Future-Proofing Your Production Line: Exploring 7 Solutions for Modern Risk Management
Manufacturers today face a challenging road ahead. The past few years have revealed how fragile the industry is, highlighting the need for adaptation, but innovation and adjustment are difficult. Not every Industry 4.0 project has worked out, so the optimal path forward may be unclear for many businesses.
The pace of change will quicken in the future. Organizations must rethink their risk management strategies to keep up with these shifts, and in many ways, that means making smart technology decisions. Here are seven ways manufacturers can embrace a future-focused business model safely and effectively.
1. Embracing AI
Whether a specific technology is worth investment often varies between companies, but there is one notable exception — artificial intelligence (AI). AI is too powerful and already disrupting too many sectors to ignore.
Over 70% of manufacturers already use AI to some extent, so those who don’t may fall behind. However, businesses must tie it to existing goals to achieve meaningful results. This philosophy is ideal for any investment but all the more so for something as expensive and disruptive as AI. AI must always be a solution to a problem, not tech adoption for technology’s sake.
Automation is the most common use case for AI today. Automating routine software tasks is a safe route since it’s straightforward and modern solutions are more than capable of doing it. However, predictive applications hold better long-term potential. Manufacturers that can use AI to predict supply chain changes or emerging risks will derive additional value in the future.
2. Emphasizing Data Management and Governance
AI adoption must go hand in hand with increased data collection. Intelligent algorithms perform better when they have more information to analyze. Consequently, gathering data through Internet of Things (IoT) solutions and similar technologies is essential. At the same time, such practices will increase risks without proper management and governance.
Data regulations will become increasingly common over time. At least eight states passed data privacy laws in 2023 alone. Legislation aside, IoT solutions and growing cloud databases introduce additional targets for cybercriminals. While manufacturers must become data-centric to future-proof their operations, they must ensure they take better care of this information.
Given such concerns, no risk management approach is complete without data guidelines. These should include regular review of applicable regulations, specific roles and access permissions for IT employees, and steps to safeguard privacy. Data cleansing and organization practices will also help by making it usable for AI.
3. Ensuring Proactive Cybersecurity
Cybersecurity must play a central role in manufacturing risk management from here on out. The industry is already the world’s most-targeted sector, accounting for 25.7% of all attacks in 2023. Manufacturers will only become more valuable as targets as data volumes grow and AI reliance increases, necessitating proactive security.
Baseline measures like data encryption and network segmentation are essential for all organizations. However, businesses hoping to become future-proof must go further. Cybercrime is constantly in flux, so protections must be agile and adaptable.
Regular penetration testing and threat hunting provide a strong foundation. Additional defenses like AI-powered continuous monitoring and user and entity behavior analytics are also ideal, as these protect against unknown threats.
4. Building Flexible Supply Chains
As the past few years have demonstrated, manufacturers also need more reliable supply chains to survive in the future. Long-standing lean practices leave organizations vulnerable to disruption. Moving away from conventional wisdom in favor of agility and flexibility will improve companies’ risk tolerance.
Supplier diversification is a good first step. It is impossible to tell where the next supply chain disruption will stem from or how geopolitical relationships will evolve. Consequently, no single dependency is safe. Maintaining relationships with multiple 3PLs may be necessary for similar reasons.
Manufacturers should also ensure they have the resources to mitigate events they cannot prevent. Supply chain insurance can help, as it covers losses from disruption to offset financial damage in the event of property damage, equipment breakdown and more. Keeping larger safety stocks of critical materials and creating a formal emergency response plan is also crucial.
5. Maximizing Transparency
Supply chain risks will be easier to manage once these networks become more transparent. Cyber-vulnerabilities and regulatory concerns likewise become manageable with additional visibility. Consequently, future-focused manufacturers must maximize transparency across their operations.
Technologies like IoT tracking, cloud management platforms and blockchain can provide visibility throughout supply chains. Data mapping and AI monitoring tools can do the same for a company’s IT networks.
Businesses must also act on their increased transparency. That means analyzing real-time data for emerging risks and supplying government regulators with necessary information. Providing sourcing and emissions information to customers is also ideal, as voluntary disclosures can give companies a competitive advantage in today’s market.
6. Experimenting Early but Carefully
Many of these strategies emphasize the need to embrace novel technologies. However, not every invention produces a positive ROI, especially among the earliest adopters. While manufacturers must foster a spirit of innovation, they should also be careful not to invest too much too early.
Driverless vehicles are a prime example of these complex considerations. Self-driving trucks could reduce fuel consumption and mitigate labor shortages, but their current state makes them too dangerous and expensive for large-scale deployment.
One way to balance both sides of experimentation is to create a small department dedicated to testing innovative business practices. Manufacturers can deploy new technologies on a minute scale to learn how to use them effectively without excessive risks or costs. Any projects showing promise can then expand to the company’s main operations.
7. Fostering Forward-Thinking Workforce Management
As crucial as technological advancement is, organizations cannot overlook the human side to future-proofing their business. Humans and machines excel in different areas, so the workforce must adapt as Industry 4.0 takes off. Manufacturers should also consider their tech adoption’s impact on jobs and engagement.
While experts predict technology will create more jobs than it takes, the shift is not a one-to-one transition. The resulting new roles require different skills and experience than those facing dwindling demand. Consequently, companies may produce unwanted job displacement and spread fear throughout their workforce if they don’t address this issue.
Upskilling and reskilling are the answers. Forward-thinking manufacturers can avoid disruption by investing in training programs to equip workers with AI and tech-related skills. Encouraging employees to pursue such experience will prevent job losses and make implementing novel technologies in the future easier.
Modern Manufacturers Must Look to the Future
Risk management today is equal parts capitalizing on technology and taking a more critical approach to new tech. While getting ahead of technological trends is vital to surviving in future markets, so is preventing common obstacles related to these shifts.
In either case, manufacturers cannot survive in tomorrow’s markets by relying on conventional strategies. Embracing practices like these seven solutions is essential to minimize risks and maximize value in the next era of manufacturing.
Comments (0)
This post does not have any comments. Be the first to leave a comment below.
Featured Product
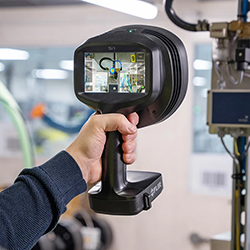