Mistakes are sent packing - Autonomous Machine Vision improves accuracy while reducing costs
According to the World Allergy Organisation (WAO), 2.5 per cent of the general population is allergic to one of more foods, while up to 10 per cent can manifest adverse drug reactions. This is just one example of why in highly regulated industries, such as food or pharmaceutical manufacturing, it is particularly important to protect consumers by ensuring that items are properly packaged and labelled. Here Zohar Kantor, VP of sales and project management at Inspekto, explains how Autonomous Machine Vision can help provide an extra layer of protection.
Packaging and labels contain key information on food products and drugs. A minor mistake on either could have serious repercussions that impact a product’s safety, regulatory compliance and consumers’ satisfaction.
Errors in packaging are often the cause of huge recalls — the wrong label on the wrong product, for example, could lead to food containing ingredients that it shouldn’t, with dangerous consequences for consumers that are allergic. Other risks linked to incorrect packaging and labelling are premature spoiling, contamination with externals pollutants and changes in the product’s taste and colour.
For these reasons, quality assurance (QA) must be an integral part of the packaging process. Yet the huge amount of stock keeping units (SKUs) and different labeling concepts, make quality assurance in packaging a task even more challenging than in other sectors.
Machine vision solutions can automate QA procedures, but their inherent complexity, coupled with the high number of SKUs and inspection scenarios, often prevents small and medium packaging plants from implementing them.
Worsening the problem, companies usually need the assistance of a systems integrator or machine vision expert to build and set up the solution. For many SMEs, the cost of these services, together with the initial investment in a traditional machine vision solution, are far too high.
As a consequence, many small to medium sized packaging manufacturers rely on manual inspection, a method that carries an error rate of more than 25 per cent. In the context of Industry 4.0, this is an anachronistic approach that cannot be relied on.
Autonomous Machine Vision for QA and traceability
The introduction of Autonomous Machine Vision (AMV) by Inspekto, a German start up with Israeli DNA, gives manufacturers of every size peace of mind that their products are packaged and labelled correctly.
AMV constitutes a whole new category in the world of visual QA, since it provides users with universal inspection products that are completely autonomous—self-setting, self-learning and self-adjusting. Consequently, the plant’s personnel will be able to independently set up and operate the system, which comes ready to use, out of the box, like a laptop or a smartphone.
The first AMV system on the market, the INSPEKTO S70, has a number of characteristics that differentiate it from traditional QA solutions. Firstly, traditional solutions are tailor-made to inspect only one product at a specific junction of a production line and are designed and tested by a systems integrator to recognise all possible defects in a product.
In packaging, this means exposing the QA solution to thousands of defective items, until it memorises every potential production mistake, from missing labels, to misspelling, to unsealed or partially sealed packaging. This process of developing and training can take several weeks, causing extended periods of downtime.
On the other hand, the INSPEKTO S70 can be installed in only 30 minutes by any plant employee while production is running as normal. The user simply traces the perimeter of the area to be inspected and presents to the system an average of 20 to 30 good sample item, such as correctly printed and placed labels and integral packaging, and no defective items. The system, thanks to an array of AI engines working in tandem, automatically learns what the end-product should look like and alerts the QA manager if it detects any variation.
In short, Autonomous Machine Vision systems invert the parameters of traditional machine vision for QA — instead of learning what every single defect looks like, they learn what a perfect product looks like and flag up abnormalities.
Autonomous Machine Vision systems are already installed in the Leicester plant of a multinational food, snack and beverage corporation, where they are used to check that packaging is properly sealed and that labels are correctly attached and readable. The plant is planning to use the systems for other types of fast-moving consumer goods, to inspect the integrity of the packaging material and the correct placement of labels.
The consequences for labelling and packaging
The INSPEKTO S70 cannot perform optical character recognition (OCR) and read text yet, but can compare the inspected label to images of a perfect label that it has previously memorised.
Therefore, it can detect whether a label is incorrect, poorly printed, not securely attached, misplaced or missing altogether, and can also verify the physical integrity of the packaging material to make sure that the quality of products has not been compromised.
Environmental changes, such as changing in lighting and product orientation, are not a problem for the system, which only flags up actual defects. The highly reflective properties of some packaging materials are therefore not an issue, because the system will self-adapt its camera parameters to ensure that a clear image of the product will be taken, with no human intervention. Additionally, the system archives pictures of the inspected items, so that the manufacturer can respond to any claims and prove that items left the facility in perfect condition.
Available at one tenth of the price of a traditional QA solution, and with no complex integration requirements, Autonomous Machine Vision systems provide packaging facilities of every size a reliable alternative to manual quality inspection. This means that employees can be freed from tedious, repetitive manual inspection tasks and moved into more productive roles that add value to the production line.
The affordability, simplicity and speed of installation of Autonomous Machine Vision systems also mean that manufacturers can have several QA stations, instead of just one at the end of the production line, a concept that Inspekto calls Total QA. Over time, Total QA allows manufacturers to spot areas where mistakes happen more frequently and optimise the production line.
Food allergies and drug intolerances are becoming increasingly publicised and regulatory compliance to labelling and packing guidelines is essential to guarantee consumers’ safety. Thanks to Autonomous Machine Vision, packaging manufacturers of every size now have an extra asset to improve their products’ quality.
For more information and to request a free demonstration on your production line, visit www.inspekto.com.
About Inspekto: Inspekto is a German industrial company with Israeli DNA. Backed by leading industrial businesses from across the DACH region, the start-up is out to reinvent the vision inspection sector, introducing the first powerful entries into the new Autonomous Machine Category.
Inspekto Autonomous Machine Vision systems are designed to put the Machine Vision market on a one-way course, replacing existing integrator-centric solutions by ready-to-go out-of-the-box QA systems put at the very hands of the industrial plant QA manager. The systems are driven by Plug & Inspect™, the first expert-free technology for visual quality inspection, gating and sorting, which eliminates the costly integration and customised developments that characterised traditional machine vision technology.
Comments (0)
This post does not have any comments. Be the first to leave a comment below.
Featured Product
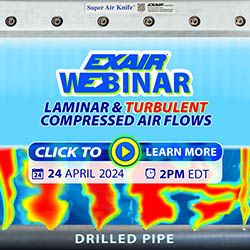