together with production processes achieved through MRP software helps decrease material waste summations. The system calculates materials with precision to prevent excess use of raw materials which reduces discarded stock amounts.
The software allows quality control operations in addition to batch tracking which detects defective materials at early stages thus decreasing waste and enhancing product quality.
2. Energy and Resource Efficiency
Production operations demand major use of resources as well as substantial energy expenditure. The MRP software system makes resource usage more efficient through its ability to improving production processes while making equipment work time more productive. Optimal scheduling of operations together with proper machine usage reduces energy expenses and generates lower environmental footprints.
When manufacturers include sustainability metrics they gain better oversight into resource use so they can develop environmentally-friendly practices which reduce unnecessary expenses.
3. Lowering Overproduction
Overproduction causes businesses to manage surplus inventory along with related storage expenses and increased possibility of product expiration. The implementation of MRP software ensures on-time production because it matches production yield with actual demand predictions.
Manufacturers who analyze market demand together with sales data and seasonal trends can produce only the necessary amounts thus reducing both waste and excess inventory costs. The lean manufacturing method uses resources in an efficient manner while minimizing production expenses.
4. Improved Quality Control
Products containing defects result in waste as well as product cost spikes. MRP software achieves quality control integration by monitoring manufacturing metrics and promptly detects errors while it maintains industry standards compliance.
The combination of batch production tracking and real-time quality assessment allows production facilities to decrease defects as well as improve customer happiness and control waste of materials and labor.
Case Studies: Real-World Impact of MRP Software
Case Study 1: Automotive Manufacturer Boosts Efficiency
A manufacturer operating in the automotive sector solved inventory inconsistencies and production problems by installing MRP software to modernize its processes. By automating inventory management and production scheduling, the company reduced material waste by 25% and improved on-time deliveries by 40%.
Case Study 2: Food Processing Company Reduces Waste
The food processing company encountered two main difficulties involving perishable inventory and frequent stock spoilage. Since implementing MRP software the business enhanced its demand projection which decreased both raw material waste by 30% and substantial savings on storage expenses.
Case Study 3: Electronics Manufacturer Optimizes Supply Chain
A manufacturer from the electronics sector solved their supply chain inefficiencies through MRP software which strengthened supplier coordination. The production process became more efficient while expenses decreased through MRP software implementation which cut lead times by 20% while also reducing production delays by 15%.
The Future of MRP Software in Manufacturing
MRP software continues to integrate modern features of artificial intelligence (AI) as well as machine learning and Internet of Things (IoT) capabilities. The implemented innovations allow businesses to conduct more accurate predictions while enabling automatic decision-making along with improved operational performance.
The artificial intelligence capability of modern MRP systems enables analysis of extensive dataset to forecast market demand alongside supply chain optimization and advanced production warning functions. IoT-enabled MRP software creates an improved system of real-time monitoring that establishes effective exchanges between machines and personnel operators.
MRP software assumes a vital position in upcoming operations because Industry 4.0 continues to revolutionize manufacturing practices. Manufacturers who transform digitally will unlock better and more flexible production processes featuring high operational efficiency.
Conclusion
Modern manufacturing experiences a radical change through MRP software because it enhances efficiency level while reducing waste and optimizing resources. Manufacturers who use automation for inventory management and improve their production scheduling and enhance their demand forecasting capability will obtain streamlined operations with cost savings benefits.
A combination of waste reduction and downtime reduction together with better quality control will advance manufacturing into both sustainability and profitability. The evolution of technology will strengthen MRP software's position as a driving force in developing the upcoming era of manufacturing efficiency.
Companies aiming to dominate a competitive marketplace will earn their best return on investment from robust MRP solutions that boost productivity and decrease production costs while establishing a sustainable operation.
Shak Ahmed is the Director of Sales at Chetu UK, with a decade of experience in technology. He graduated from Oxford and is responsible for revenue growth, relationship building, and problem-solving for clients in the transportation, supply chain, inventory management, logistics, and aviation industries. Shak's communication and collaboration skills make him a valuable asset to cross-functional teams, helping clients achieve their full potential. Shak joined Chetu in 2021, where he has built a reputation as a thought leader and industry expert within the IT community. Shak has risen through the sales department ranks, helping the company grow into an award-winning organization.
Comments (0)
This post does not have any comments. Be the first to leave a comment below.
Featured Product
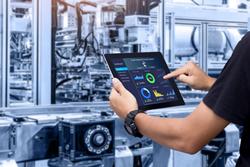