Smart Factories: A Digital Native’s Guide
Digital natives, especially those working in IT, are at the forefront of leveraging the latest technology to drive efficiency and innovation. These bright tech minds are often well-versed in cutting-edge digital solutions and know how to make the most out of the latest technology in a traditional workplace. But how do these tactics translate to alternative work settings, like factories?
The way we leverage technology in a manufacturing environment is vastly different from one where most workers are seated in front of a computer all day. The established processes and daily challenges faced by plant managers are worlds apart from the digital realm of IT.
Fortunately, the technology available today presents a massive opportunity for factories to improve operations and efficiency by more seamlessly connecting machines, processes and data analytics. However, to make “smart factories” a reality, technology professionals must understand the specific needs and constraints of the factory environment and consider solutions that serve both the digital and physical worlds.
Bridging the Gap: Connecting IT and OT
For smart factories to thrive, IT and operational technology (OT) need to integrate seamlessly. To do so, IT managers wanting to implement new digital tools in a factory must not only have a deep understanding of digital solutions, but also of what’s important to plant managers. They need to understand both realms, their differences, and commonalities. From a smart factory point of view, connecting in the physical world means connecting the data across the whole factory in real time.
It may sound straightforward in theory, but bridging this gap is far from it – and the problem isn’t technological, but rather cultural. IT managers and plant managers have different opinions and priorities on how to use data. IT people tend to have a more idealistic perception of how easily new technology can be implemented in a factory setting. Plant managers, on the other hand, tend to be more realistic and focused on what will keep things moving forward while minimizing disruption. They typically prioritize high efficiency, productivity and keeping production running under any circumstance. This causes a natural gap between the two, as priotites – at first glance and in the short-term – seem to be opposed.
For example, IT and OT managers have different measurements of success. Whereas IT focuses on metrics like service availability, mean time to resolve, support tickets, average handling times and IT security; OT focuses on metrics like overall equipment effectiveness, set-up time, jobs per hour, defects, losses, downtime and utilization metrics. In reality, both the IT and OT side want the machines to work together seamlessly and efficiently.
The first step in smart factories is getting IT and OT to see eye to eye: enabling the IT side to manage the data infrastructure and software stack on the OT side, and for the OT side to believe that this is beneficial and buy into it. It needs to be practical, working and robust.
Once these dynamics are sorted, it’s time to focus on the tech that enables smart factories.
Remotely controlling your factory
Asset management and the ability to control your factory remotely is key in a smart factory environment, especially with the increasing shortage of skilled workers. With the right tools, you can bring all the assets of OT equipment and devices into one dashboard to manage them remotely. From there, you’ll be able to see all your inventory – both IT and OT hardware assets – and manage connectivity to troubleshoot, should any technical issues arise.
Digitalizing manufacturing means support centers must be more agile and responsive in the event of a disruption, so a secure remote connectivity solution that ensures access and control of machines on the factory floor without the need for sending technicians on-site is critical.
This ensures that technical teams can gain access to designated devices in an instant.
Setting up an integration layer for the entire plant
Another way to get a step closer to smart manufacturing is by integrating all parts of the plant, using software – such as a factory data hub – that provides a common data infrastructure to bridge the technological gap.
This type of software can be fully managed and owned by the plant as the gateway collects, processes, and distributes industrial data on-prem, while enabling seamless communication between heterogeneous devices, machines, and processes in the smart factory. It decouples the sensitive production environment from critical access requests from any networks.
This method gives OT managers the security they need, while also providing the IT side the manageability to get data flowing in the right direction.
Creating a data foundation for the whole plant network
Once the plant is connected, the next step is to get a data analytics company, specifically for data in manufacturing plants. If you think about all the machines that are now connected, there are so many different data structures, different cycle times, different data items, and other changes, so having a partner that understands those dynamics is key.
Collecting, structuring, and analyzing data from manufacturing operations with innovative AI applications can provide insights into areas such as quality control, system-level plant performance, and predictive maintenance, enabling data-driven decisions that vastly improve operating efficiency, sustainably and resilience.
Making frontline workers smarter
Having dealt with the machines and the data, the one critical aspect still left are the actual people who make up the factory. That’s where an industrial augmented reality (AR) solution comes in to upskill frontline workers, connect them to the infrastructure and make them smarter with digital tools. AR glasses for frontline workers provide dynamic step-by-step instructions into an employee’s field of vision, making them smarter, more efficient and productive.
AR technology in factories eliminates the need for frontline workers to have to leaf through workplace manuals or find a supervisor each time they have a query. With AR, employees become part of the digital infrastructure with live data – such as work instructions – being fed directly to their devices. Especially with continued skills shortages across the manufacturing sector, this technology strengthens the business case for making the recruitment and onboarding process as efficient as possible.
Hyundai Motor Company is an example of a company that is utilizing these innovations in their Singapore facility. They have a holistic smart factory that interconnects humans, robots and logistics, with digital twin technology, cell-based smart manufacturing and an AI-driven warehouse for highly efficient inventory management. With this transition to a smart factory, they have improved workflow, quality control, efficiency and onboarding of workers – smartly bringing OT and IT together to streamline its operations.
Digital transformation across the manufacturing sector is an ongoing process. Combining the physical and digital worlds – especially with the addition of new robotic elements, ambient sensors, performance monitoring tools, and servers— makes for an increasingly complex tech stack to manage and maintain. And that’s not to mention the employees trying to upskill and adapt, while still being confronted with the day-to-day challenges of production.
But the adjustment will be worthwhile as transitioning to a smart factory has many benefits including improved productivity, safety, sustainability, product quality and customer service.
And once the gap between the physical and digital is bridged, smart factories will thrive and both IT and OT will reap the benefits of it.
Georg Beyschlag is the President of TeamViewer for the Americas region. He is based in Clearwater, Florida, and his responsibilities encompass all go-to-market activities in the region, including direct sales as well as developing an ecosystem of strong alliances such as channel partners, distributors, and resellers.
Comments (0)
This post does not have any comments. Be the first to leave a comment below.
Featured Product
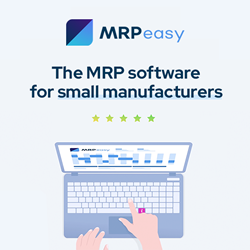