Protecting Your Bottom Line: Financial Strategies for Automation Failures
Key Takeaways:
- Automation failures — caused by hardware malfunctions, software glitches, cyberattacks, or human error — can lead to costly downtime, lost revenue, and reputational damage.
- Financial safeguards like emergency funds, insurance coverage, and predictive maintenance help manufacturers mitigate the risks of system failures.
- A well-prepared contingency plan, including rapid response teams and alternative production strategies, ensures quick recovery and minimal disruption.
- Manufacturers that proactively invest in financial preparedness can protect long-term stability and avoid severe business impacts from automation breakdowns.
Automation is the backbone of modern manufacturing, streamlining production, increasing efficiency, and reducing labor costs. But when an automated system fails, the consequences can be severe: unplanned downtime, lost revenue, and damaged reputation. The question isn’t just whether your systems are reliable but whether your business is financially prepared to handle unexpected failures.
Many manufacturers focus on optimizing efficiency and cutting costs through automation but underestimate the financial risks of system failures. A single breakdown can halt an entire production line, leaving companies scrambling to cover losses. Without a solid financial safety net, businesses may struggle to recover, especially in competitive markets where delayed orders and supply chain disruptions can drive customers elsewhere. Proactive financial planning isn’t simply a precaution — it’s a necessity for long-term stability.
The Risks of Automation Failures
Even the most advanced automation systems are not immune to failure. Whether due to mechanical breakdowns, software glitches, cyberattacks, or human error, disruptions can bring production to a standstill.
- Hardware malfunctions: Wear and tear on robotic arms, conveyor belts, and sensors can lead to breakdowns if not properly maintained.
- Software issues: Bugs, outdated firmware, and system incompatibilities can cause unpredictable failures.
- Cybersecurity threats: Manufacturing systems are increasingly connected, making them vulnerable to ransomware and other cyberattacks.
- Human error: Despite automation, workers still interact with machines, and mistakes in setup, programming, or maintenance can cause system failures.
The financial impact of these failures can be staggering. Some experts estimate that unplanned downtime can cost manufacturers up to $260,000 per hour. Beyond immediate losses, delays in production schedules can lead to missed deadlines, lost contracts, and reputational damage that affects future business.
Financial Preparedness: Building a Safety Net
While manufacturers invest heavily in automation technology, many overlook the financial safeguards needed to weather system failures. A proactive financial strategy can prevent short-term disruptions from turning into long-term business challenges. Start with these steps:
1. Establish an emergency fund.
Unexpected failures require quick financial action. Setting aside an emergency fund specifically for automation-related disruptions can help cover repair costs, temporary labor, and lost productivity. Businesses should assess historical maintenance costs and downtime expenses to determine an appropriate reserve.
2. Invest in business interruption insurance.
Traditional equipment warranties and service contracts may not cover the full impact of a breakdown. Business interruption insurance can help manufacturers recover lost income during prolonged downtime. An umbrella insurance policy can provide extra coverage beyond standard liability and property insurance, protecting businesses from high-cost damages resulting from automation failures. Policies should be tailored to cover automation-related risks, ensuring financial stability while systems are restored.
3. Implement predictive maintenance.
Predictive maintenance uses IoT sensors, AI, and ML to monitor equipment performance in real time. By identifying potential failures before they occur, manufacturers can reduce costly downtime and extend the lifespan of their automation systems. This investment not only minimizes risk, but also improves operational efficiency.
4. Develop a contingency plan.
Every manufacturer should have a well-documented response plan for automation failures. This plan should include:
- Rapid response teams: Designated personnel trained to diagnose and resolve issues quickly.
- Alternative production strategies: Backup manual processes or secondary production lines to maintain output.
- Vendor and supplier agreements: Pre-negotiated service contracts to ensure fast repairs and replacement parts.
The Cost of Inaction
Relying on automation without financial safeguards is a gamble no manufacturer can afford to take. Even a short period of downtime can ripple across the supply chain, leading to lost business opportunities and increased operational costs.
Manufacturers that take a proactive approach — establishing financial reserves, securing insurance coverage, investing in predictive maintenance, and creating contingency plans — position themselves for long-term success. Automation will always come with risks, but with the right financial preparation, those risks become manageable.
Key Considerations for Manufacturers
- Automation failures can result from hardware malfunctions, software bugs, cyberattacks, and human error.
- Unplanned downtime can be costly, impacting revenue, production schedules, and business reputation.
- Financial safeguards like emergency funds, business interruption insurance, and predictive maintenance can mitigate risks.
- A contingency plan ensures quick recovery and minimal disruption.
Manufacturers investing in automation must also invest in financial preparedness. The future of your business depends on it.
Dennis Verheijde is the National Retail Sales Manager at Affordable Contractors Insurance. Originally from Heerenveen, Friesland in the Netherlands, Dennis moved to Scottsdale, AZ during high school. He began his career as a Paramedic/Firefighter before transitioning to a Licensed Agent with ACI in its early days. After exploring growth opportunities in the retail automotive industry as a General Manager in California and Tennessee, Dennis returned to ACI. He brings a commitment to client satisfaction, process improvement, and agent development, contributing to the agency's remarkable growth over the past 12+ years. Dennis aims to further enhance the agency by upgrading its IT infrastructure to provide agents with the latest tools for maximum efficiency and optimized client experiences.
Comments (0)
This post does not have any comments. Be the first to leave a comment below.
Featured Product
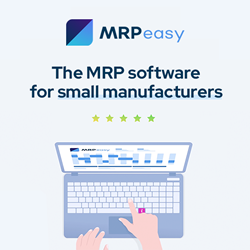