Using AI to Fill Blind Spots and Revolutionize Manufacturing Processes
One of the biggest pain points in the manufacturing industry is that most processes are not instrumented, resulting in upwards of 75% of digital blind spots. This lack of visibility on the shop floor leaves manufacturers without a complete data picture to make strategic decisions. Thanks to the AI revolution, many organizations have begun to implement automation technologies within their systems to increase operational efficiencies. However, manufacturers are only using a small portion of available data to feed their AI systems. This is problematic because AI will be given a skewed data set, which will significantly increase bias and alter outputs. Without a comprehensive data set, AI is not used to its full potential to enhance operational efficiency and predict outcomes.
To solve this issue, IIoT asset tracking and digital twins can fill manufacturing blind spots with critical data and analysis required to make better and more profitable production decisions. By doing so, businesses can ensure digital transformation success and create a complete dataset for their next generation AI initiatives. This will improve yield, profitability, and compliance while decreasing waste, maintenance and energy consumption throughout the value chain.
The First Step: Asset Management
Streamlining asset management processes is a significant challenge for manufacturers due to its crucial role in maintaining government-owned and company-owned assets as mandated by the Federal Acquisition Regulation. Asset custodians and analysts maintain records for dispersed asset items across domestic and international facilities. Companies integrate asset management databases into their Enterprise Resource Planning (ERP) systems to simplify asset management, using bar-coded asset tags for identification and location tracking. However, the manual process of updating records when items are relocated presents significant challenges, consuming time leading to errors and compliance issues.
To overcome these hurdles, organizations need innovative solutions that leverage digital tracking advancements. Automation and AI can optimize operations, ensuring accuracy and efficiency while eliminating human error and freeing up those resources for other uses. Using advanced tracking technology, active beacons can transmit continuous information, which is captured by strategically positioned gateways. The data integrates seamlessly into ERP systems, accurately determining the locations of asset items in real-time, eliminating manual tracking. Integrating an automated location-tracking system with ERP asset management databases ensures synchronization between physical movement and records. Location changes are automatically reflected and contextualized to improve reporting on decision-making. This enhanced approach to asset management brings numerous benefits, including increased operational efficiency, enhanced regulatory compliance, eliminating human error, and improving transparency and accountability through accurate and up-to-date records.
The Second Step: Digital Twin
Hundreds of millions of dollars have been spent on existing analog equipment and manual processes that have proven effective for decades. Unfortunately, these machines and processes do not provide any usable digital data for business intelligence analysis and leave executives with an incomplete picture when trying to make critical production, safety and regulatory decisions. The truth is most manufacturers don’t have the budget or a strategy on how to replace this equipment and find it cost-prohibitive to transform these processes.
This is where the concept of a digital twin comes in to provide digital data with the simple addition of sensors. These sensors are added to currently uninstrument-able machinery to provide data on nearly anything, including location, temperature, humidity, battery usage, vibration, air pressure, air quality, and more. Once this digital twin is transferred to the cloud, manufacturing leaders can associate the contextualized data with their assets, revealing previously hidden blind spots on the shop floor.
Achieving Maximum ROI
By streamlining asset management processes and creating a digital twin of processes, manufacturers have access to granular data that is contextualized to help with decision-making. Ultimately, this will allow businesses to achieve full ROI potential by improving yield, profitability, and regulatory compliance. At the same time, this will support waste reduction, less machine maintenance, and decrease energy consumption in accordance with sustainability initiatives. Manufacturing leaders should lean into the value of IIoT asset tracking and digital twins to support digital transformation and next gen AI initiatives. Those that fail to realize its full potential will get left behind in the smart manufacturing revolution.
Comments (0)
This post does not have any comments. Be the first to leave a comment below.
Featured Product
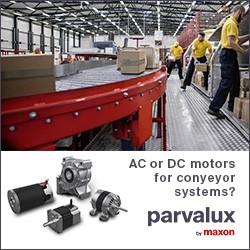