What are the Best Parts of a Manufacturing Plant to Automate?
Manufacturing automation is transforming the industry today, leaving many manufacturing professionals wondering how they can get started or add to their current automated systems. Identifying manufacturing processes that need automation in any plant is all about matching challenges and solutions.
Automation is the perfect tool for driving efficiency, productivity, and quality control. It can help optimize manufacturing plants to get them running at peak productivity with top quality and minimized resource waste. Are you ready to identify the right areas in any plant for manufacturing automation?
Manufacturing Processes That Need Automation
The best parts of a manufacturing plant to automate are the areas that are running slowly or ineffectively. This will be different from one plant and niche to another, but there are some clear common indicators to look out for: excess time, excess materials, or insufficient personnel.
A simple example of this approach to manufacturing automation is a car manufacturing plant. The car manufacturing process usually follows the same general flow. The raw materials for the cars arrive at the plant, where they’re sorted and inspected. All of the different components of the car are produced separately, such as the doors, the engine, and the air conditioning system. They all get produced, welded, stamped, and painted then assembled onto the car’s chassis. Then the interior of the car is added. Finally, a completed car is rolled off the assembly line.
Virtually every single step of this process can be automated. Throwing automated systems at everything at once is not an effective approach to automation, though. Instead, managers should carefully analyze each step of the car manufacturing process.
This analysis will reveal where things need improvement. For instance, maybe the welding process is creating a bottleneck because the plant has a shortage of professional welders. This could potentially be fixed with some warehouse automation, specifically welding robots.
Tips for Deciding Where to Automate
The best parts of a manufacturing plant to automate are the weakest. Manufacturing processes that need automation are almost always those that are currently holding the plant back. This is a classic example of “only as strong as the weakest link”. Start automating manufacturing plants with the processes that need the most help.
Manufacturing plant managers will need to do some research and analysis on the current state of their plant before diving into any automation. Monitor every step of the manufacturing workflow. Collect data on how long each process takes and where materials are being used most. Check in with team leaders to see which teams are short staffed or working long hours. With all this information in mind, here are a few things to look out for.
Skill Gaps and Labor Shortages
The National Association of Manufacturers estimates that there will be 2.1 million unfilled jobs in the industry by 2030. Many manufacturers today are facing labor shortages, as well as serious skill shortages. There are numerous reasons for this – advancing technology, waves of retiring workers, a lack of new young hires.
Regardless of the cause, labor and skill shortages often present key opportunities for manufacturing automation. Even if employees are working at peak productivity, they won’t be able to keep up if they don’t have enough help. Overworking employees will only worsen low productivity, as well.
If skill gaps and labor shortages are an issue, collaborative robots could be a great automation solution. These are robots that are designed to work alongside humans safely. Adding this type of robot to processes that are short staffed can help fill gaps left by labor shortages.
For instance, a plant manager at a car manufacturing plant might realize that raw materials inspection is taking longer than expected. On further inspection, the manager learns that the raw materials team is running on half the necessary staff. The plant manager could get courier robots to make the raw materials inspection process operate more efficiently.
The robots would retrieve and shuttle raw materials between employees, saving them the time and effort of running all over the materials storage area. This allows a small team to work like a big team, simply by making every employee’s job a little easier with automation.
High Error Rates
Another key indicator of manufacturing processes that need automation is high error rates. For instance, a plant manager might notice that their packaging process is operating slower than average and using much more plastic and cardboard than estimated. These high error and waste rates are red flags that result in money wasted on excess energy and materials, challenges that automation could resolve.
Semi-automated or even fully automatic machines provide an efficiency boost and help ensure that at least one part of the packaging process will be more consistently accurate. Plus, the more efficient strapping systems will use less power and emissions, helping to resolve the energy waste challenge.
Next, the plant manager could add pick and place robots to the packaging department. The robots will autonomously pack units into their boxes and send the boxes through an automated taping or sealing machine.
Now the packaging department has a more accurate sealing device and automated unit packing. All employees need to worry about is quality control inspections on the finished, packaged products.
Process Bottlenecks
A red flag for manufacturing processes that need automation is bottlenecks. In any manufacturing plant, bottlenecks can derail an entire production facility. The processes before the bottleneck get backed up with excess units and the processes afterward are wasting time waiting for new units. Every unit takes more time and money to get off the assembly line.
Bottlenecks indicate an inefficiency in the manufacturing process, which is exactly the kind of challenge that manufacturing automation is designed to solve. Robots and robotic machinery can perform the exact same task innumerable times without diminishing returns, declining focus, or quality inconsistency. This leads to higher production efficiency.
Lean manufacturing coupled with automation can turn bottlenecks into the most streamlined, optimized processes in the whole manufacturing plant. The lean manufacturing approach already focuses on reducing time spent on each task. Automation can take this to the next level by reducing the number of manual tasks in the plant. With robotic technology assigned to bottlenecked processes, there will be a much lower likelihood of errors and delays slowing down the process.
Innovating With Manufacturing Automation
Manufacturing automation is sweeping the industry today. There is never a bad time to begin adding automation technology. The best way to get started is to closely analyze performance throughout the entire manufacturing plant. A thorough analysis will reveal which teams are struggling, which processes are trailing behind, and where resources are being wasted.
These are not failures – they are opportunities for innovation. Plant managers can use automation to strengthen their manufacturing processes. Through improved efficiency, accuracy, and quality, manufacturing automation can turn any plant into a powerhouse of productivity and industry-leading quality.
Comments (0)
This post does not have any comments. Be the first to leave a comment below.
Featured Product
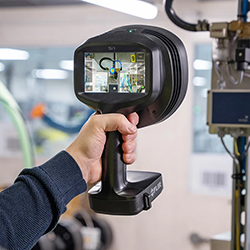