Should you build or buy your MES? - Three key reasons you might be safer with COTS
The decision to build or buy a Manufacturing Execution System can be a daunting one for many companies. Opponents in the build versus buy debate often defend fiercely entrenched positions, making it harder to understand the pros and cons. Here, Martin Hurley, business development manager at Novotek Ireland, offers three key reasons for purchasing a commercial off-the-shelf (COTS) MES.
The ultimate debate?
Manufacturing Execution Systems (MES) are software applications used in manufacturing operations to coordinate, track, control, and report on the production process. An MES can be critical to the efficient operation of a manufacturing facility, providing real-time information on production processes, inventory levels, and quality control.
An MES can be purchased off the shelf or developed in house. However, all systems, including those purchased off the shelf, will require a certain level of customisation. Building a system from scratch is very different from purchasing something that has already been built, but offers you greater room for a “perfect fit” to your operation’s particular ways of working.. However, this customisation tends to carry immediate and long-term additional costs in terms of time and money, and herein lies the debate.
A colleague of mine was recently invited onto a podcast after a fiery exchange on social media about the pros and cons of building versus buying your MES. For the interested onlookers, the debate showed that much can be gained when both sides have honest and open conversations, but it was also a time for those on either side of the fence to more carefully refine their positions. With that in mind, here are the three core reasons I believe buying is generally preferrable to building, although I understand that every case is different.
Before proceeding it worth acknowledging that like everyone in the debate, I am not neutral. Novotek is a provider of software solutions for manufacturing companies, so we supply some of the world's most popular MES options like GE Digital’s Proficy. However, having experience in this area means I have witnessed first-hand the pros and cons of different systems and the benefits that manufacturers can unlock with the right off-the-shelf product.
Time and cost
Building an MES requires a lot of resources, both in terms of time and money. In a world where minimising production downtime is imperative, time to implement is a key factor in any decision when it comes to building or buying and MES.
Purchasing an MES can lead to quick implementation times. As the software has already been developed and tested, the installation and configuration process can be streamlined. This factor is especially important for manufacturers who need to implement new systems quickly in sectors where keeping up with changing market demands is important.
In contrast, building your own system will typically take longer because the software must be developed and tested from scratch. This development process can be time-consuming and require specialised knowledge and expertise.
Furthermore, off-the-shelf products give you access to maintenance and support. When building an MES, manufacturers are responsible for maintaining and supporting the software. This can be especially challenging for small manufacturers who may not have dedicated IT resources.
As well as time, the additional cost of purchasing an MES is often lower than developing a custom solution. An off-the-shelf MES is designed to be scalable and adaptable to a wide range of manufacturing environments. As a result, they can be implemented quickly and with fewer development costs. In comparison, developing a custom MES can be expensive, especially for small and medium-sized manufacturers. This additional cost is in addition to the cost of any increased downtime that is accrued as a result of the longer time to implement.
Know what works
Off-the-shelf software is generally proven. It is already being used and relied upon by many of the biggest companies in the world. You don’t have to experiment or wait and see if the software is reliable, as many of the world’s largest brands have already done this. If it didn’t work, they wouldn’t keep using it.
There are also case studies out there from some of the world’s most successful companies. Returning to the example of Proficy above, companies like Procter & Gamble, McNeil, Akzo Nobel, and Volvo have successfully implemented GE Digital's Proficy MES solution to drive operational excellence, improve productivity, enhance product quality, and achieve cost savings.
These implementations highlight the potential benefits of adopting an MES solution like Proficy in terms of optimizing production processes, achieving regulatory compliance, and gaining real-time visibility and control over manufacturing operations. In the first half of the article, I mentioned that the time to implement and cost is often a barrier for smaller and medium sized companies. Yet many of the world’s largest companies, those that can afford the higher costs of building their own system, repeatedly return to the tried and tested systems that are already available.
Finally, we have detailed analysis from independent consulting firms like Gartner informing us about the capabilities of different products on the market and ranking them accordingly. The Gartner Magic Quadrant for Manufacturing Execution Systems Report and Critical Capabilities Report provides a wealth of information and insight into what other users think and which product is right for you. You might have noticed my bias toward Proficy, so don’t take my word for it – check out what independent analysts are saying.
The debate over whether to build or buy an MES is often a contentious one. This is because most of the participants in the debate have a commercial interest underlying their position. Each manufacturer needs to make the decision that is right for them, but COTS can generally deliver a solution in a quicker time, and at a lower cost, when compared with building a new system from scratch. Even companies that can afford the higher costs of building their own system repeatedly return to the tried and tested systems that have been proven to work time and again.
Novotek helps industrial firms adopting advanced automation, IoT technologies and smart factory solutions. To find out more, Irish customers can visit novotek.ie and UK customers can visit novotek.co.uk
Comments (0)
This post does not have any comments. Be the first to leave a comment below.
Featured Product
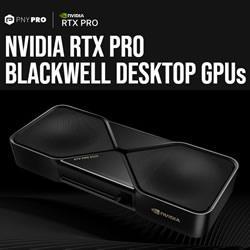