The Benefits of Predictive Maintenance Capabilities in Energy Management Systems for Industrial Facilities
The integration of predictive maintenance within energy management systems marks a significant advancement for industrial facilities. This approach, which anticipates equipment failures before they occur, is crucial for maintaining continuous operations and achieving energy efficiency. It holds particular relevance in sectors where system uptime directly correlates with productivity and profitability.
Predictive maintenance employs continuous monitoring of equipment conditions using advanced sensors and data analytics to forecast when maintenance should be performed. This method stands in contrast to preventive maintenance, which is scheduled at regular intervals, and reactive maintenance, which occurs after equipment failures. The key components of a predictive maintenance system include condition-monitoring equipment, advanced analytics software, and automated control systems that help manage the timing and execution of maintenance tasks.
Integration with existing energy management systems is greatly enhanced by employing upstream oil and gas software, which can process large volumes of operational data to optimize both operations and maintenance schedules. This not only helps in monitoring but also in automatically adjusting operations to maintain optimal efficiency and prevent downtime.
Benefits for Industrial Facilities
The implementation of predictive maintenance capabilities within energy management systems provides several tangible benefits. First, it dramatically reduces downtime and boosts productivity by allowing maintenance to be scheduled during planned downtimes, thus minimizing disruptions to production. Secondly, there are substantial cost savings, as predictive maintenance enhances energy efficiency and reduces the frequency and severity of maintenance issues, cutting down on both energy consumption and maintenance costs.
Equipment lifespan is also significantly extended as regular, data-driven maintenance prevents the excessive wear and tear associated with running machinery to the point of failure. Finally, predictive maintenance improves safety and ensures better compliance with regulatory standards by foreseeing potential equipment failures, thereby preventing accidents and hazardous conditions.
Despite its many benefits, the implementation of predictive maintenance is not without challenges. The initial investment in the necessary technology and training can be considerable. However, the ROI from reduced operational costs and extended equipment lifespans can justify this expenditure. The effective implementation of predictive maintenance also requires extensive data collection and the ability to analyze this data to derive actionable insights, necessitating advanced data analytics capabilities.
Additionally, the adoption of this technology often requires significant cultural shifts within an organization. Staff must be trained not only on how to use the new systems but also on the importance of a proactive maintenance approach. Overcoming internal resistance to such changes involves clear communication from management about the benefits and continuous engagement with all stakeholders during the implementation process.
Future Trends and Innovations
Looking forward, the potential for predictive maintenance in industrial facilities is expansive, with innovations in AI and machine learning leading the way. These technologies are set to refine the accuracy of predictive analytics and enhance the efficiency of data processing, making predictive maintenance systems even more reliable and effective.
The continued integration of Industrial Internet of Things (IIoT) devices promises a higher level of connectivity and data exchange across facilities, which will further enhance the capabilities of predictive maintenance systems. As factories continue to evolve into smarter, more interconnected environments, predictive maintenance will become a cornerstone in managing energy efficiently and optimizing operational performance.
Predictive maintenance is a key strategy for future-proofing industrial facilities. It enhances operational efficiency and positions manufacturers as leaders in the industrial sector by adopting forward-thinking technologies. As these technologies continue to advance, the importance of predictive maintenance in industrial energy management systems is set to increase, making it an indispensable tool for any modern manufacturing facility.
Vince Dawkins, President and CEO of Enertia Software, has worked with industry-leading organizations, and he has been integral in developing the Enertia application into a resource used by over 150 leaders in the upstream oil and gas industry.
Comments (0)
This post does not have any comments. Be the first to leave a comment below.
Featured Product
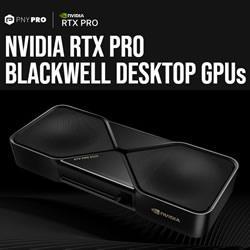